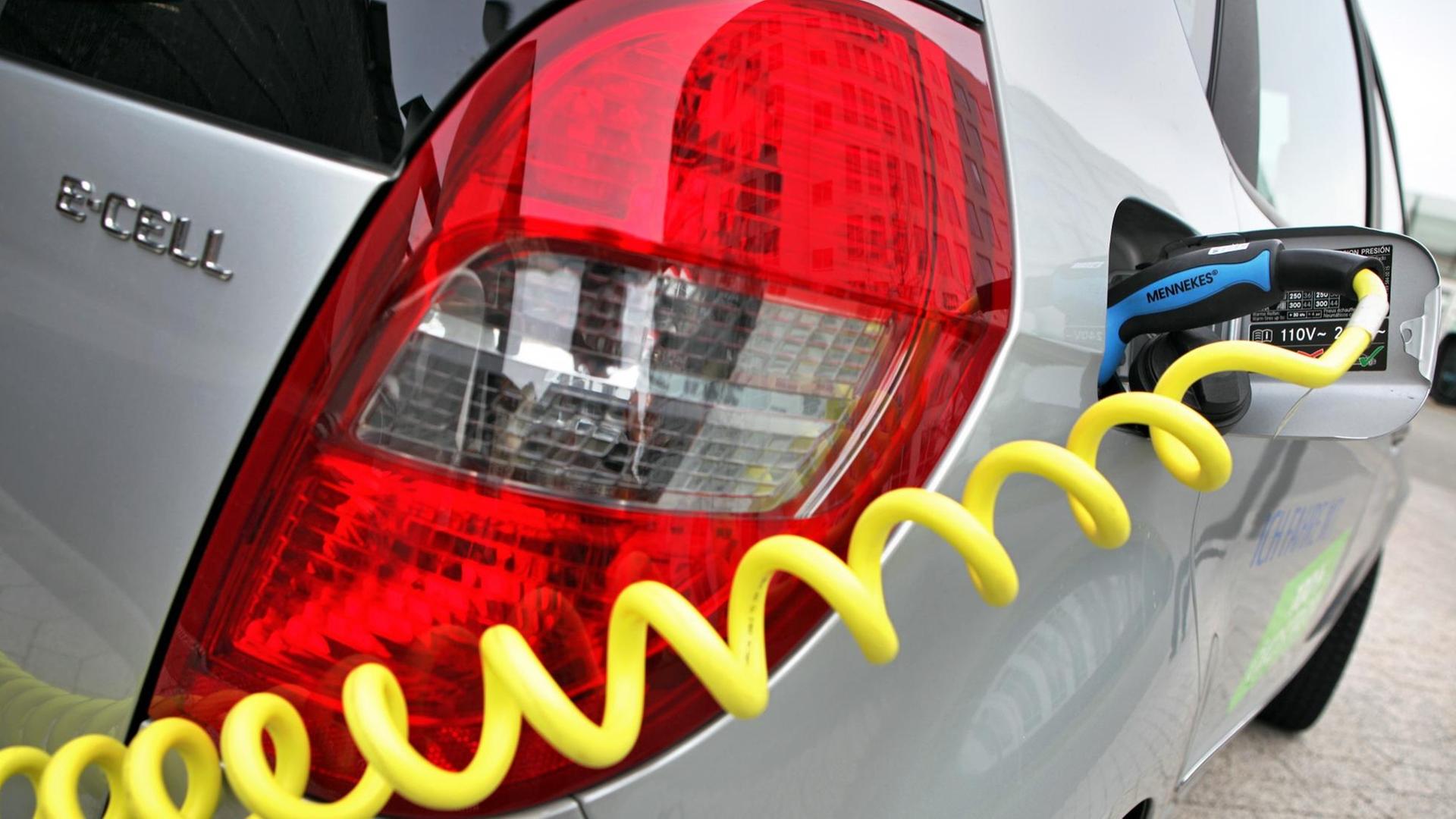
Wer mit einem Elektroauto unterwegs ist, dürfte die Situation kennen: Nervös behält das Auge die Batterieanzeige im Blick – und den Weg zur nächsten Ladesäule. Heute reicht, abhängig von Modell und Jahreszeit, mancher Akku keine 100 Kilometer, was den Aktionsradius des Elektroflitzers stark begrenzt.
Deshalb arbeiten Forscher verstärkt an einer neuen Generation von Batterien – an Akkus, die länger halten, sich schneller aufladen lassen und zudem günstiger und sicherer sind als die heutigen Modelle. Braucht es dafür ganz neue Ideen, quasi eine Revolution? Oder genügt es, an der bewährten Technik zu schrauben?
"Fahrkomfort sehr hoch, total geräuschlos. Beschleunigung ist sehr gut. Einfach sehr gut zu fahren."
Tuomo Hatakka ist der Chef von Vattenfall Deutschland, dem Energieversorger. Das Elektroauto hat er sich vor zwei Jahren zugelegt, seitdem legt er den Weg von seinem Haus in die Firmenzentrale gewöhnlich damit zurück. Flott, leise, komfortabel. Leider nicht ausdauernd: "Reichweite 120 Kilometer im Sommer. Etwa 90 Kilometer im Winter. Der Unterschied hat damit zu tun, dass die Heizung viel Batteriekapazität im Winter frisst."
Hattaka schaut aufs Armaturenbrett. Batterie fast leer, sagt die Anzeige. "Wenn das passiert, findet man eine Ladesäule und sorgt dafür, dass es wieder Batteriekapazität gibt fürs Elektrofahren." Er öffnet den Kofferraum und kramt das Ladekabel hervor.
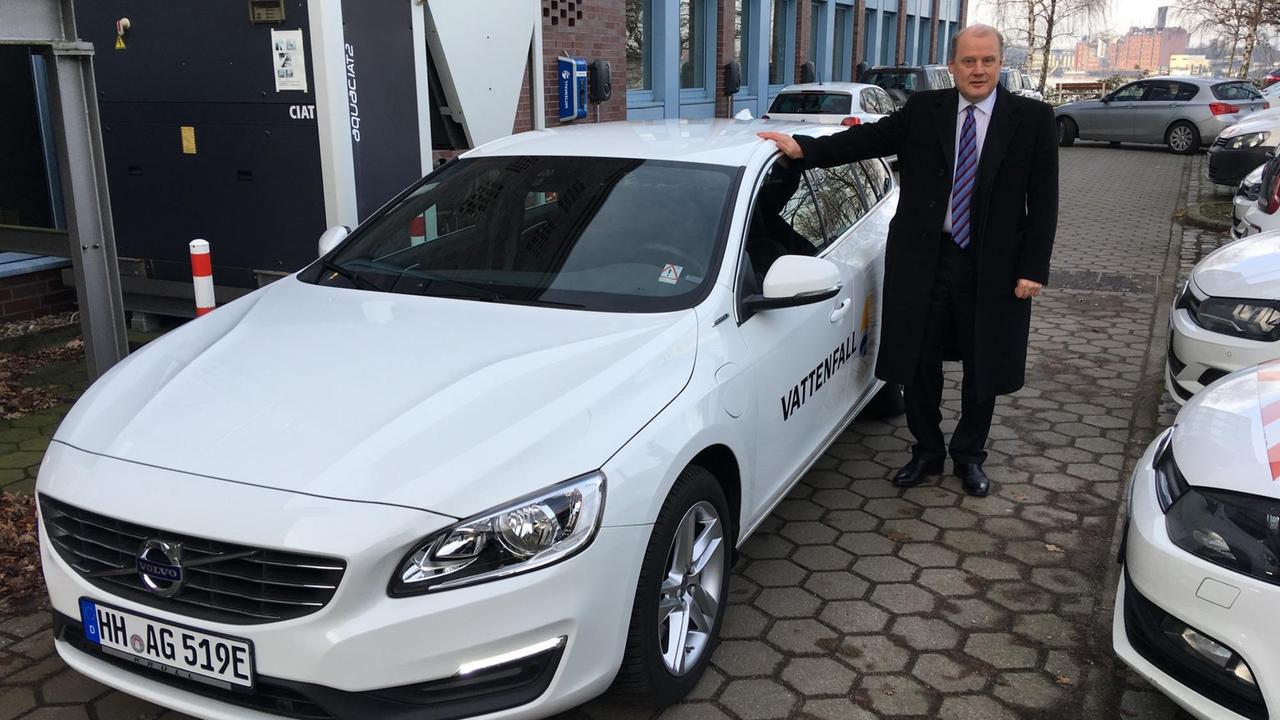
"Ich habe zwei Ladesäulen. Eine Ladesäule im Büro, die andere zu Hause. Damit ist Tanken sehr einfach." Ein Kabelende in die Säule, das andere ins Auto. Säule aktivieren, die Batterie lädt. Eine simple Prozedur – wäre da nicht ein Problem: "Es gibt einen Mangel an öffentlichen Ladesäulen. Es ist sehr mühsam, die Genehmigungen für öffentliche Ladesäulen zu bekommen. Da brauchen wir bessere Rahmenbedingungen. Da ist viel Nachholbedarf im Moment überall."
90 Kilometer im Winter, 120 im Sommer – das reicht nur für den Stadtverkehr. Zwar schaffen manche der neuesten Modelle einiges mehr, gut doppelt so viel. Dennoch: Das Aufladen dauert, die Herstellung ist teuer, verbraucht rare Rohstoffe und jede Menge Energie. Gesucht wird eine Superbatterie, die deutlich mehr als 500 Kilometer hält, die sicher ist, bezahlbar und ressourcenschonend. Auch Deutschland arbeitet daran.
"Thema Lithium-Ionen wird uns noch lange Zeit beschäftigen"
Münster, das Batterieforschungszentrum MEET. Peter Bieker passiert eine Schleuse, die verhindern soll, dass Luftfeuchtigkeit ins Labor dringt. "Die Luft wird hier gefiltert. Sie werden merken, wenn Sie hier zwei Stunden drinstehen, dass die Umwälzung so stark ist, dass Sie langsam austrocknen. Wenn Sie hier im Raum länger als eine Stunde oder so arbeiten, dann verlieren Sie auch ordentlich Gewicht, weil dem Körper Wasser entzogen wird."
Trinken ist Pflicht – weshalb sich vorm Labor die Mineralwasser-Kästen stapeln. Trockenraum, so nennen die Forscher ihr Labor, die Luft ist tausendmal trockener als in der Sahara, sagt Biekers Kollege Tobias Placke. "Das ist sehr wichtig für den Zusammenbau der Batterien, weil Luftfeuchtigkeit oder Wasser der Batterie schadet und dadurch sehr starke Alterungseffekte auftreten."
Placke und Bieker gehören zu den rund 200 Fachleuten, die sich in Münster um die Batterie von morgen kümmern – um Akkus, die länger halten, sich schneller aufladen lassen und günstiger sind. Braucht es dafür ganz neue Ideen, eine Revolution? Oder genügt es, an der bewährten Technik zu schrauben - der Lithium-Ionen-Batterie? "Wir glauben fest daran, dass das Thema Lithium-Ionen uns noch lange Zeit beschäftigen wird, sind aber durchaus offen, auch alternative Technologien zu untersuchen."
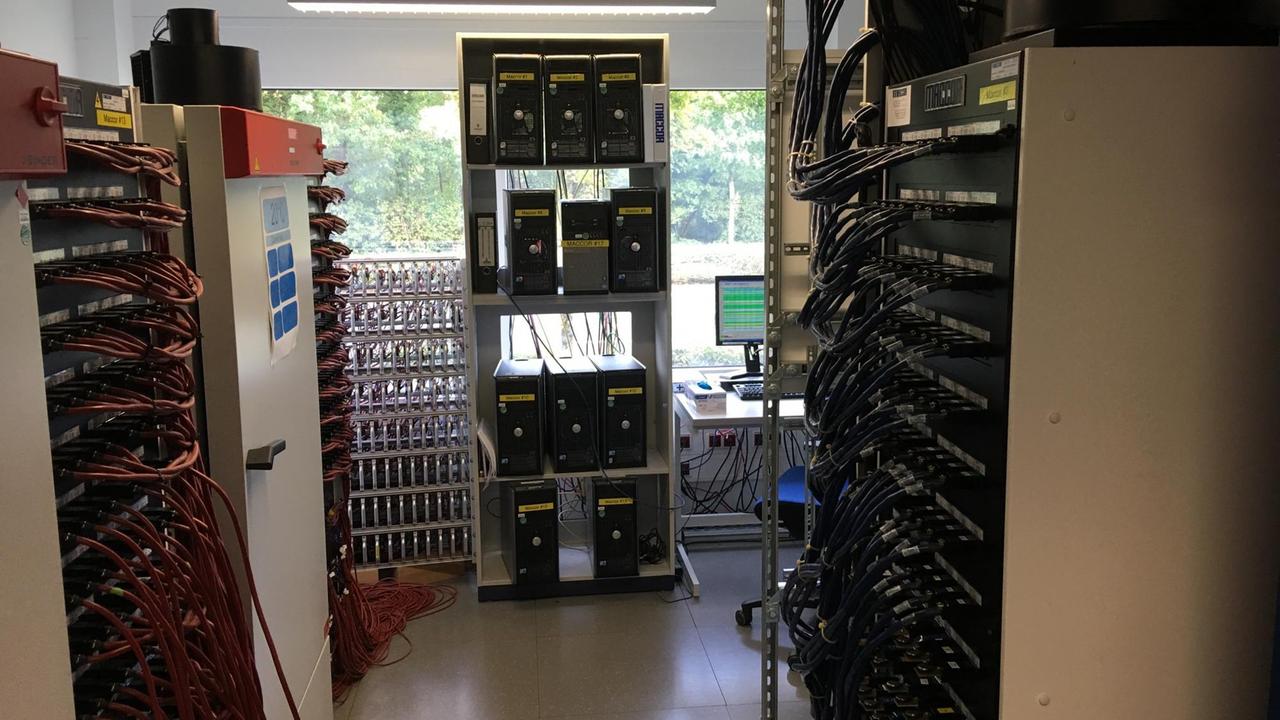
Die Lithium-Ionen-Batterie. Am 4. Februar 1991 von Sony vorgestellt. Heute steckt sie in Smartphones, Laptops und Elektroautos, sagt Martin Winter, der wissenschaftliche Leiter des MEET.
"Die Lithium-Ionen-Batterie besteht im Prinzip aus zwei Elektroden und einem Elektrolyten. Elektroden muss man sich vorstellen wie Hotels. Die Hotels nehmen Lithium-Ionen als Gäste auf. Diese Lithium-Ionen können reversibel, das heißt umkehrbar, in diesen Hotels aufgenommen werden, beziehen dort ihre Zimmer und gehen danach wieder aus den Hotels heraus."
Bildlich gesprochen steht das eine Hotel, die positive Elektrode, im Tal – wenig Energie. Das andere Hotel, die negative Elektrode, thront auf dem Berg – viel Energie.
"Wenn geladen wird: Die positive Elektrode, da wandern die Gäste raus und wandern in die negative Elektrode. Beim Entladen, beim Prozess, bei dem die Energie gewonnen wird, werden die Gäste aus der negativen Elektrode gehen und wandern zur positiven Elektrode."
Energie, Leistung, Lebensdauer, Sicherheit, Kosten
Beim Laden muss Energie hineingesteckt werden – quasi die Energie, um die Gäste vom Tal auf den Berg zu befördern. Beim Entladen, wenn die Gäste von oben nach unten rutschen, wird diese Energie wieder frei, die Batterie liefert Strom. Je größer der Höhenunterschied ist, umso größer die Spannung, und je mehr Betten die Hotels haben, umso höher ist die Kapazität der Batterie, umso mehr Strom kann sie speichern.
"Das sind die fünf Kriterien: Energie, Leistung, Lebensdauer, Sicherheit, Kosten. Und das Schöne ist: Lithium-Ionen-Batterien kann man anpassen, dass man überall einen relativ brauchbaren Eigenschaftsmix hat. Man kann sie auch trimmen, dass sie besonders starke Leistung hat und dabei nicht so viel an Leben verliert. Oder man kann sie auf besonders starken Energieinhalt trimmen. Und sie ist immer noch recht leistungsfähig."
Mit der Zeit konnte die Forschung die Lithium-Ionen-Batterien immer weiter verfeinern: Elektroden, die mehr Lithium aufnehmen. Elektrolyte, die das Lithium besser zwischen den Elektroden hin- und herleiten. Und: raffinierte Architekturen mit einem Maximum an Speichermaterial und einem Minimum an Peripherie. Dennoch: Es gibt Optimierungsbedarf, etwa in punkto Sicherheit.
"Wie kann man Batterien nicht nur aktiv sicher machen, durch das entsprechende Management – in Autos werden Batterien gemanagt –, sondern auch passiv sicher machen, dass sie gar nicht brennen können?"
Oder in punkto Schnellladung. "Fünf Minuten glaube ich, das ist akzeptabel. Im Moment sind es 20 bis 30 Minuten. Das ist für viele schon nicht mehr so komfortabel." Oder in punkto Ressourceneinsatz. "Wenn jeder von uns ein Elektroauto hat, wird’s eng bei einigen Elementen. Da müssen wir uns Alternativen überlegen."
Und natürlich in punkto Kapazität. Was ist noch möglich mit der Lithium-Ionen-Technologie? Im Trockenraum des MEET stehen Peter Bieker und Tobias Placke vor den Apparaturen, mit denen sie ihre Batterie-Prototypen herstellen.
Eine Stanze für Elektroden. Ein Gerät zum Anschweißen der Metallkontakte. Eine Maschine zum Vakuumverpacken der Batteriezelle. Und die Wickelmaschine. Sie wickelt die positive und die negative Elektrode – beide in Folienform – zu einem kleinen Zylinder auf, voneinander getrennt durch den Separator, eine Trennfolie.
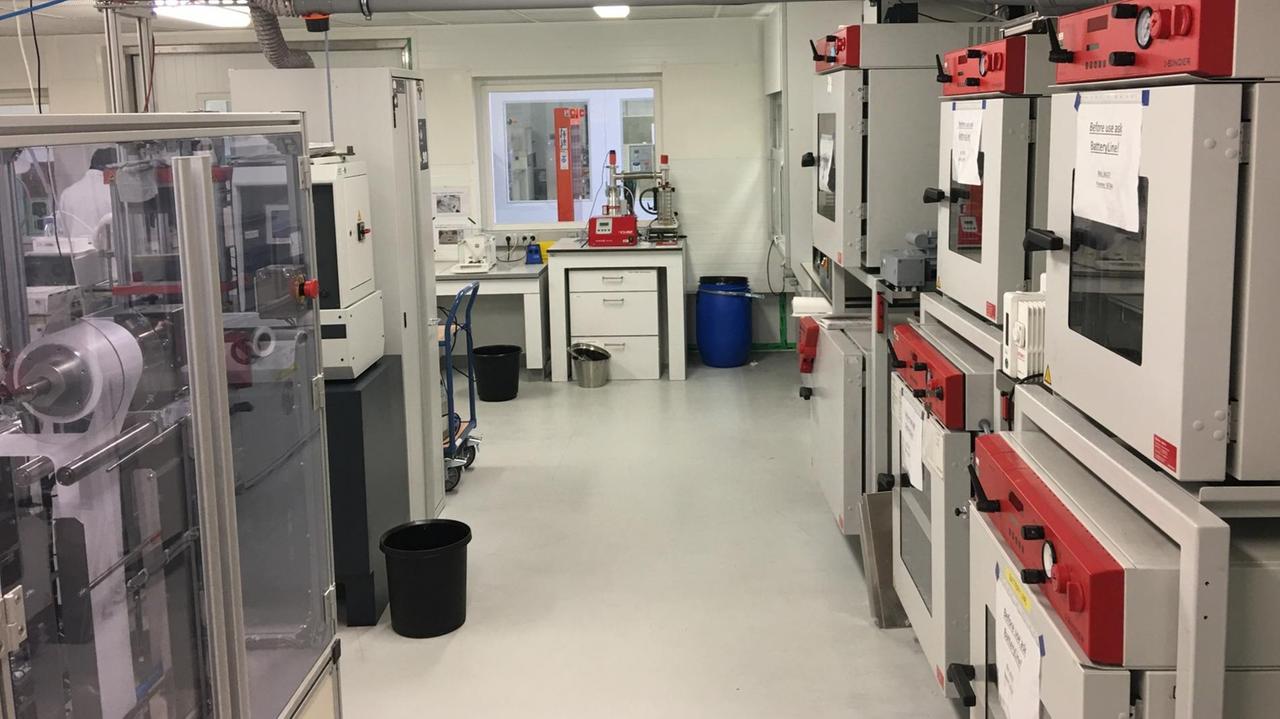
"Hier oben wird die Kathode eingespannt. Da steht ja auch schon positiv. Hier wird die negative Elektrode, also die Anode, eingespannt. Gleichzeitig wird oben und unten der Separator langgeführt. Das Ganze wird hier vorne aufgewickelt und in einen Behälter gepackt."
Zigtausende stecken im Tesla Model S
Dieser Behälter sieht aus wie ein Lippenstift – genau jener Batterietyp, der zu Zigtausenden im Tesla Model S steckt, dem wohl bekanntesten Elektroauto. In vielen Praxistests schafft er bei normalem Tempo mehr als 300 Kilometer, bei defensiver Fahrweise sogar noch mehr, kostet allerdings über 100.000 Euro. In Münster tüfteln die Forscher unter anderem daran, die Elektroden der Batterien zu verbessern. Tobias Placke nimmt eine Folie in die Hand – das Elektrodenmaterial.
"Momentan wird, wenn man die Anode anschaut, Graphit standardmäßig eingesetzt in allen Lithium-Ionen-Zellen. Man versucht mehr und mehr dahinzukommen, auch Silizium einzusetzen. Das könnte die Energiedichte und auch die Reichweite für die Elektromobilität deutlich nach vorne bringen."
Das Problem: Silizium kann zwar viel Lithium speichern, dehnt sich dabei aber kräftig aus, um das Dreifache seines Volumens. Reine Siliziumelektroden würden durch das extreme An- und wieder Abschwellen ziemlich schnell kaputtgehen. Deshalb bauen die Forscher das Silizium in die Graphitelektroden ein.
"In jetzigen Zellen ist schon ein bisschen Silizium drin, ein bis zwei Gewichtsprozent vielleicht. Das wird weiter optimiert, das wird mehr und mehr kommen. Und dadurch wird man auch mehr Reichweite bekommen. Das ist nicht mehr so weit weg."
Bis zu 20 Gewichtsprozent Silizium scheinen machbar, meint Placke – und damit ein respektabler Kapazitätsgewinn.
Ein weiterer Angriffspunkt: der Elektrolyt, also jene Flüssigkeit, die in der Batterie für den Transport der Lithium-Ionen zwischen den Elektroden sorgt.
"Da ist der Nachteil, dass wir organische Lösemittel haben. Organische Lösemittel sind sehr reaktiv in Verbindung mit Lithium. Es könnte anfangen stark zu brennen wegen der organischen Flüssigkeiten."
Flüssigelektrolyte ersetzen durch feste, pulverförmige Elektrolyte
Franziska Klein arbeitet am Helmholtz-Institut Ulm, eines von mehreren Batterieforschungszentren, die in den letzten Jahren in Deutschland gegründet wurden. Brennende Lithium-Akkus haben immer wieder für Schlagzeilen gesorgt, in Laptops, aber auch in Elektroautos. Deshalb wollen Klein und ihre Kollegen die brennbaren Flüssigelektrolyte durch weniger heikle Stoffe ersetzen – durch feste, pulverförmige Elektrolyte.
"Die haben sehr hohe Leitfähigkeit, also können sehr gut Lithium transferieren. Eine große Schwierigkeit dabei ist: Wenn man den Flüssigelektrolyt hat, der dringt einfach schnell überall ein. Bei dem Festelektrolyten hat man das Problem, dass man Grenzflächen hat, zum Beispiel zur festen Anode. Dadurch entstehen Widerstände, die überwunden werden müssen. Und das sind Herausforderungen."
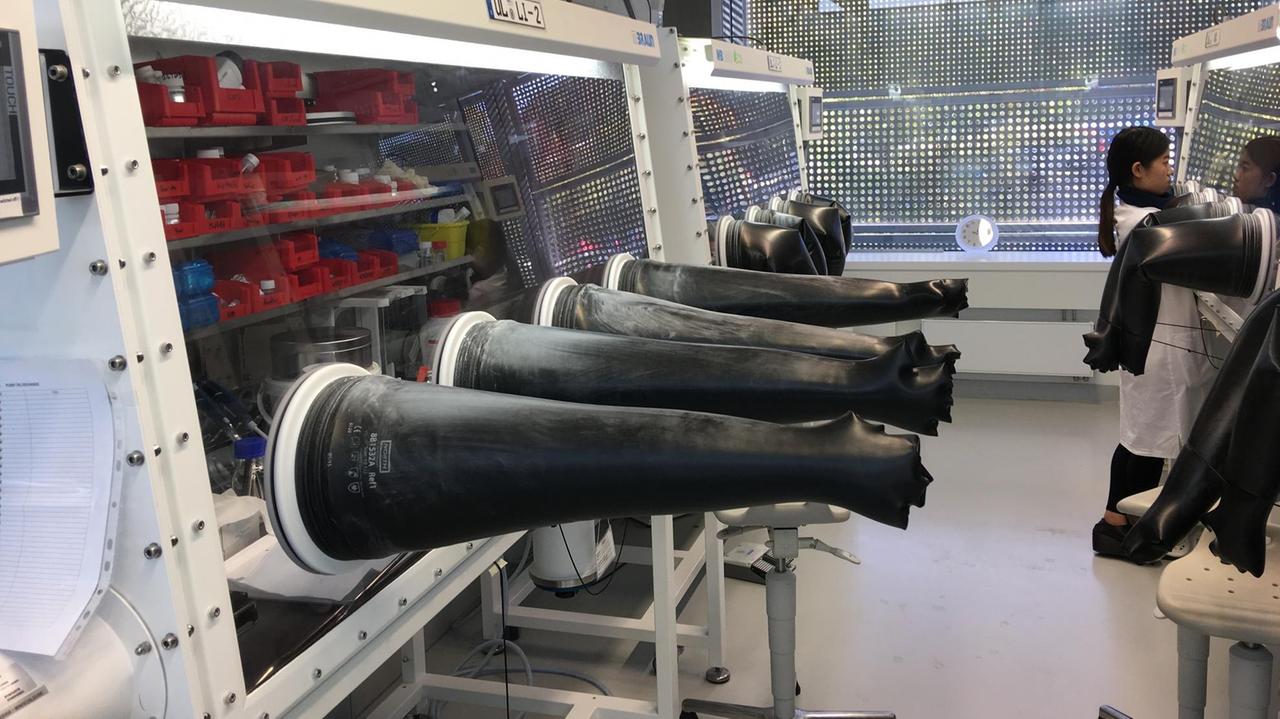
Die Forscher versuchen das Problem zu lösen, indem sie das Pulver fest mit den Elektroden verpressen, das vermindert den Widerstand. Oder sie experimentieren mit hauchdünnen Elektrolyt-Schichten, das senkt ebenfalls den Widerstand.
"Da ist man gerade auf einem guten Weg, viel zu verstehen. Ich denke, das wird für die Industrie interessant sein, gerade weil man die Sicherheit erhöhen kann. Die Sicherheit ist ein wichtiger Faktor gerade im Auto. Die wollen ihren Kunden nur Autos verkaufen, wo sie sagen können: Unsere Batterie ist sicher."
Und weil die Batterie durch den festen Elektrolyten sicherer würde, ließe sich das Speichermaterial auch dichter packen.
"Die Energiedichte kann dadurch erhöht werden. Die ist wichtig, denn je höher die Energiedichte, desto größer wird auch die Reichweite."
"Jetzt wird es etwas lauter. Das liegt daran, dass wir mehrere Klimaanlagen haben, um die Temperatur möglichst gleichbleibend zu halten, um keine verfälschten Ergebnisse zu haben."
Jede Zelle in einer sogenannten Klimakammer
Zurück in Münster. Hinter der Tür, die Peter Bieker gleich öffnet, steckt eine der Kernkomponenten des Instituts – ein Teststand. "In diesem Raum befinden sich 1200 Kanäle, um 1200 Batteriezellen gleichzeitig zu laden und zu entladen. Dann gehen wir mal rein."
"Wie Sie hören, haben wir hier ein sehr starkes Gebläse, das kommt von den ganzen Lüftungen. Jede Batteriezelle hat hier einen eigenen Kanal, deswegen haben wir hier die ganzen Kabel heraushängen. Jede Zelle ist in einer sogenannten Klimakammer bei einer festen Temperatur und wird dort zyklisiert."
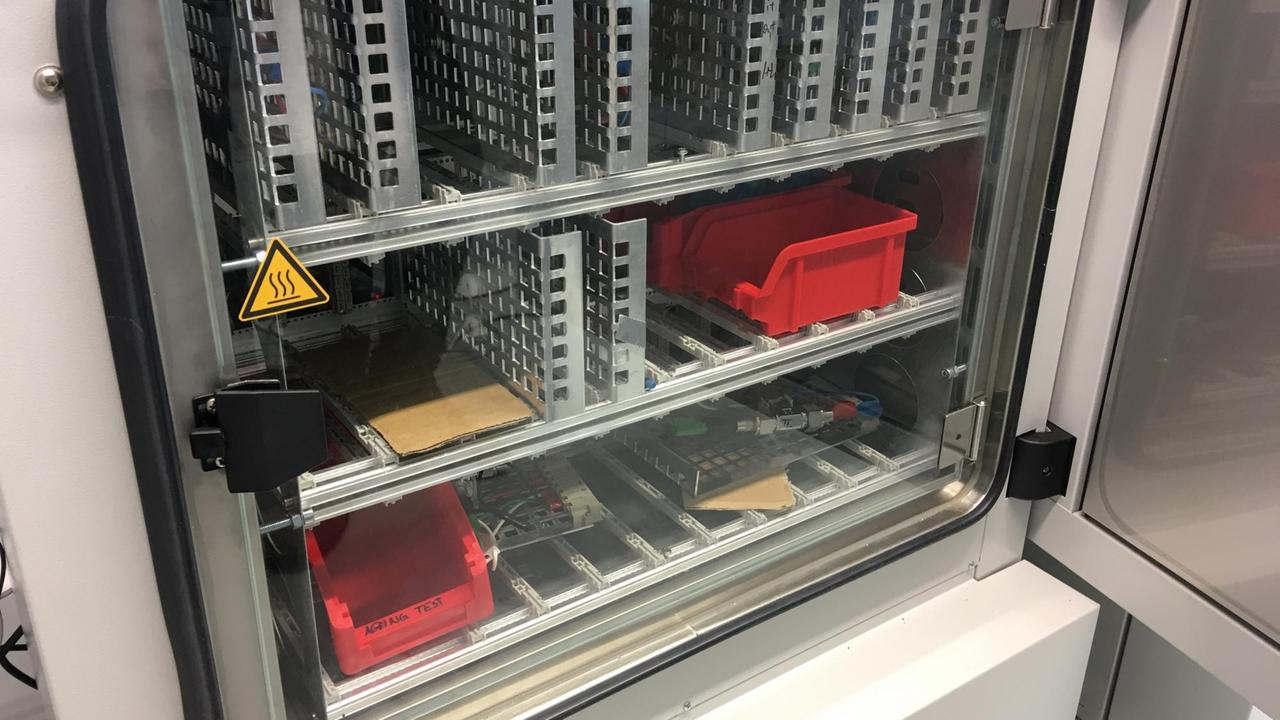
Zyklisieren – so nennen die Forscher es, wenn sie ihre Prototypen immer wieder laden und entladen – dutzende, hunderte, tausende Male nacheinander.
"Hier gibt's Zellen, die haben ihre 10.000-12.000 Zyklen durch und laufen immer noch." Das Ziel: Innerhalb von 20 Minuten soll eine Batterie auf 80 Prozent ihrer Maximalkapazität geladen werden, und zwar in einem Temperaturbereich von minus 40 bis plus 60 Grad. Die Nagelprobe für neue Prototypen, sagt Tobias Placke.
"Wenn man neue Materialien anschaut, sieht man relativ schnell, ob die sich stabil verhalten. Wenn die Kapazität relativ schnell abfällt nach wenigen Ladezyklen, sieht man, dass da irgendwas nicht stimmt, und man muss das Ganze verbessern."
"Wir versuchen laufend, immer mehr Energie auf immer kleinerem Raum zu speichern. Hier verspricht die Lithium-Schwefel-Batterie Einiges: Theoretisch könnte sie die zehnfache Kapazität eines Lithium-Ionen-Akkus haben."
Alberto Varzi, Batterieforscher am Helmholtz-Institut Ulm. Bei der Lithium-Schwefel-Batterie dient Schwefel als Pluspol. Der Unterschied zu den heutigen Akkus: Schwefel fungiert nicht als Hotel für die Lithium-Ionen. Stattdessen reagiert es chemisch mit dem Lithium. So lässt sich das Lithium viel dichter packen. Bildlich gesprochen brauchen die Lithium-Ionen keine Hotelzimmer mehr, sondern stehen dicht an dicht wie die Zuschauer in einem Stadion.
"Leider ist der Weg noch ziemlich lang. Ein Problem: Wir können keinen reinen Schwefel verwenden, das wäre instabil, sondern müssen ihn in ein Kohlenstoffgitter einpacken. Und das ist nicht ganz einfach. (OTon hoch) Eine weitere Schwierigkeit: Beim Laden und Entladen entstehen Zwischenprodukte, und die senken die Lebensdauer der Batterie."
Immerhin: Zum Teil sind die Probleme gelöst, heute gibt es Labormuster mit einer Speicherkapazität anderthalb Mal so groß wie die eines Lithium-Ionen-Akkus – bezogen auf das Gewicht. Bezogen auf das Volumen verflüchtigt sich der Vorsprung aber gleich wieder: die Lithium-Schwefel-Batterie ist groß und nimmt viel Platz weg.
"Meiner Meinung nach dürfte es schwierig werden, die Technik bald in Elektroautos einzusetzen. Interessant könnte sie vor allem für Luft- und Raumfahrt sein, wo es weniger auf Platz ankommt als auf ein möglichst geringes Gewicht."
Große Erwartungen in die Lithium-Luft-Batterie
Ähnliches gilt für einen anderen Ansatz, in den die Fachwelt große Erwartungen setzte – die Lithium-Luft-Batterie. Hier besteht eine Elektrode aus Lithiummetall, die andere aus porösem Kohlenstoff, in den Sauerstoff geleitet wird. Theoretisch könnte die Energiedichte 20mal höher sein als bei Lithium-Ionen-Akkus. Aber den bisherigen Labormustern mangelt es unter anderem an Durchhaltevermögen. Schon nach wenigen Ladezyklen geben sie ihren Geist auf. Martin Winter:
"Metall-Luft halte ich ganz klar für ein Grundlagenthema. Absolut nicht absehbar, ob das eine Anwendung finden wird. Sehr viele Probleme: Nebenreaktionen überwiegen die eigentlich gewünschten Reaktionen. Meiner Meinung nach im Moment verfrüht zu sagen, dass das überhaupt kommt."
Lithium-Schwefel und Lithium-Luft – sie wurden lange als vielversprechende Nachfolger der Lithium-Ionen-Batterie gehandelt. Doch wie es scheint, können beide die Erwartungen nicht wirklich erfüllen.
Am MEET in Münster ist Tobias Placke ins Analyselabor gegangen. Ein Raum voller Hightech-Apparaturen, millionenschwer, mit komplexen Steuerpulten. Hier werden die Prototypen präzise unter die Lupe genommen.
"Da gibt’s verschiedenste Methoden, zum Beispiel ein Rasterelektronenmikroskop. Man nimmt die Elektroden nach dem Zyklisieren und kann sich die Oberfläche der Elektroden anschauen. Sind Alterungseffekte aufgetreten? Sind zum Beispiel Partikel auseinandergebrochen in der Elektrode? Daraus kann man Rückschlüsse ziehen, wie stabil das Material ist."
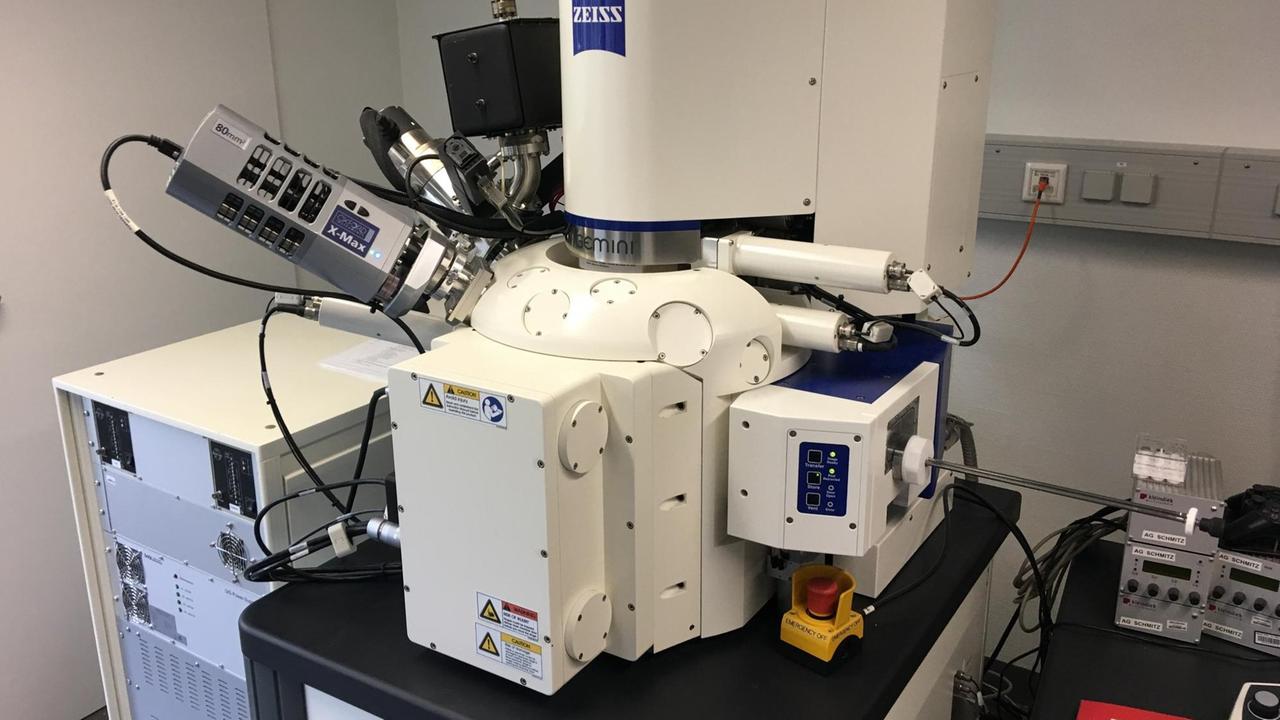
Placke schaltet das Mikroskop ein und zeigt auf den Monitor. Die Nahaufnahme einer Elektrode, sie erinnert an einen stark zerklüfteten Schwamm.
"Man sieht sehr schön die Porosität. Hier sind einzelne Partikel, zwischendrin sind Poren. Das sind alles Sachen, die großen Einfluss haben auf die Performance in der Zelle."
Durch die Poren kann der Elektrolyt tief in die Elektrode eindringen und den Lithium-Ionen den Weg ebnen bis in die hintersten Winkel. Dann dreht sich Placke um und zeigt auf einen speziellen Röntgenapparat. Der kann Batteriezellen quasi in Aktion durchleuchten. Was passiert in ihrem Inneren, wenn sie aufgeladen werden? Und was, wenn sie sich entladen?
"Da sieht man schön, wie die Lithium-Ionen in die Schichten eindringen können. Über mehrere Zyklen kann man sich das anschauen und Erkenntnisse gewinnen, wie stabil die Materialien sind, wie generell der Mechanismus der Speicherung abläuft."
Erkenntnisse, die helfen, die Technik Schritt für Schritt zu optimieren. "Im Augenblick haben wir zwei Ziele, die sich ein bisschen widersprechen. Das eine Ziel ist, die Batterie immer besser zu machen. Und das andere Ziel ist, im Auge zu haben, dass die Ressourcensituation sich verschärfen wird den nächsten Jahren."
Batterieherstellung verschlechtert die Klimabilanz
Maximilian Fichtner ist der Direktor des Helmholtz-Instituts Ulm. Die Batterieherstellung kostet viel Energie, was die Klimabilanz von Elektroautos verschlechtert. An der energieintensiven Herstellung wird sich nur wenig ändern lassen, meint Fichtner.
"Aus meiner Sicht ist die Lösung eher so, dass wir unser Stromsystem entsprechend anpassen. Idealfall wäre es so was wie Norwegen, die haben über 90 Prozent Wasserkraft. Wenn Sie die Herstellung mit erneuerbaren Energien machen, sieht der Footprint völlig anders aus."
Und: In Batterien stecken Rohstoffe, die, sollte jeder ein Elektroauto fahren, knapp werden könnten. Und das gilt nicht nur fürs Lithium.
"Das bezieht sich insbesondere auf das Element Kobalt. Kobalt ist im Pluspol in der Batterie drin. Kobalt wird im Augenblick größtenteils über Kinderarbeit im Kongo gewonnen. Als erstes versucht man, diesen Kobaltgehalt zu reduzieren, hoffentlich bis auf null. Da ist aber nicht sicher, ob man gleichzeitig auch die Speicherkapazität, die wir im Augenblick haben, erhalten kann bei den kobaltfreien Materialien."
Nickel ist eine naheliegende Alternative, meint Fichtner. Doch langfristig können auch die Nickelreserven knapp werden, außerdem sind Nickelstäube giftig. Deshalb arbeiten die Forscher an neuen Ansätzen – an Batterien, die ohne Lithium funktionieren und auch kein Kobalt und kein Nickel benötigen. Eine Alternative: Natrium, sagt Fichtners Kollegin Franziska Klein.
"Natrium finden wir überall, vor allem im Meer gelöst. Natrium ist das Element, das am siebthäufigsten in der Erdkruste vorkommt, und Lithium ist auf Platz 26." Aber: Natrium ist chemisch reaktiver als Lithium – ein Problem für die Sicherheit. Eine Herausforderung, die die Fachwelt allmählich in den Griff zu bekommen scheint.
"In Japan gibt es schon erste Überlegungen, dass Natriumionenbatterien auf den Markt gebracht werden können. Dass es sehr zeitnah auf den Markt kommt."
Ionen von Magnesium können mehr Elektrizität aufnehmen
Zwar versprechen Natriumbatterien Ressourcenvorteile, aber nicht unbedingt höhere Reichweiten als die heutigen Lithium-Akkus. Deshalb suchen Fachleute wie Maximilian Fichtner weiter: "Es gibt einige alternative Systeme, die in großer Menge verfügbar sind auf der Erde, wie Kalzium, Magnesium, Aluminium, die zumindest auf dem Papier deutlich höhere Speicherkapazitäten versprechen."
Der Hintergrund: Anders als bei Lithium oder Natrium sind die Ionen von Magnesium nicht einfach, sondern doppelt geladen, können also mehr Elektrizität aufnehmen.
"Wir arbeiten zum Beispiel an einer Magnesium-Schwefel-Zelle. Schwefel bekommen sie praktisch zum Nulltarif. Es gibt weltweit Millionen von Tonnen Schwefel aus Entschwefelungsanlagen. Magnesium – die Hälfte der Dolomiten besteht aus Magnesium – ist auch in großer Menge verfügbar. Und wenn ich die nackten Zahlen vergleiche von einer Magnesium-Schwefel-Zelle mit einer Lithium-Schwefel-Zelle, dann könnte eine Magnesium-Schwefel-Zelle im Volumen dreimal so viel Energie speichern wie eine Lithium-Schwefel-Zelle."
In einem Verbundprojekt wollen Fichtner und seine Leute nun die weltweit ersten größeren Magnesium-Schwefel-Zellen herstellen. Aber:
"Da gibt es noch Probleme. Es ist immer noch so, dass wir deutlich mehr Spannung anlegen müssen beim Beladen, als dass wir hinterher herausbekommen. Das heißt da gibt es noch Widerstände in der Batterie, die wir im Augenblick noch gar nicht richtig verstehen. Da ist noch Forschung erforderlich, damit es am Ende alles auch kommerziell Sinn macht."
Kommerziell Sinn machen – das würde wohl auch eine andere Maßnahme. Heute nämlich werden die Batteriezellen fast ausschließlich in Asien produziert. Keine gute Voraussetzung für einen Durchmarsch der Elektromobilität in Europa, meint Fichtner.
"Weil die großen Batteriemengen, die wir hier in Europa benötigen werden, kann man nicht alle immer antransportieren. Das ist aber schon in Arbeit. Es ist es so, dass große asiatische Hersteller anfangen mit Anlagen in Europa, die zu planen, die aufzubauen. Allerdings nicht in Deutschland, sondern in Polen und Rumänien."
Das europäisches Konsortium TERRA E will nun Ende 2019 eine eigene Produktion etablieren, der Standort soll in Deutschland liegen. Anfang März gab es aber auch einen Rückschlag: Der Elektronikkonzern Bosch hat angekündigt, sich aus der Batterieforschung zurückzuziehen. Die Investitionen seien schlicht zu hoch, um es mit der Konkurrenz in Asien aufzunehmen.
Aus Sicherheitsgründen aufs Dach des MEET verlagert
Wir steigen aufs Dach des Batterieforschungszentrums MEET in Münster, Peter Bieker will zum Schluss noch etwas Besonderes zeigen – graue Container mit wuchtigen Türen und Warnschildern.
"Das sind Teststände für größere Testzellen, wir können hier Zellen bis zu 400 Amperestunden, also wirklich große Zellen testen, die teilweise schon im Auto drin waren oder die ins Auto rein sollen."
Ein Härtetest für ausgewachsene Batterien. Zuweilen werden sie hier bis an ihre Grenzen belastet. Entsprechend hoch sind die Sicherheitsvorkehrungen.
"Jede Zelle hat eine eigene Kammer. Sollte es zu einem Brand kommen, wird diese Kammer sofort mit Argon geflutet und der Brand gelöscht. Deswegen steht das Ganze hier oben auf dem Dach. Wenn irgendwas passiert, dann hier im Container und nicht unten im Labor."
Im Labor mit den kleinen Prototypen umzugehen, sei eine Sache – mit großen, praxisnahen Systemen eine andere, meint der Forscher.
"Und wir haben noch ein Labor, das steht hinten auf der grünen Wiese. Da werden die Zellen absichtlich kaputtgemacht. Zum Beispiel einen Nagel durch die Zelle geschossen, und dann wird geguckt, was mit der Zelle passiert."
"Quant E sport limousine is a full electric car, powered with a flow battery called Nanoflowcell…"
Auf einer Automesse steht der Prototyp eines Supersportwagens: extrem flach, extrem windschnittig, die Flügeltüren hochgeklappt. Nunzio La Vecchia, Inhaber der kleinen Schweizer Firma Nanoflowcell, hebt vorsichtig die Motorhaube an. Darunter schlummert kein fetter Zwölfzylinder, sondern ein Tank – Bestandteil eines vermeintlich revolutionären Batterietyps, der Flusszellenbatterie: Bei ihr steckt die Energie nicht in den Elektroden, sondern im Elektrolyt, einer Art Salzwasser.
"For filling up the systems you need not more time than a conventional car…"
Statt die Batterie stundenlang aufladen zu müssen, genüge es einfach den Elektrolyten nachzutanken – behauptet La Vecchia. Und erst die Reichweite: 1000 Kilometer an einem Stück soll die Schweizer Wunderbatterie durchhalten. Zu schön, um wahr zu sein - meint manch ein Fachmann.
"Wenn man sich alle Parameter, die angegeben sind, von den Beschleunigungswerten, Fahrzeuggewichten, Reichweiten, Spitzengeschwindigkeiten anschaut, dann ist einfach zu viel Widerspruch in den Zahlen. Das passt einfach alles nicht zueinander."
Jens Tübke steht in einer Halle seines Instituts, dem Fraunhofer ICT in Pfinztal. Wie Nanoflowcell in der Schweiz arbeitet auch er an der Flusszellenbatterie, auch Redox-Flow-Batterie genannt. Doch Tübkes Batterie füllt eine Halle – es ist ein Prototyp, der die Energie eines Windrads zwischenspeichert. Der Elektrolyt lagert in riesigen Tonnen, zusammen haben sie das Fassungsvermögen eines Hallenbadbeckens. Das ist der Nachteil der Flusszellenbatterie: Ihre Energiedichte ist zu gering für ein Elektroauto.

"Wir sind heute noch eine Größenordnung davon entfernt. Und es ist auch nicht abzusehen, dass man damit auf entsprechend notwendige Energiedichten kommt. Das macht für mobile Anwendungen keinen Sinn."
Jubelmeldungen über Batterien mit fantastischen Reichweiten gibt es immer wieder, sagt Maximilian Fichtner.
"Es gibt eine Menge Start-ups, die alles Mögliche versuchen. Sie können exotischere Materialien verwenden, die deutlich höhere Speicherkapazitäten bringen. Aber die haben nicht so eine lange Lebensdauer. Und damit kommen sie dann schon mal weit – aber nicht sehr oft. "
Durchbruch morgen oder in drei Jahren?
Die Forschung an neuen Batteriekonzepten macht Fortschritte, zumindest im Labor. Noch aber sind viele Probleme ungelöst. Ob und wann man sie in den Griff bekommt, ist nur schwer vorherzusagen.
"Es kann sein, dass wir in der nächsten Woche einen Durchbruch erzielen. Es kann aber sein, dass es erst in drei Jahren passiert oder nie. Es gibt Dutzende von vielversprechenden Systemen in der Vergangenheit, in der alle möglichen Gruppen auf der Welt versucht haben, etwas Tolles zum Laufen zu bringen. Das ist dann irgendwann daran gescheitert, dass man das Material nicht billig herstellen kann oder dass es ein Sicherheitsproblem hat oder dass das Verhalten in der Zelle auf lange Sicht einfach nicht in den Griff zu bekommen war. Es gibt immer wieder Dinge, an denen das am Ende doch noch scheitern kann. Deshalb bin ich da vorsichtig."
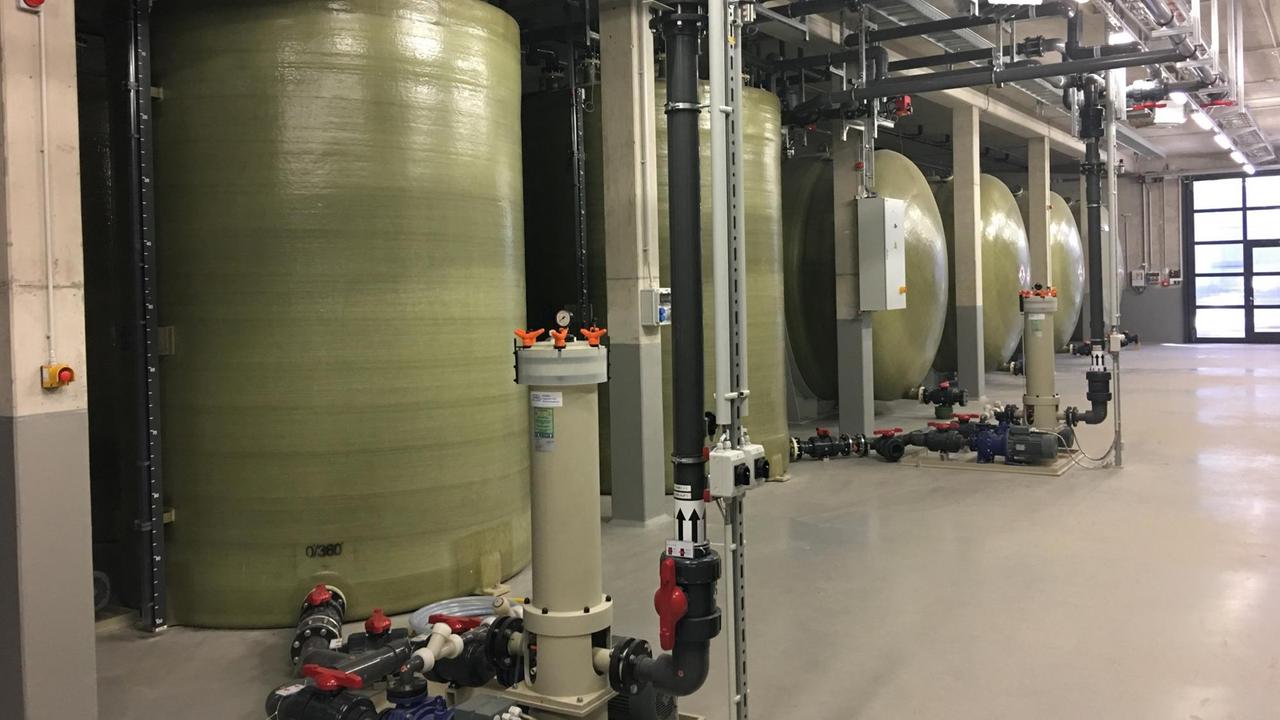
So sieht es auch die Automobilbranche – und setzt erst mal darauf, die bewährte Lithium-Ionen-Technologie weiterzuentwickeln. In ein bis zwei Jahren, sagt sie, soll es halbwegs bezahlbare Batterien mit Reichweiten bis zu 500 Kilometer geben. Aber:
"Es gilt dafür, wo man 90 km/h fährt und möglichst wenig elektrische Verbraucher anhat. Echte Reichweite, das heißt mit komfortablem Fahren, auch mal die Klimaanlage an und solche Sachen – da werden wir 2025 die 500 Kilometer leicht überschritten haben. Die 700 Kilometer halte ich auch für machbar."
Die Superbatterie kommt also nicht per Revolution, sondern schrittweise, als Evolution. Die Technik, sagt Martin Winter, verbessert sich von Jahr zu Jahr.
"Ich glaube, wenn die Leute sagen: Ich kaufe mir kein Auto, sondern ich lease es, und nach zwei bis drei Jahren gebe ich es zurück und nehme das nächste mit der besseren Batterie, fährt man auf Nummer sicher."
"Dann nehmen wir einfach dieses Kabel mit, und die Sache ist erledigt. Jetzt haben wir wieder genug Reichweite, um vom Büro zurück nach Hause zu fahren."
Das Elektroauto, das Tuomo Hatakka an der Ladesäule angeschlossen hatte, ist nun aufgeladen. Er stöpselt das Ladekabel ab und verstaut es im Kofferraum. Die Batterie ist voll, die Fahrt kann weitergehen.
Hatakka fährt los, dann zeigt er auf einen Schalter – den Range Extender. "Das ist ein benzingetriebener Generator. Ich kann mit diesem Generator die Autobatterie aufladen. Dann habe ich die doppelte Reichweite, theoretisch 250 Kilometer."
Gebraucht habe er den Benzingenerator zwar noch nie, sagt Hatakka. Aber trotzdem: "Das ist wie eine Lebensversicherung im Falle eines Falles."
Zu Wort kamen in der Sendung folgende Experten:
Prof. Dr. Maximilian Fichtner, Helmholtz-Institut Ulm
Dr. Alberto Varzi, Helmholtz-Institut Ulm
Dr. Franziska Klein, Helmholtz-Institut Ulm
Prof. Dr. Martin Winter, Batterieforschungszentrum MEET, Münster
Dr. Peter Bieker, Dr. Tobias Placke, MEET, Münster
Prof. Dr. Jens Tübke, Fraunhofer-Institut für Chemische Technologie, Pfinztal
Tuomo Hattaka, Vattenfall, Berlin
Dr. Alberto Varzi, Helmholtz-Institut Ulm
Dr. Franziska Klein, Helmholtz-Institut Ulm
Prof. Dr. Martin Winter, Batterieforschungszentrum MEET, Münster
Dr. Peter Bieker, Dr. Tobias Placke, MEET, Münster
Prof. Dr. Jens Tübke, Fraunhofer-Institut für Chemische Technologie, Pfinztal
Tuomo Hattaka, Vattenfall, Berlin