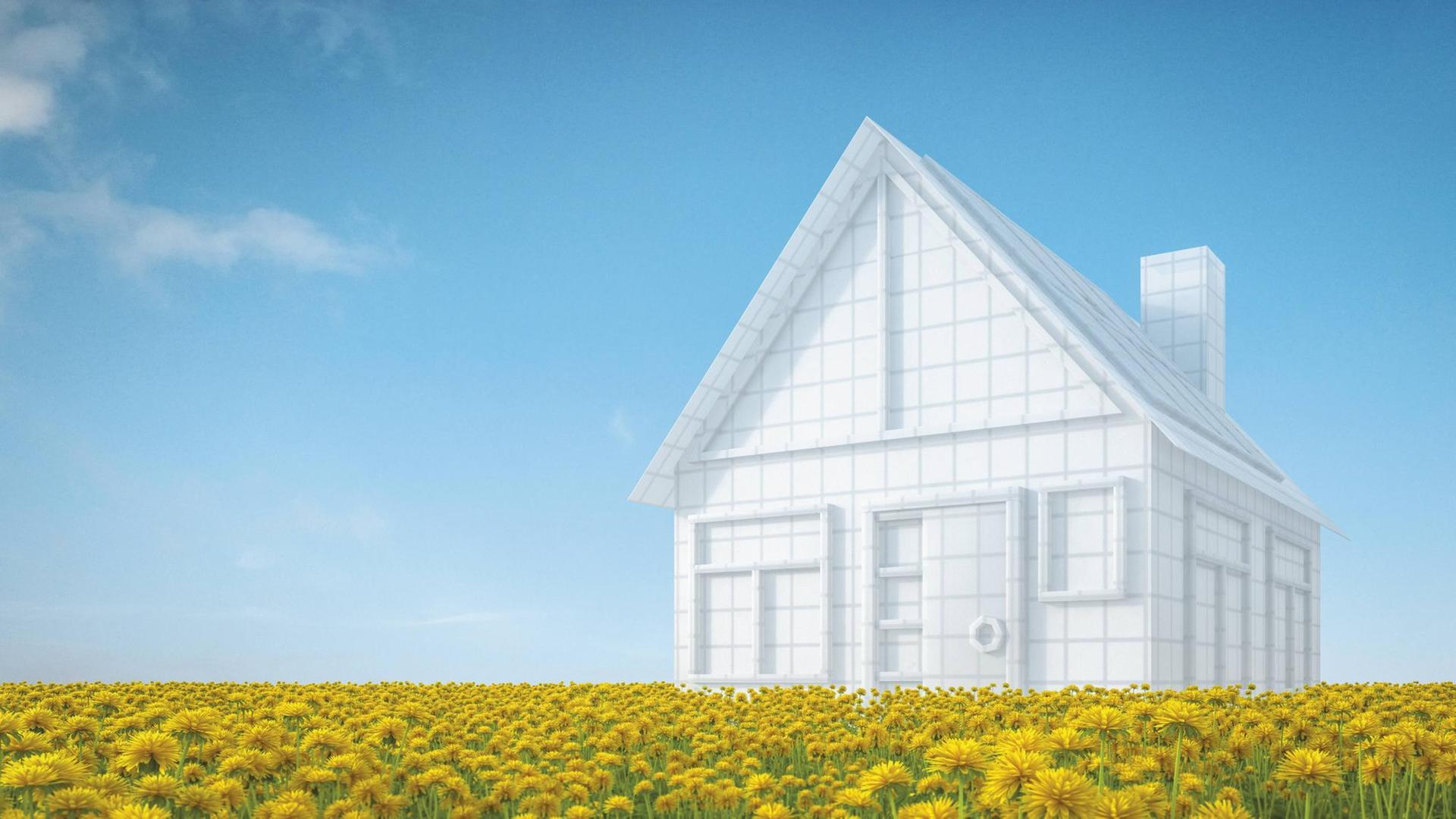
Der Druckkopf zieht seine geschwungene Bahn. Hinterlässt auf der Metalloberfläche eine feine, weiße Spur. Dann hebt er sich kurz nach oben, fährt an eine andere Stelle und führt seine Bewegung fort. Ein 3D-Drucker, der Schicht für Schicht ein Objekt aus Plastik aufbaut. Günstige Geräte für den Hobbykeller sind bereits für einige Hundert Euro zu bekommen. Profi-Geräte kosten gut und gerne einige Zehntausend Euro. Additive Fertigung nennt sich das dann, weil der Werkstoff in Schichten hinzugefügt wird, erklärt Klaudius Henke.
"In vielen Branchen hat sich die additive Fertigung bereits als Stand der Technik durchsetzen können. Ein gutes Beispiel ist zum Beispiel Medizintechnik, wo man auf der Basis eines Scans des Patienten einen Knochen nachmodellieren kann und dann zum Beispiel ein Hüftimplantat patientenspezifisch drucken kann."
Und nun erobert der 3D-Druck auch allmählich das Bauwesen. Fassadenschmuck, Wandelemente oder gar ganze Häuser. Auch hier eröffnet diese Technologie ganz neue Möglichkeiten - und vielleicht ist es mit der Schichtbauweise sogar möglich, Gebäude auf dem Mond zu errichten oder auf dem Mars.
Die Technik dahinter: Selektives Binden
"Im Bauwesen haben wir genau diese Situation, dass wir einmal fast immer Einzelfertigung haben. Jedes Gebäude sieht anders aus; schon allein deswegen, weil ich mich immer auf ein anderes Baugrundstück einlassen muss. Und zum anderen habe ich auch oft komplexe Objekte. Und deshalb passen eigentlich additive Fertigung und das Bauwesen sehr gut zusammen. Es gibt ja bereits Beispiele zum Beispiel in China, in Peking, wo man ein ganzes zweigeschossiges Gebäude auf der Baustelle gedruckt hat. Allerdings wäre diese Bauweise, wie wir es dort sehen, in Deutschland oder in Europa auch nicht einsetzbar, weil zum Beispiel die Dämmung noch komplett fehlt."
Klaudius Henke ist Architekt. An der Technischen Universität München entwickelt er 3D-Druckverfahren, mit denen sich nahezu beliebig geformte Bauteile aus Beton herstellen lassen. "Selektives Binden" nennt sich eines dieser Verfahren. Wie das funktioniert? Dazu müssen wir uns nach unten in den Keller des Nebengebäudes begeben. Dort erwartet uns in einem fensterlosen Raum schon Daniel Talke. Der Doktorand schraubt gerade an einem Metallgestell, das dem Rahmen eines Himmelbetts ähnelt.
"Das ist unser erstes Versuchsgerät, um Zementschichten selektiv mit Wasser zu binden."
Im Inneren des Metallgestells steht eine Plattform, eingerahmt von vier Wänden.
"Was wir hier tun, ist: feine Zementschichten auf einer Bauplattform ausbringen und diese dann ganz selektiv mit speziellen Düsen mit Wasser beträufeln. Zunächst wird eine Schicht Zement ausgebracht. Dann wird das Wasser eingetragen, wo wir es benötigen. Dann kommt wieder eine Schicht Zement, wieder Wasser, wieder Zement, wieder Wasser. Und nur an den Stellen, wo das Wasser tatsächlich ankommt, wird der Körper gefestigt."
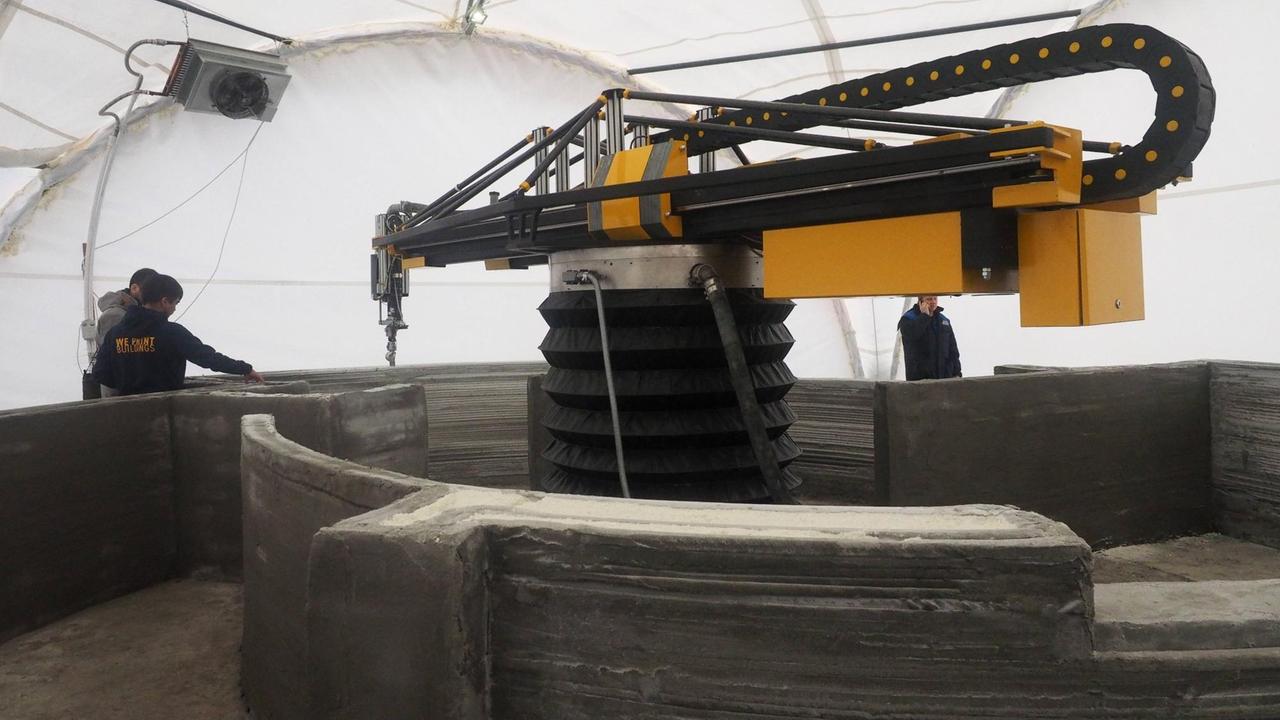
Weil die Betonschüttung allmählich wächst, fahren gleichzeitig die vier Wände einer Gleitschalung Millimeter um Millimeter nach oben.
"Am Schluss haben wir dann einen komplett gefüllten Bauraum, den wir von dem losen Material befreien müssen. Am Ende haben wir unser komplettes 3D-Modell in Beton da."
Die Maschine erinnert mich an 3D-Drucker, die nach dem Binder Jetting-Verfahren arbeiten. Damit lassen sich zum Beispiel Objekte aus Kunststoff oder auch Metall herstellen.
"Die Besonderheit bei uns ist, dass das noch niemand in Zement gemacht hat. Zement ist ein sehr komplizierter Baustoff, um ihn in feinen Schichten auszubringen, weil er gerne Klumpen bildet und dadurch keine feine Schicht herstellen lässt. Wir haben dafür einen speziellen Dispenser entwickelt, damit wir unsere 1-Millimeter-Schichten Zement sehr schön herstellen können."
Bleibt nur noch eine Frage: Welchem Zweck dient das glänzende, stromlinienförmige Gerät in Schwarz und Blau, das in der hintersten Ecke des Raumes steht?
"Das ist unser neuer Staubsauger. Das ist ganz wichtig für unsere 3D-Druck-Geschichten. Wir arbeiten hier mit Zementstaub, und ein guter Staubsauger ist da wirklich wichtig."
Die Natur als Vorbild
Ein Vorteil des 3D-Drucks von Betonteilen besteht darin, dass man teures Baumaterial einsparen kann. Wie solch ein Objekt aussehen kann, zeigt Klaudius Henke in seinem Großraumbüro. Auf einem Regal steht dort ein Betonklotz in der Größe eines Hohlblocks. Seine Struktur erinnert aber eher an einen Schwamm oder an das engmaschige Gerüst im Inneren eines Knochens.
"Was wir hier sehen, ist ein Ausschnitt aus einer formoptimierten Stütze. Da wurde ein Computerprogramm verwendet, was aus einer Stütze virtuell am Computer eben an den Stellen Material entfernt, wo es zum Tragen nichts beiträgt. Und stehen bleibt dann eben tatsächlich nur das Material, was auch trägt. Und dadurch entstehen diese filigranen Zellstrukturen. Und Sie sehen: Zum Rand hin wird es dichter, weil da mehr Last abgetragen werden muss. Und im Inneren wird es dann luftiger."
Die Form folgt in diesem Fall der Kraft. Und dann deutet Henke auf ein zweites Objekt, ein graues Rohr mit einer rauen Oberfläche. Im Inneren verlaufen Betonstreben von einer Seite auf die andere.
"Das soll eine Stützstruktur darstellen, ein Rohr mit inneren Verstrebungen. Da war ein wenig die Vorlage ein Vogelknochen. Vögel haben in ihren Flügeln Röhrenknochen, die sehr leicht und trotzdem sehr stabil sind. Und das ist in der Natur dadurch realisiert, dass in der Röhre eben noch solche Verstrebungen drin sind. Und dadurch wird die stabilisiert. Und hier haben wir das mal abstrakt nachgebildet aus Beton."
Die Ingenieure aus München arbeiten neben dem selektiven Binden auch noch an einem anderen 3D-Druck-Verfahren, am Extrusionsverfahren. Dabei verarbeiten sie bereits fertig gemischten Beton, der im flüssigen Zustand aus einer Düse gepresst wird – so wie man Zahnpasta aus einer Tube drückt. Ein Roboterarm führt die Düse so, dass sich aus den Mörtelsträngen dreidimensionale Objekte aufschichten lassen. Auch solch ein Bauelement steht auf dem Regal: Ein Klotz mit wabenförmigen Zellen in seinem Inneren.
"Da wo die Zellen groß sind, habe ich eine gute Wärmedämmung. Weil Luft ein schlechterer Wärmeleiter ist als dieser Beton. Und dort wo die Zellen klein sind, habe ich mehr Material, eine höhere Dichte und dadurch eine bessere Tragfähigkeit."
"Ein entscheidender Schritt auf dem Weg zur Industrie 4.0"
Auch andere Forschergruppen und Firmen arbeiten daran, dieses Extrusionsverfahren auf die Baustelle zu bringen. Apis Cor zum Beispiel ist ein Start-up-Unternehmen mit Sitz in San Francisco, Moskau und Irkutsk. Mithilfe eines Roboterarms, der sich um 360 Grad drehen kann, haben die Mitarbeiter innerhalb von nur 24 Stunden ein Haus auf einer Fläche von knapp 40 Quadratmetern errichtet. Kosten soll es nicht mehr als 10 000 US-Dollar. In Katastrophengebieten könnten mit diesen 3D-Druckern in kürzester Zeit Notunterkünfte entstehen. Ein weiteres Projekt dieser Art ist CONPrint3D an der Technischen Universität Dresden. Das Besondere hier: Eine mobile Betonpumpe soll zum 3D-Drucker aufgerüstet werden. Der Ausleger der Pumpe dient als Roboterarm, der Schicht für Schicht ganze Wände hochziehen kann. Geleitet wird das Projekt von Viktor Mechtcherine. All diese Verfahren sind attraktiv, sagt er, weil man so komplex und individuell bauen kann für wenig Geld - und in kurzer Zeit.
Arndt Reuning: "Bleiben wir doch einfach mal bei der Zeit. Warum sind diese Techniken so sehr viel schneller als das konventionelle Bauen?"
Viktor Mechtcherine: "Also, ich kann hier direkt aus digitalen Bauplänen eine Herstellung herbeiführen. Ich brauche keine Schalung, ich führe einfach die Düse nach den Vorgaben. Und dann entsteht ein Bauwerk genauso, wie ich das digital geplant habe."
Reuning: "Das heißt, die Daten sind sowieso vorhanden aus der Planung und müssen dann nur noch quasi wie im 3D-Drucker, den man vielleicht auch zu Hause stehen hat, umgesetzt werden?"
Mechtcherine: "So ist es."
Reuning: "Wie sieht es aus: Schont denn dieses Verfahren auch Ressourcen?"
Mechtcherine: "Ja, also, ich habe bereits angesprochen, dass wir die Schalung nicht mehr brauchen. Wir können auch so viel Material verbauen wie tatsächlich auch benötigt wird. Das heißt, wir haben keine Reste des Materials und wir können auch Geometrien herstellen, die mit anderen Verfahren nicht herstellbar sind. Und wir können dieses Prinzip 'Die Form folgt der Kraft' auch komplett umsetzen."
Reuning: "Sie sagen: neue Formen. Sind denn auch neuartige Materialien und Werkstoffe vielleicht möglich, mit denen man dann druckt?"
Mechtcherine: "Derzeit müssen wir auch neue Materialien einsetzen, das heißt, neue Betonarten. Aber man kann auch mit dem herkömmlichen Beton oder Beton, welcher sehr ähnlich dem herkömmlichen Beton ist, auch bauen."
Reuning: "Welche neuen Betonarten sind das denn?"
Mechtcherine: "Es geht hier um die Anpassung der Verformbarkeit des Materials. Also ich muss dieses Material fördern erstmal an den Druckkopf, also durch Pumpen. Ich muss das Material ablegen durch Extrusion. Ich muss dann eine Schicht nach der anderen aufbauen mit einem guten Verbund das Ganze auch gewährleisten. Und dafür brauche ich besondere Betonqualitäten. Also, es ist relativ einfach, Material nur zu pumpen. Oder es gelingt auch relativ einfach, das Material durch die Extrusion abzulegen. Aber gleichzeitig zu pumpen und abzulegen das Material, so dass es nicht zerfließt und dass man auch eine weitere Schicht aufbringen kann, das ist eine Herausforderung, und das können wir inzwischen."
Reuning: "Ich nehme an, der Mörtel muss dann auch entsprechend schnell härten."
Mechtcherine: "So ist es, das ist der nächste Punkt. Und auch hier brauchen wir besondere Eigenschaften. Das Material muss schnell an der Festigkeit gewinnen, aber gleichzeitig darf dadurch der Verbund zu den vorangegangenen Schichten nicht leiden."
Reuning: "Neue Materialien ermöglichen dann ja vielleicht auch ganz neuartige Gestaltungsmöglichkeiten. Können Sie da vielleicht ein Beispiel geben, was alles möglich ist?"
Mechtcherine: "Letztendlich sind wir hier unbeschränkt, also es gibt keine Einschränkung in Bezug auf die Formgestaltung. Also ganz auch verrückte Formen, die ich für, sagen wir, Kunst am Bau benötige, also die einem Künstler, einem Bildhauer vielleicht einfallen und die er dann vielleicht auch digital umsetzen kann in Beton."
Reuning: "Wie sehen Sie denn die Situation in Deutschland? Wie steht Deutschland, wenn es um diesen 3D-Druck geht, im internationalen Vergleich da?"
Mechtcherine: "Ja, im Bereich der Forschung sind wir weltweit in der ersten Reihe, nicht jedoch bei der praktischen Umsetzung. Da gibt es derzeit andere, die den Ton angeben, zum Beispiel China. Auch in Europa gibt es bereits erste realisierte Projekte: eine Fußgängerbrücke in Spanien und eine Fahrradbrücke in den Niederlanden. Das Interesse der deutschen Industrie ist aber groß an solchen additiven Verfahren. Die Entwicklung additiver Fertigungsverfahren zur Herstellung von Betonbauteilen ist ein entscheidender Schritt auf dem Weg zur Einführung der Industrie 4.0 ins Bauwesen, nämlich von der bereits existierenden digitalen Planung bis hin zur digitalen Fertigung."
"Die Ressourcen vor Ort nutzen" - auch im Weltall
Bauen, was man will, schnell und für weniger Geld, mit Plänen, die heute sowieso schon digital vorliegen. Das macht den 3D-Druck für das Bauwesen auf der Erde so spannend, sagt Viktor Mechtcherine von der TU Dresden. Und dabei hat er einen Aspekt noch nicht einmal genannt: Man könnte zukünftig auch bauen, wo man will. Und deshalb werfen wir jetzt einen Blick in die Zukunft - zusammen mit Donald Trump.
"We will establish a foundation for a mission to Mars and perhaps someday to many worlds beyond."
Sollten tatsächlich eines Tages Menschen wieder zum Mond fliegen - oder von dort sogar weiter bis zum Mars, wie es dem US-Präsidenten vorschwebt -, dann müsste dort für eine Unterkunft gesorgt sein. Der 3D-Druck könnte sich auch hier als nützlich erweisen. Über erste Konzepte denken zum Beispiel Experten der ESA nach, am Europäischen Astronautenzentrum EAC in Köln.
Das Labor von Aidan Cowley ist in einem Container neben dem Hauptgebäude untergebracht. Er greift nach einer Plastikflasche, die mit einem schwarzen Pulver gefüllt ist.
"In dieser Flasche befindet sich ein Material, das wir als Ersatz für Mondstaub verwenden, auch als Regolith bekannt. Die Zusammensetzung und die Korngröße stimmen genau mit dem Basalt-Sand überein, wie er auf der Mondoberfläche zu finden ist. Die Apollo-Missionen haben ja nur knapp 400 Kilo davon zur Erde gebracht. Für unsere Versuche wäre das Original viel zu teuer, daher verwenden wir diesen Ersatz."
Dieses Material will der Forscher als Baumaterial auf Mond und Mars nutzen. Dazu müsste es vor Ort zunächst einmal geschmolzen werden.
"Dafür gibt es verschiedene Möglichkeiten. Zum Beispiel mit Mikrowellen. Die heizen das Eisen im Regolith auf, so dass das Material schmilzt. Der Mikrowellenofen, den wir hier benutzen, ist nicht gerade das Standardmodell aus der Küche. Aber er funktioniert nach genau demselben Prinzip. In der Küche versetzen die Mikrowellen Wassermoleküle in Bewegung. Wir arbeiten bei genau derselben Frequenz. Eine Laune der Natur will es so, dass auch der Mondstaub auf diese Frequenz reagiert."
Das Mikrowellengerät müsste auf dem Mond dann an einen Roboterarm oder einen Rover montiert sein. Seine Energie würde es aus Solarzellen beziehen. So könnte es den Regolith schmelzen, um daraus Fahrwege, Landeplätze und sogar Gebäude entstehen zu lassen. Eine neue Ära für den Mond. Oder den Mars.
"In der Vergangenheit haben wir auf unseren Reisen ins Weltall alles mitgebracht, was wir zum Überleben brauchten. Aber wenn wir nun weiter ins Sonnensystem vordringen wollen, müssen wir lernen, die Ressourcen vor Ort zu nutzen - wie die Forschungsreisenden, die früher den Atlantik oder Pazifik überquert haben. Wenn wir auf der Mondoberfläche bauen können, ermöglicht uns das längere und nachhaltigere Missionen."
"Das sind ambitionierte Pläne"
Dann greift Aidan Cowley nach dem Modell eines Gebäudekomplexes auf dem Mars. Es besteht aus drei kuppelartigen Gebäuden, die durch Gänge miteinander verbunden sind.
"Das ist ein Modell für unser Projekt LavaHive. Es stellt eine Marsbasis dar. Dabei möchten wir so viele Komponenten wie nur möglich von dem Raumschiff wiederverwenden. Zum Beispiel hier das Dach des Habitats, des Wohnraums der Astronauten. Das ist ursprünglich die Rückwand der Landeeinheit. Aber diese beiden Abschnitte hier, das Labor und die Andock-Station, dafür möchten wir den 3D-Druck verwenden. Wir hätten dann ein zentrales Gebäude, um das herum sich diese Untereinheiten anordnen."
Arndt Reuning: "Wie sieht denn die Technologie dahinter im Detail aus? Wie bauen Sie diese Wände auf?"
Aidan Cowley: "Bevor wir Menschen auf den Mars schicken, würden wir erst einmal ein paar kleine Rover dort absetzen. Die würden dann Regionen mit ausreichend Regolith ausfindig machen und das Material zum Bauplatz schaffen. Dann würden sie einen kleinen Kanal graben, der anschließend von einem anderen Rover mit dem geschmolzenen Regolith gefüllt wird. Wenn der wieder abgekühlt ist, kann dieser Prozess wiederholt werden. Und so entsteht Schicht um Schicht das Gebäude."
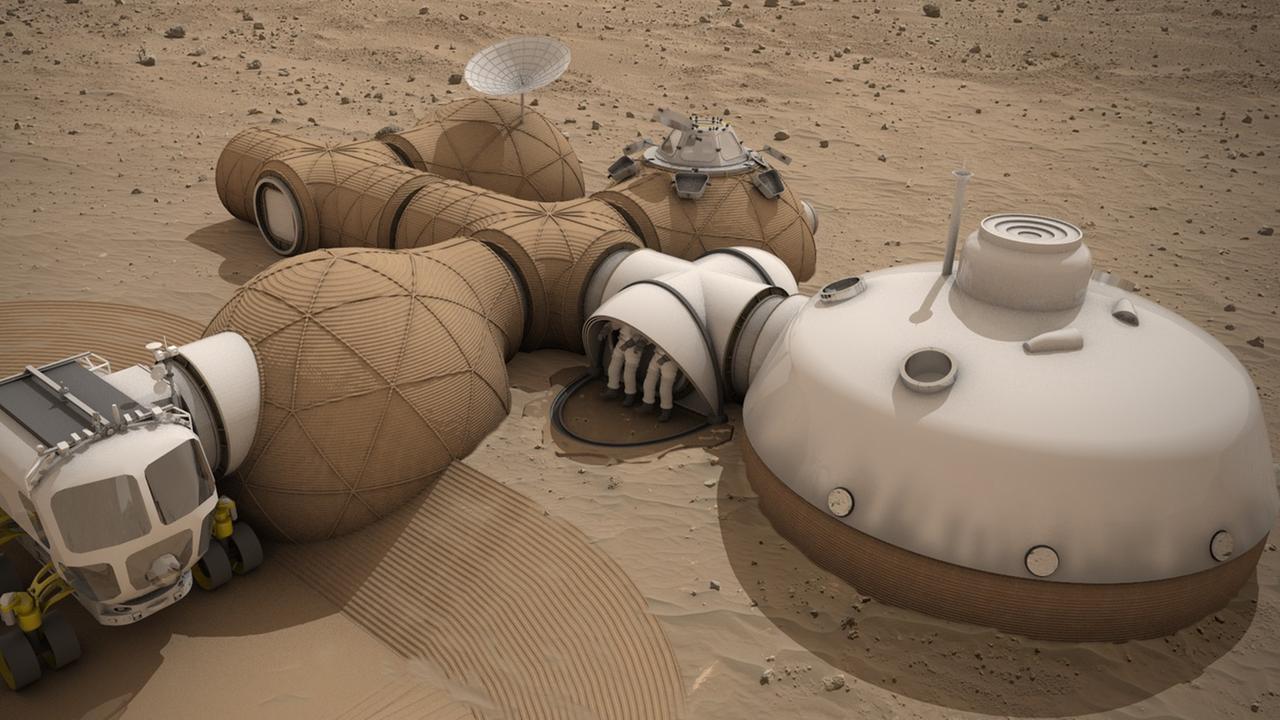
Reuning: "Wann ist es so weit? Wann wird gebaut?"
Cowley: "Das sind ambitionierte Pläne, die erst in weiter Zukunft verwirklicht werden können. Aber viele dieser Technologien existieren bereits hier auf der Erde. Etliche Firmen beschäftigen sich mit dem 3D-Druck von Häusern auf Basis von Beton. Jetzt geht es vor allem darum, die Verfahren an die harschen Bedingungen auf dem Mond oder dem Mars anzupassen. Aber es ist kein Ding der Unmöglichkeit."
Stahl schmelzen mit der Kraft der Sonne
Regolith lässt sich nicht nur mithilfe von Mikrowellen schmelzen. Auch Laser kommen infrage. Oder auch das konzentrierte Licht der Sonne. Das EAC befindet sich auf dem Gelände des Deutschen Zentrums für Luft- und Raumfahrt. Daher muss ich nicht weit laufen, um mich mit Hans-Gerd Dibowski zu treffen, der für den Sonnenofen am DLR zuständig ist.
Wir laufen vorbei an einem großen beweglichen Spiegel, dem Heliostat, dann zu einem großen Garagentor, das sich gerade öffnet. Es gibt den Blick frei auf eine Anordnung vieler kleiner Spiegel, die in sich gewölbt sind. Am Boden vor unseren Füßen ist eine gelbe Linie aufgemalt.
"Das Licht vom Heliostat ist noch nicht konzentriert. Das ist ein Planspiegel. Und erst ab dieser gelben Linie wird sozusagen die Reflexion zum Gebäude hin gelenkt. Und da würde man dann, wenn man da rumläuft, auch merken - man würde einen heißen Kopf bekommen -, dass man sich im Bereich konzentrierten Lichts befindet."
Dieses einstöckige Gebäude betreten wir nun. Über den Kontrollraum mit seinen vielen Computerbildschirmen gelangen wir in ein abgedunkeltes Labor. Eine Klappe in der Wand öffnet sich, und da sind sie wieder, die gewölbten Spiegel, vor denen wir gerade eben noch gestanden haben.
"Wir stehen jetzt hier in dem Experimentalbereich. Ein Bereich, wo das Experiment von der hochenergiereichen Strahlung dann bestrahlt wird. Und wir sehen gerade durch eine Öffnung im Gebäude auf den Konzentrator. Der Konzentrator besteht aus 159 sphärischen Spiegeln und bündelt das Licht von ungefähr fünfzig Quadratmetern auf die Größe eines Ein-Euro-Stücks."
Damit lassen sich Temperaturen von bis zu 2500 Grad Celsius erzeugen. Was auch immer in den Brennpunkt gerät, reagiert innerhalb kürzester Zeit.
"Also ob Sie jetzt Baustahl nehmen, Edelstähle, Keramiken - Sie sehen sofort eine Reaktion. Der Stahl schmilzt. Die Keramiken platzen. Sande schmelzen auf zu Glas, können also auch gesintert werden als Vorstufe zu der Verglasung. Also man sieht sofort eine starke Reaktion durch diese hohe Energiedichte."
"Wir können mittlerweile einen Stein von mehreren Zentimetern Dicke erzeugen"
Mit solch einem Sonnenofen möchten die Experten den Mondstaub zu festen Bausteinen zusammenbacken, und zwar vor Ort auf dem Erdtrabanten. Um damit Gebäude für Astronauten zu errichten. Im Prinzip ist dieser Sinter-Prozess machbar. Und zum Beweis zeigt mir Hans-Gerd Dibowski einen Tiegel mit Sand und einer glatten, glänzenden Scheibe darin.
"Was wir hier sehen, ist ein aufgeschmolzener Haufen Saharasand. Und es funktioniert sehr gut, also mit halber Leistung vom Sonnenofen können wir diesen Sand soweit durchstrahlen, durchschmelzen, dass er, wenn er wieder erkaltet, ein fester Baustein ist. Und die nächste Frage wäre jetzt im Grunde ingenieurmäßige Routine, daraus einen homogenen Baustein zu machen. Grundsätzlich geht es."
Regolight heißt das Projekt, in dem das Verfahren entwickelt wird. Nachdem innerhalb eines halben Tages klar war, dass die Temperaturen ausreichen, ging es anschließend darum, gezielt Bausteine herzustellen.
"Deswegen hatten wir in einem zweiten Schritt ein 3D-Druck-Verfahren entwickelt mit externen Partnern auch zusammen, wo dann Mineralschichten abgefahren werden mit einem Brennpunkt. Wenn diese eine Ebene aufgeschmolzen ist, wird eine zweite Schicht darüber gelegt, und so konnten wir mittlerweile einen Stein von mehreren Zentimetern Dicke erzeugen. Und weil das sehr zeitintensiv ist, haben wir das an dem Sonnensimulator gemacht, der aus zehn Xenon-Kurzbogenlampen besteht mit einer ähnlichen Leistung wie der Sonnenofen. Und damit konnte man sehr kontrollierte Bedingungen erzeugen und den Stein tatsächlich auch im ersten Anlauf herstellen."
Das Verfahren würde im Prinzip auch auf dem Mond funktionieren
Koordiniert wird das Projekt am DLR von Matthias Sperl vom Institut für Materialphysik im Weltraum. Mit ihm treffe ich mich am Sonnenofen, wo er mir erklärt, welche besonderen Herausforderungen es zu meistern gilt beim Häuserbau auf dem Mond.
Matthias Sperl: "Wie bei vielen Dingen, die wir auf dem Mond machen wollen und planen, ist eine der größten Herausforderungen der enorme Temperaturunterschied zwischen Tag und Nacht. Auf der Erde habe ich, wenn ich Beton anwenden will, habe ich einen Temperaturunterschied zu beachten von maximal +40 Grad Celsius und -40 Grad Celsius, ist also 80 Grad Unterschied. Auf dem Mond ist dieser gleiche Unterschied 300 Grad. Das heißt, was noch sehr heiß auf der Mondvorderseite durch die Sonne beschienen wird, wird am Ende wirklich sehr, sehr kalt. Und das führt zu großen Belastungen auf das Material. Deshalb kann man auch nicht immer mit Standardstrategien, wie wir sie hier auf der Erde gewohnt sind, ein Baumaterial optimieren."
Arndt Reuning: "Das heißt, was müssen Sie da dann verbessern?"
Sperl: "Ein Aspekt, wenn man unsere Strategie für die gesinterten Bauelemente mit Beton vergleicht: Wir vermeiden das Verwenden eines Bindemittels. Wir haben also keinen Zement und kein Wasser, weil wir befürchten, dass das auf der Mondoberfläche durch die Tag-Nacht-Unterschiede auf jeden Fall sehr schnell zerbröseln würde. Was wir produzieren, ist am Ende ein wirklicher Gesteinsziegel, der kein Bindematerial mehr braucht, sondern wir versuchen, die Bauelemente direkt miteinander zu verknüpfen und versuchen das dann auch mit jedem Schritt und jeder Addition eines neuen Ziegels in sich selber stabil zu gestalten."
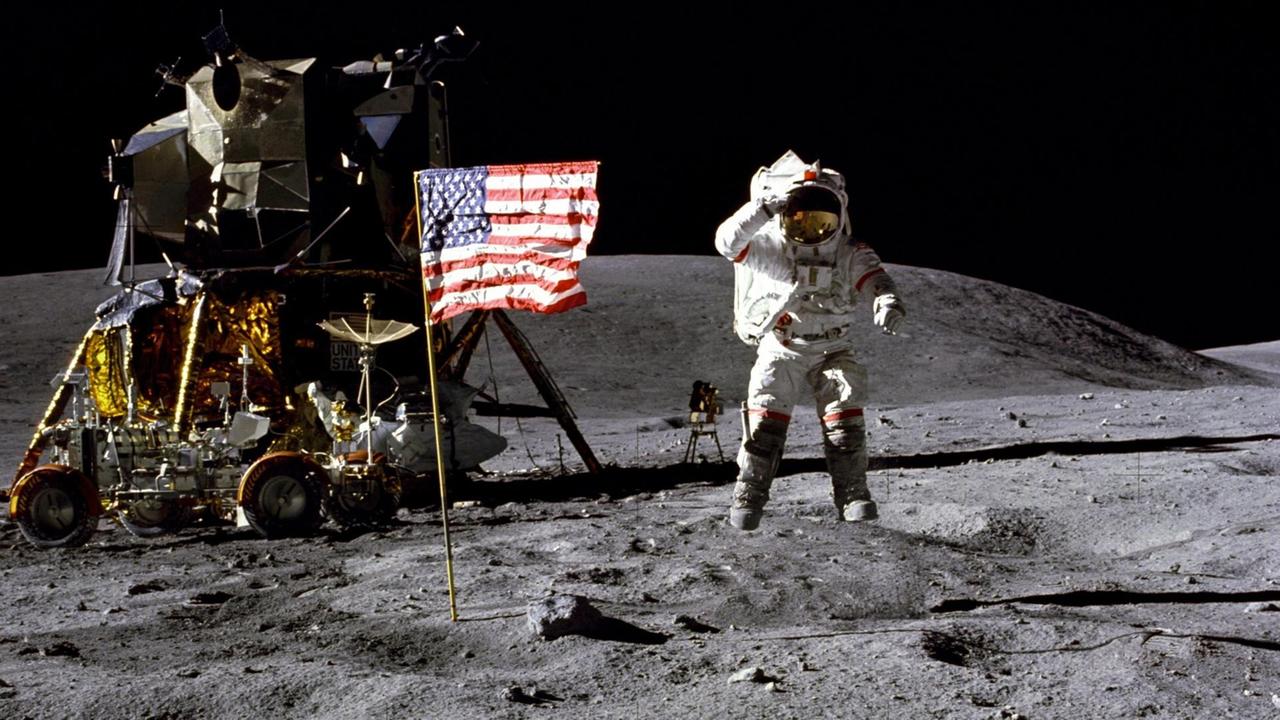
Und dann zieht Matthias Sperl eine Tüte mit kleinen, grauen Plastikbausteinen aus der Tasche.
Sperl: "Ich habe hier mitgebracht Modellbauteile im Maßstab 1:100 von Bauelementen, so wie wir sie uns vorstellen für ein Mondhabitat. Das sind Bausteine, die jetzt ähnlich funktionieren wie Lego. Man kann sie ineinanderstecken, und sie halten selbsttragend ihr eigenes Gewicht und das Gewicht der Bausteine obendrüber. Ich zeige Ihnen das mal hier. So, fällt jetzt hier auseinander, wenn man es nicht richtig macht. Wie gesagt: das ist im Maßstab 1:100. Auf dem Mond hat man noch den großen Vorteil: Die Bausteine wären auch sehr viel rauer und halten dann durch Reibung und durch diese Methode des sich gegenseitig Blockierens."
Reuning: "Könnte man dieses Verfahren eins zu eins auf den Mond übertragen?"
Sperl: "Das ist zunächst mal ein Verfahren, das im Prinzip so auch auf dem Mond funktionieren würde. Man würde es vielleicht mit einem kleineren Gebäude versuchen, um nicht vorher schon genügend Geld auszugeben, um sehr viel Material hochzubringen. Man kann sich vorstellen, das Ganze mit einem mobilen Rover und einer Linse zu machen, aber im Prinzip ist das Verfahren genauso, wie es auf dem Mond auch funktionieren würde."
Reuning: "Wie sieht es denn aus: Lässt sich denn diese Methode irgendwie auch für Anwendungen hier bei uns auf der Erde nutzen?"
Sperl: "Wir haben ein schönes Projekt gemacht, das sich darauf bezieht, dass ein Problem, das man am Anfang gar nicht für wahr halten würde, uns erzählt wurde: Wenn ich in der Wüste ein Gebäude bauen will, ist der Wüstensand, den man dort in rauen Mengen findet, gerade sehr schlecht geeignet, um so ein Gebäude aufzubauen. Der Sand ist sehr rund. Das ist schlecht, und es gibt auch mehrere andere Eigenschaften. Und wir haben mit ähnlichen Methoden mal Wüstensand genommen, diesen Sand, der schlecht geeignet ist, um Beton zu machen, im Sonnenofen so verändert, dass er sich besser eignet für Betonherstellung. Und das ist eine Methode, die auch funktioniert. Ob sie dann am Ende auch kommerziell umsetzbar ist, das wird die Zukunft dann zeigen."
Reuning: "Das heißt, Sie würden in dem Fall aber nur den Sand selbst verändern in seiner Struktur, in seiner Körnung, aber nicht den Sand zusammenschmelzen zu Bauelementen?"
Sperl: "Wir würden an der Stelle, wenn es um die Betonherstellung geht, den Sand nicht zu Bauelementen verschmelzen. Das wäre, glaube ich, für eine Anwendung auf der Erde, für die allerallermeisten Anwendungen, die man sich vorstellen kann, viel zu langwierig und damit zu teuer. Man kann aber Sandkörner anschmelzen und dann wieder aufbrechen. Und das führt auf jeden Fall zu einem Bausand, der sehr viel besser geeignet ist als der ursprüngliche Wüstensand."
Von der Erde zum Mond und zum Mars und wieder zur Erde zurück. Hier sind die ersten Gebäude im 3D-Druck bereits entstanden: Zum einen die Häuser der Firma Apis Cor südlich von Moskau. Aber auch in China sind bereits mehrstöckige Gebäude auf diese Weise gebaut worden. In den USA fasst der 3D-Druck gerade Fuß im Bauwesen. Saudi-Arabien zeigt sich hoch interessiert an der additiven Fertigung. Und die Vereinigten Arabischen Emirate haben einen Plan verabschiedet, nach dem bis zum Jahr 2030 jeder Neubau in Dubai zu einem Viertel auf 3D-Druck beruht. Dort soll sogar der erste Wolkenkratzer mithilfe dieser Technologie gen Himmel wachsen. Heißt das etwa, dass wir in Zukunft alle unsere Häuser nur noch ausdrucken werden, frage ich zum Schluss den Architekten Klaudius Henke. Er sagt:
"Nein, damit ist wohl nicht zu rechnen. Ich denke schon, dass die additive Fertigung das Bauwesen verändern wird. Aber man wird es dort einsetzen, wo ich wirklich auch einen Mehrwert habe. Und ich denke, dass wir eine Mischbauweise bekommen werden, wo additiv gefertigte Bauteile und konventionell gefertigte Bauteile zusammenspielen."