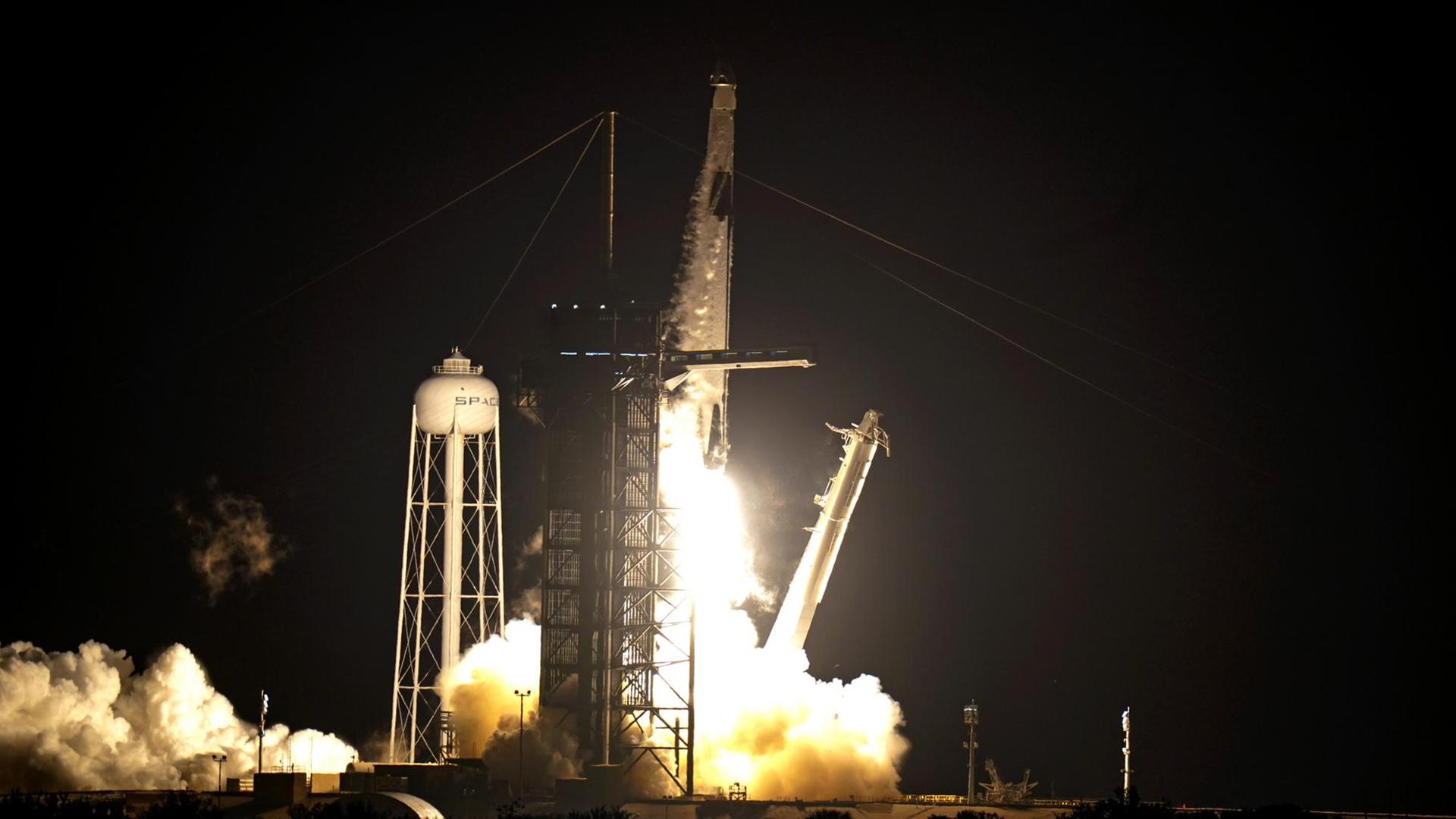
"Das hier ist mein Baby. Ich habe hier angefangen als Projektleiter, bei der Rocket Factory. Und das hier war meine Case Study."
In einer Fabrikhalle steht Ibrahim Ata vor einem Zylinder aus Edelstahl und Karbon von der Größe eines Kleinbusses.
"Das ist der Oberstufentank, flugqualifiziert."
Es ist der Tank für eine Rakete, die hier am Rand von Augsburg gerade entwickelt wird. Daneben stehen Fräsmaschinen und Drehbänke; in einem eigens abgetrennten Raum brummen 3D-Drucker.
Kleinsatelliten sollen in die Umlaufbahn gebracht werden
Eine Etage weiter oben sitzen in einem Großraumbüro einige Dutzend Entwickler der Rocket Factory Augsburg, die heute 85 Mitarbeiter zählt. Jörn Spurmann gehörte vor drei Jahren zu den Gründern. Damals erkannten Investoren weltweit, dass sich ein neuer Markt entwickelte.
"Wenn man alle Konstellationen aus Kleinsatelliten nimmt, die momentan irgendwo als Idee auf dem Papier existieren und die Business Cases der Firmen, mit denen wir sprechen, dann sind es über 50.000 Satelliten über die nächsten zehn Jahre."
Schon lange werden in Deutschland Raketenteile entwickelt. OHB, der Mutterkonzern der Rocket Factory Augsburg, baut Teile für die Ariane 5 und ihren Nachfolger Ariane 6. Aber diese Raketen sind zu teuer; US-Konkurrent SpaceX startet viel günstiger. SpaceX kann Erststufen seiner Raketen zur Startrampe zurückkehren lassen und dann wiederverwenden – und hat die Startpreise massiv gesenkt.
Gestufte Verbrennung als Marktvorteil
"Das ist der Vorbrenner. Das ist die Turbopumpe", erklärt Ibrahim Ata. Mit ihrem Raketentriebwerk wollen die Augsburger der Konkurrenz die Stirn bieten. "Und hier ist die Brennkammer. Das darunter ist der Düsenhals."
Das Verfahren heißt gestufte Verbrennung: Der Treibstoff und flüssiger Sauerstoff befeuern zunächst eine Turbine, die wiederum eine Hochleistungspumpe antreibt.
"Um die Turbopumpe anzutreiben, braucht man eine suboptimale, nicht stöchiometrische Mischung, damit man von der Temperatur ungefähr bei 700 °C ist."
Die Pumpe drückt dann den Treibstoff in die Brennkammer, wo 300 bar herrschen: selbst für ein Raketentriebwerk ein extremer Druck.
3D-Drucker liefern Bauteile für das Triebwerk
"Alles wird perfekt verbrannt. Du hast maximale Energieausbeute. Ist aber von der Entwicklung her ein bisschen komplizierter. Es ist komplizierter, sagen wir es so."
Teile des Triebwerks kommen aus dem 3D-Drucker. Eine Brennkammer, die besonders hohe Temperaturen aushalten muss, besteht aus einer exotischen Kupferlegierung. Verbrannt wird darin ein eigens entwickeltes Kohlenwasserstoff-Gemisch, das etwas leichter ist als Kerosin. Neun dieser Triebwerke sollen einmal gebündelt die erste Raketenstufe antreiben. Jedes einzelne Triebwerk ist kaum größer als ein Kfz-Motor. Und das hat einen einfachen Grund, sagt Firmengründer Stefan Brieschenk.
"Wenn Sie Raketenmotoren bauen, die so groß sind wie ein Automobilmotor, dann kann ich das recht einfach automatisieren. Das ist natürlich bei großen Raketenmotoren deutlich schwerer. Da braucht so etwas Wochen."
Der Heilige Gral der Raketenbauer
Die Augsburger wollen 1.600 Kilogramm in einen niedrigen Orbit bringen. Doch da sind die Ingenieure noch lange nicht: Auf einem Prüfstand in Schweden haben gerade die Tests einzelner Komponenten begonnen. Das Verfahren der gestuften Verbrennung gilt unter Raketenbauern als heiliger Gral, weil es zwar sehr effizient, aber auch sehr komplex ist. US-Raketentüftler von SpaceX und Blue Origin arbeiteten ein Jahrzehnt lang an Triebwerken mit vergleichbarer Technik – und kämpfen bis heute mit technischen Problemen.
Stefan Brieschenk, der Erfahrungen vom neuseeländischen Raketenbauer Rocket Lab mitbringt, ist dennoch optimistisch, dass die Rakete aus Augsburg schon Ende nächsten Jahres abheben kann: "Daher also unser Ziel ist natürlich, das so schnell hinzubekommen wie jetzt ein Rocket Lab oder SpaceX, aber mit weniger Failure. Ja, mal sehen."