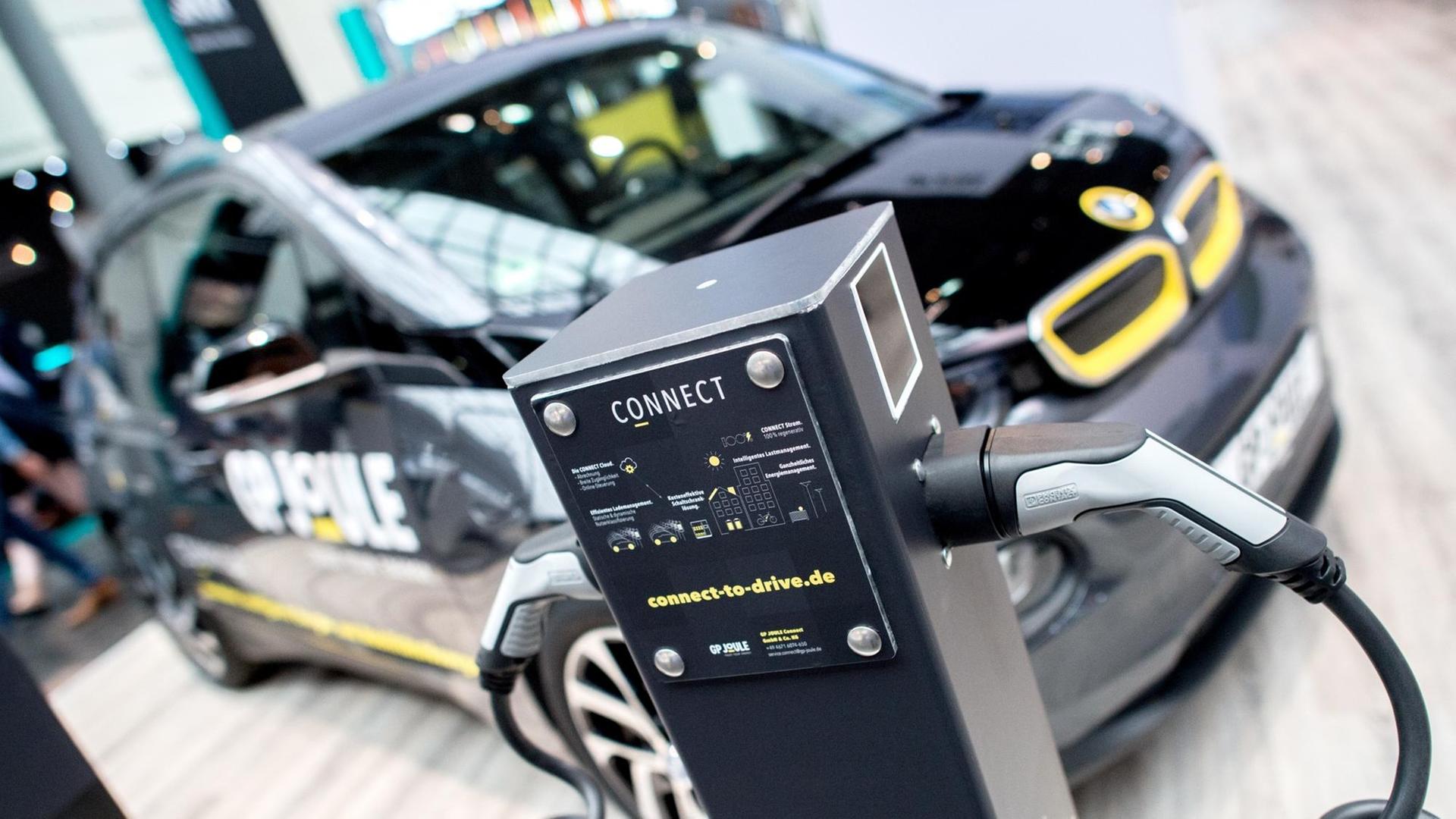
Eine Lithium-Ionen-Batteriezelle für Elektroautos ist ein kompaktes Energiebündel. Sie enthält viele unterschiedliche Bestandteile auf engstem Raum, erklärt Urs Peuker, Professor für Aufbereitungstechnik an der TU Bergakademie Freiberg.
„Da drin stecken zwei Elektroden. Das sind dünne Folien. Eine besteht aus Aluminium, eine aus Kupfer. Die sind umeinander gewickelt. Diese Folien sind beschichtet mit Aktivmaterial, das aus Nickel, Kobalt, Mangan bestehen kann – das ist die Aluminiumfolie. Und die Kupferfolie ist mit einem speziellen Graphit beschichtet. Jetzt haben wir schon mal vier Materialien. Dann kippen wir noch ein Lösungsmittel rein, das mit verschiedenen Chemikalien gemischt ist, die die elektrische Leistungsfähigkeit der Batterie verstärken.“
Die Trennung der Bauteile – eine Herausforderung
Diese bunte Mischung kann auf drei ganz verschiedenen Wegen voneinander getrennt werden. Entweder es wird einfach alles erhitzt, bis die Metalle schmelzen. Diese Schmelze wird dann aufgefangen, die Metalle weiter aufgearbeitet. So macht es die Firma Umicore in Antwerpen in Europas größter Anlage. Das Verfahren braucht aber viel Energie. Andere Betriebe zerkleinern die Batteriezellen deshalb mechanisch.
„Es gibt verschiedene Zerkleinerungsaggregate, landläufig vielleicht Schredder genannt, die unterschiedlich schnell laufen, unterschiedliche Werkzeuge haben. Und die kann man jetzt auf die Batterien anpassen. Wir müssen gucken, dass es die richtige Drehzahl hat, entsprechend lange in der Maschine bleibt, sodass wir genau das kriegen, was wir bei dem Zerkleinerungsprozess haben wollen. Und das ist auch die Aufgabe, die wir als Wissenschaftler entwickeln müssen.“
Wertvolle Metalle werden recycelt
Die Beschichtung der Elektroden fällt dabei als schwarze krümelige Masse an, die viel Nickel und Kobalt enthält. Beide Elemente sind nicht nur teuer, sondern auch knapp. Deshalb werden die schwarzen feinen Krümel von den geschredderten Metallfolien abgesiebt und anschließend ähnlich aufbereitet wie nickel- oder kobalthaltige Erze. Übrig bleibt das Elektrodenmaterial selbst. Gehäckselte Folien von Aluminium und Kupfer auseinander zu sortieren, ist aber nicht einfach. Urs Peuker:
„Wer jemals versucht hat, Lametta voneinander zu trennen – das ist eine Herausforderung. Wir sind dran, den Trick zu machen, was man zu Hause auch macht, die Aluminiumfolie einfach zu knüllen. Und die Kupferfolie auch zu knüllen. Dann haben wir wieder kompakte Teilchen. Und Kupfer ist deutlich dichter als Aluminium. Dann haben wir ein Trennmerkmal und können das trennen.“
Dieses Zerknüllen passiert beim letzten Zerkleinerungsschritt in einer sogenannten Hammermühle. Hier wird das Material zu Kugeln von einigen Millimetern Größe geschlagen. Durch Windsichten – so wie beim Dreschen von Getreide – erreichen die Forschenden schließlich, dass Aluminium und Kupfer immerhin zu 90 Prozent rein sind.
Wasser, Strom – dann knallt es
Einen ganz anderen, bisher noch experimentellen Weg gehen Wissenschaftler der Fraunhofer-Projektgruppe für Wertstoffkreisläufe in Hanau. Johannes Öhl packt die ganze Batteriezelle in einen Reaktor, so groß wie eine Waschmaschine, füllt den mit Wasser und legt Strom an. Dann knallt es, denn es entstehen:
„Schockwellen, die hervorgerufen werden bei der Entladung einer großen elektrischen Spannung. Die werden in dem Medium Wasser hervorgerufen und treffen auf die Batterien, die wir in dem Reaktor haben. Das Besondere dieser Schockwellen ist: Die greifen bevorzugt Schwachstellen der Materialien an. Das heißt, wir können damit verschiedene Materialien gezielt auseinander bringen.“
Die Technik ist bewährt, um Leiterplatten oder Photovoltaik-Module zu zerlegen. Lithium-Ionen-Batterien müssen die Forschenden aber rund tausend Mal mit einem Stromstoß behandeln, bis schließlich die schwarze Beschichtung ganz von den Elektrodenfolien abgelöst ist. Auch das braucht viel Energie. Und deshalb rechnet sich diese Trennmethode bis jetzt genauso wenig wie das Einschmelzen oder das Schreddern. Ob sich letztlich eines der Verfahren durchsetzen wird, das wird auch von der Wirtschaftlichkeit abhängen.