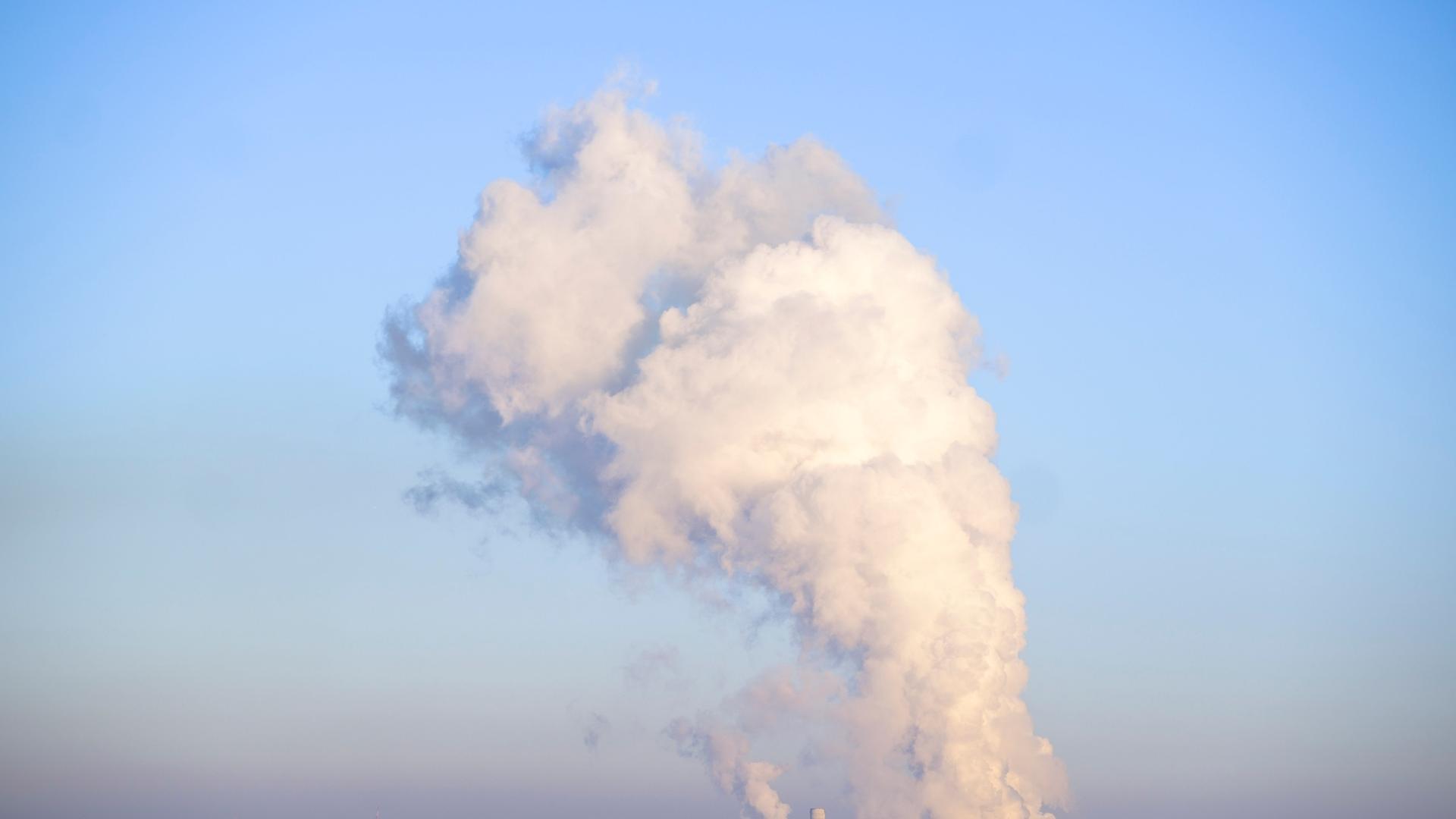
- Die Forschung läuft auf Hochtouren
- Die Risiken des Wandels
- Die enormen Kosten für grünen Strom
- Welche Konzepte gibt es?
- Arbeitsprozesse müssen neu konzipiert werden
- Welche Rolle spielt Wasserstoff?
- Stahlproduktion mit Wasserstoff
- Die Vision einer sauberen Industrie
- Immenser Bedarf nach grünem Wasserstoff
- Die natürlichen Grenzen der CO2-Vermeidung
- CO2 als Grundstoff für neue Produkte
- CO2 dauerhaft binden
Stephan Behle steht vor einer riesigen Aufgabe – wörtlich genommen und im übertragenen Sinn. Der Forschungsdirektor von Saint-Gobain Deutschland läuft durch eine Werkhalle in Herzogenrath, vor ihm breitet sich eine Anlage aus, die auf den ersten Blick wie ein riesiger grauer Bunker wirkt: ein Industrieofen für das Schmelzen von Glas.
„Hier kommt das Gemenge rein“, erklärt er. Also Materialien wie Sand, Soda und Dolomit, die in dem Industrieofen geschmolzen werden. In der sogenannten Glaswanne.
„Da ist auch das berühmte Schild mit dem Namen der Wanne: Hier Marie Luise. Und die wurde erbaut 2004 und sie wurde gezündet 2005. Und seitdem läuft die jeden Tag 24 Stunden.“
Stephan Behles riesige Aufgabe ist, diese Wanne klimaneutral zu machen. Genauso wie den gesamten Standort von Saint-Gobain in Herzogenrath. Ziel ist das Jahr 2030. Doch gerade für die besonders energieintensive Glaswanne liegt die Deadline früher: „Die soll laufen bis 2027, bis 2028“, sagt Behle. „Dann wollen wir sie reparieren. Und das ist der Zeitpunkt, wo wir all das einbauen wollen, um diese Wanne CO2-neutral zu bekommen.“
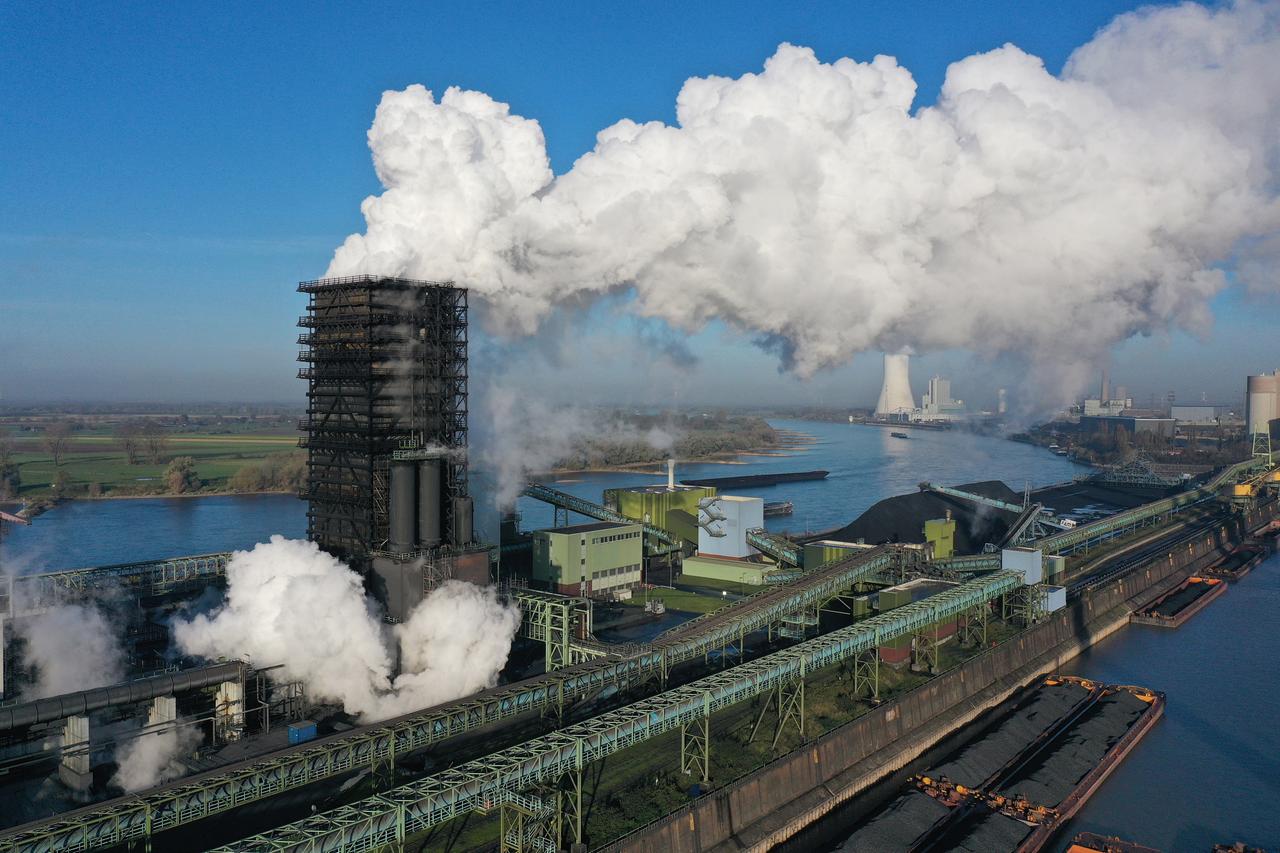
Dann sollen durch die Glasschmelze keine Treibhausgase mehr anfallen. Die Forschung dafür läuft auf Hochtouren, auch zur Frage, wie man den gesamten Standort klimaneutral umbauen kann. Behle betont: „Da sind 100 bis 150 Kolleginnen und Kollegen, die nur diese Fragestellung beleuchten. Wir sind da also ziemlich unterwegs und das ist ein Marathon.“
Eine Industrie zu schaffen, die kein CO2 mehr ausstößt, die nicht mehr dem Klima schadet: Das ist das Ziel von EU und Bundesregierung. Die EU will es bis 2050 erreichen, die Bundesrepublik bis 2045, und einige Unternehmen wie Saint-Gobain haben sich noch ambitioniertere Ziele gesetzt, zumindest für manche Standorte. Nur: Wie lässt sich die Klimaneutralität in der Industrie erreichen? Derzeit stecken fossile Rohstoffe in unzähligen Produkten. Sie ermöglichen den Transport per Schiff und Flugzeug und sie werden für Schmelz- und Brennvorgänge benötigt. All das zu verändern, scheint derzeit fast unerreichbar.
Stefan Lechtenböhmer vom Wuppertal Institut für Klima, Umwelt und Energie hält es aber für machbar: „Ich bin mir schon ziemlich sicher, dass wir 2045 eine klimaneutrale Industrie haben werden“, sagt er, nennt aber im nächsten Satz ein großes Aber. Die kritische Frage ist für ihn: „Insbesondere wie viel Industrie wir noch haben werden.“
Denn der Wandel zur Klimaneutralität birgt auch Risiken. Samir Khayat, der Geschäftsführer der NRW-Landesgesellschaft für Energie und Klimaschutz, ist optimistisch: „Ich denke so ein bisschen an das deutsche Wirtschaftswunder nach dem Krieg, das auch dadurch entstanden ist, dass die ganzen alten Anlagen weg waren und man etwas Neues bauen musste. Und so ein bisschen diesen Effekt, den werden wir auch bekommen. Es wird eine neue, grüne, innovative und technologisch fortschrittliche Industrie geben. Das ist der Plan.“
Der geht aber nur auf, wenn der Wandel gut organisiert wird. Sonst kann es auch anders kommen. Es könnte zum Beispiel passieren, dass Deutschland seine Industrie umbaut, die neuen, grünen Produkte aber zu teuer sind und wenig gekauft werden. Dann würden Firmen pleitegehen. Oder es könnte passieren, dass Unternehmen ins Ausland ziehen, weil dort grüner Strom günstiger ist.
„Ja, die Gefahr besteht natürlich“, räumt der Industrieexperte Samir Khayat ein. Es müsse durch kluge Wirtschaftspolitik vermieden werden. Einfach abwarten und nichts tun, ist für ihn keine Option: „Gewisse Risiken müssen wir eingehen. Wir sind im ganz knallharten Wettbewerb um Rohstoffe und alles andere mit anderen Staaten wie China. Da kann man sich nicht ausruhen. Entweder man bewegt sich oder wir werden absteigen als Industrienation. Wir werden nicht mit konventionellen Technologien am Weltmarkt wettbewerbsfähig bleiben.“
Im Industrieland NRW hat sich daher schon einiges getan. Insbesondere viele Großunternehmen stünden in den Startlöchern, sagt Samir Khayat:
„Für uns war es so, dass die Industrie auf unsere Landesregierung zugekommen ist und gesagt hat, wir müssen uns zusammensetzen und den Weg zur Klimaneutralität finden und beschreiben. Da stand im Raume: Wir müssen in der Industrie 56 Millionen Tonnen CO2 in den nächsten Jahren einsparen und wir haben keine Ahnung, wie wir das konkret machen sollen. Das war vor etwa vier Jahren.“
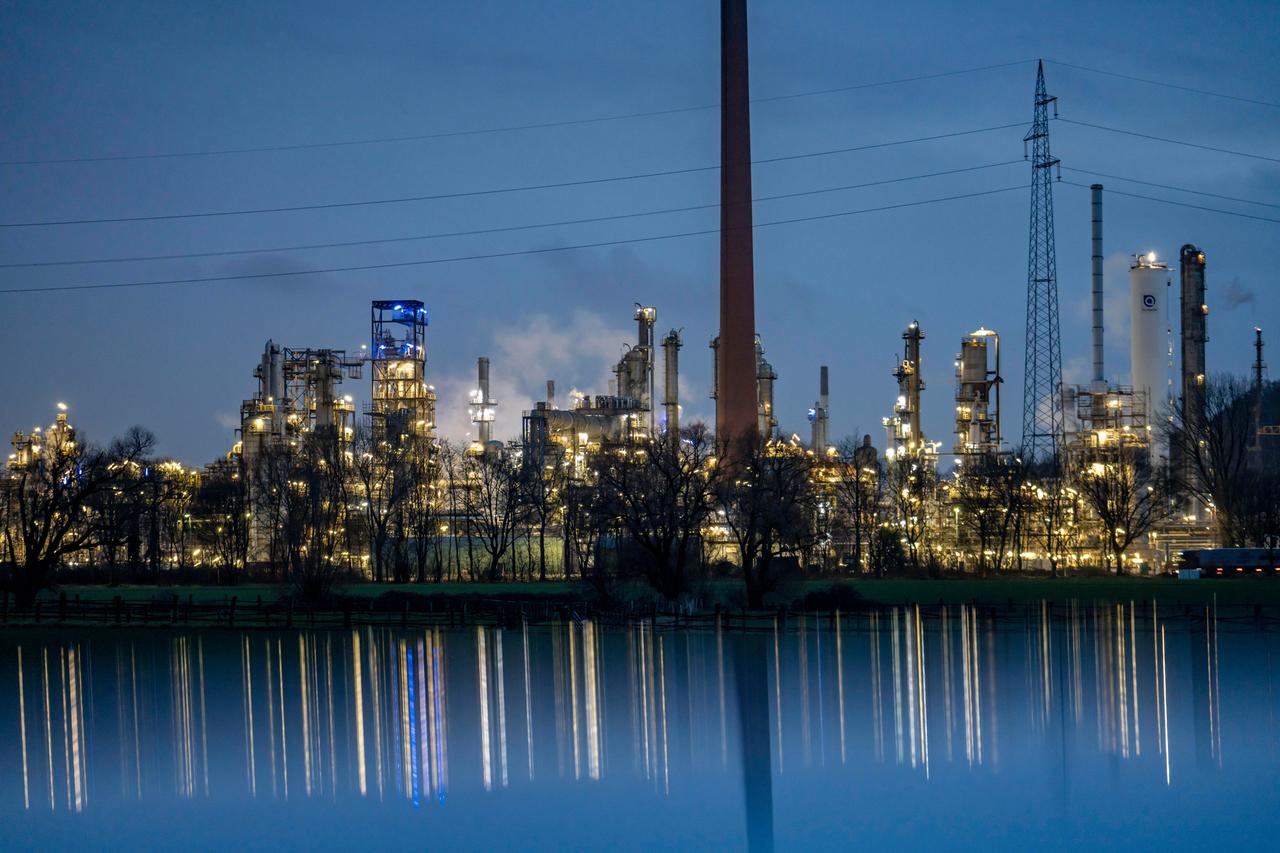
Landespolitik, Wissenschaft und Industrie haben daraufhin ein gemeinsames Konzept entwickelt. Es erklärt Schritt für Schritt, wie die Klimaneutralität erreicht werden kann. Der erste Schritt sei, dass Unternehmen so viel Energie wie möglich einsparen, sagt Samir Khayat. Zum Beispiel durch moderne Maschinen und eine smarte Beleuchtung. Doch das reiche nicht. Der nächste Schritt sei, dass Unternehmen Prozesse elektrifizieren: „Das heißt, wir haben ja viele Prozesse, die laufen mit fossilen Brennstoffen: mit Kohle, mit Öl, mit Gas. Da kann man aber viele auf elektrischen Strom umstellen.“
Und zwar auf grünen Strom, so dass keine Treibhausgase mehr anfallen. Wie das gehen kann, zeigt die Glasproduktion von Saint-Gobain bei Aachen.
„Wir gehen mal rum. Und dann sehen Sie, welche Menge an Energie hier eigentlich jeden Tag reinfließt.“
Forschungsdirektor Stephan Behle führt zu einem kleinen Guckloch an einer Seite der sogenannten Glaswanne. Dort sieht man, dass im Inneren der Anlage ein Flammeninferno tobt, es herrschen Temperaturen von bis zu 1000 Grad Celsius.
„Und das ist im Wesentlichen heute Erdgas getrieben. 80 Prozent heute ist Erdgas, der Rest ist Strom.“
Durch den anstehenden Umbau der Wanne will Stephan Behle das Erdgas überflüssig machen und deutlich mehr Strom einsetzen. Dazu muss allerdings der gesamte Prozess neu gedacht werden. Mit Erdgas heize man das Glas von oben, sagt Behle. Die Flammen stünden in der Wanne über dem flüssigen Glas. Nutze man mehr Strom, müsse man von unten heizen – so als würde man die Glaswanne auf eine sehr große heiße Herdplatte stellen. Das hat Folgen: „Flüssiges Glas: Das fängt an zu rotieren. Wenn es heiß ist, steigt es auf und wenn es kalt ist, fällt es runter. Jetzt drehen Sie aber die Beheizung um, das heißt die ganze Glaswalze – wie wir das nennen – fängt an, anders herum zu rotieren.“
Flüssiges Glas wirkt allerdings wie Schmirgelpapier: Es schleift stark. Dreht es sich am Boden der Wanne, geht diese deutlich schneller kaputt. Man braucht also neue Materialien, neue Steine, aus denen man solche Wannen bauen kann, sagt Behle: „Die Steine müssen dicker werden, die müssen wahrscheinlich auch aus anderem Material gemacht werden.“
Daran forschen seine Mitarbeitenden nun. Das Beispiel zeigt: Die Umstellung von Öl und Gas auf Strom ist oft machbar – aber nicht immer einfach. Und es gibt Fälle, bei denen Unternehmen mit Strom nicht weiterkommen. Dann brauchen sie grünen Wasserstoff – also Wasserstoff, der mit grüner Energie erzeugt und daher klimaneutral ist. Stefan Lechtenböhmer vom Wuppertal Institut für Klima, Umwelt und Energie: „Wasserstoff ist deswegen ein Stück weit die zweite Wahl, weil natürlich die Umwandlung von Strom in Wasserstoff Energie kostet.“
Sprich: Grünen Strom direkt zu nutzen, ist immer effizienter. Aber manchmal geht es eben nicht. Stephan Behle zum Beispiel braucht den grünen Wasserstoff in der Glasproduktion als Ergänzung zu grünem Strom. Und in der Stahlherstellung sei ohne grünen Wasserstoff gar nichts zu machen: „Das ist sehr, sehr energieintensiv. Das kann man theoretisch auch direkt mit Strom, aber soweit ist die Technik noch nicht.“
Eine neues Verfahren für die Herstellung von Stahl mit grünem Wasserstoff zu entwickeln – das ist die Aufgabe von Marie Jaroni. Die Managerin steht auf dem Firmengelände von ThyssenKrupp in Duisburg und zeigt auf zwei rechteckige Türme, an den außen dicke Schornsteine und Rohre entlanglaufen:
„Wir stehen gerade vor unseren kleineren Hochöfen. Dem Hochofen 8 und dem Hochofen 9“, sagt sie. Dort schmilzt das Unternehmen Eisenerz und Kohle und macht daraus Roheisen. „Das wird so übereinandergeschichtet und dann klaut die Kokskohle dem Eisenerz den Sauerstoff und dann kommt unten Eisen raus und oben CO2.“
Die Türme sind ein Symbol für eine Industrie, die es bald nicht mehr geben soll: fossil und schmutzig.
„Der Hochofen 8 ist der schön rot angemalte. Der ist 2007 in Betrieb genommen worden und damit wahrscheinlich auch der letzte Hochofen, der in Europa überhaupt in Betrieb gegangen ist“, sagt Jaroni. Sie will mit ihrer Arbeit dazu selbst beitragen: Für die Herstellung von Stahl mit Wasserstoff brauche es ganz neue Prozesse und Anlagen, sagt sie. „Das wäre alles komplett weg. Und noch viel mehr hier auf dem Gelände: Der ganze Kohlebereich im Hafen, die Kokerei, das brauchen wir dann alles nicht mehr. “
Die neuen Anlagen gibt es bisher nur in einem Schaukasten. Marie Jaroni führt zu einem Firmengebäude und dort im Foyer zu einem Glaskasten mit einem circa 50 Zentimeter hohen 3D-Modell. Auf den ersten Blick unterscheidet es sich gar nicht so sehr von den bisherigen Hochöfen: Die neue Anlage besteht ebenfalls aus einem großen Turm mit mehreren Röhren und Schornsteinen. Der große Unterschied passiere im Inneren.
„In der Direktreduktionsanlage reduzieren wir das Eisenerz mit dem Wasserstoff“, sagt Jaroni und zeigt auf den oberen Teil der Anlage. Man mische also das Erz mit Wasserstoff, nicht mehr mit Kohle. Dadurch entsteht als „Abfallprodukt“ kein CO2 mehr, sondern nur noch Wasserdampf. In der Anlage verbleibt ein Zwischenprodukt, das Marie Jaroni „Eisenschwamm“ nennt: „Dann gehts weiter runter und unten steht der sogenannte Einschmelzer. Der nimmt dann den Eisenschwamm, schmilzt den nochmal und ganz unten kommt dann unser sogenanntes Roheisen 2.0 raus, das wieder ins Stahlwerk geht.“
Die neue Anlage soll 2026 in Betrieb gehen, zunächst mit Erdgas, dann soll nach und nach binnen eines Jahres auf grünen Wasserstoff umgestellt werden. Für Marie Jaroni ist daher wichtig, dass in Deutschland bald in großem Umfang grüner Wasserstoff hergestellt wird:
„Wir müssen sicherlich die Wasserstoffwirtschaft im Beginn unterstützen in Deutschland und Europa. Weil bis wir Importe aus dem Ausland bekommen, wird das ein paar Jahre dauern. Es gibt noch keine Pipelines nach Rotterdam und so weiter und so fort“, sagt Marie Jaroni und meint mit Ausland Länder jenseits der EU. Sie hofft, dass die Politik in dieser Hinsicht schnelle Fortschritte macht.
Die Umstellung der Produktion auf grünen Strom und – wo das nicht geht – auf grünen Wasserstoff: Das sind also die wichtigsten Voraussetzungen dafür, dass die Industrie klimaneutral werden kann. Es gebe aber einige Bereiche, wo weder das eine noch das andere möglich sei, sagt Stefan Lechtenböhmer vom Wuppertal Institut. Dort werde auch in Zukunft CO2 anfallen: „Zum Beispiel die Zementindustrie, die Kalkindustrie – das sind die größten, die einfach prozessbedingt CO2 erzeugen. Also wenn sie Zement erzeugen, müssen sie Kalk brennen. Dabei entsteht prozessbedingtes CO2, das können sie nicht vermeiden.“
Das Gleiche gilt für die Müllverbrennung. Und auch für die Luftfahrt gibt es bisher keine wirklich klimaneutralen Lösungen. Die Frage ist daher: Was macht man mit diesen verbleibenden Treibhausgasen?
„Die müssen wir entweder auffangen und im Untergrund lagern. Das geht“, sagt Samir Khayat von der NRW-Landesgesellschaft für Energie und Klimaschutz. Und: Es sei in großem Maße nötig. „Und dann gibt es noch die Möglichkeit, CO2 in der chemischen Industrie zu nutzen.“
Und zwar als Rohstoff für neue Produkte. Daran forschen zum Beispiel die Unternehmen Siemens Energy und der Chemiehersteller Evonik in ihrem Projekt „Rheticus“. Die Unternehmen nutzen CO2, um Spezialchemikalien herzustellen. Dafür verarbeiten sie das CO2 mit Wasser und grünem Strom zu Synthesegas und lassen das Gas von speziellen Bakterien zu Chemikalien umwandeln.
Martin Demler ist der Betriebsleiter der Evonik-Pilotanlage im Chemiepark Marl:
„Hier stehen wir vor der Rheticus Pilotanlage.“ Er zeigt auf einen runden, circa acht Meter hohen Edelstahlbehälter. Darin schwimmen in einer Nährstofflösung die Bakterien, die das mit CO2 hergestellte Synthesegas umwandeln. Würde man in den Behälter hineinblicken, sähe man eine milchig-beige Flüssigkeit, sagt Demler: „Das kann man auch vergleichen mit Bäckerhefe. Die Farbe ist vergleichbar.“
Evonik leitet kontinuierlich kleine Mengen Synthesegas in die Lösung. Darin schwimmen zwei Arten von Bakterien: Die erste nimmt das Gas auf, nutzt es zum Wachsen und scheidet – quasi als „Abfallprodukt“ – Kohlenstoff aus. Die zweite Art von Bakterien setzt diese Kohlenstoff-Teilchen zu langen Kohlenstoffketten zusammen, zu sogenanntem C6. Das ist für Demler und seine Kolleginnen und Kollegen wertvoll, denn C6 ist ein gefragter Rohstoff in der Industrie. Es kommt unter anderem in Kosmetik zum Einsatz. Evonik muss das C6 dann aus der Nährlösung herausfiltern und kann es verkaufen.
Die Nachfrage nach solchen klimaneutral hergestellten Inhaltsstoffen in der Chemiebranche wachse, sagt der Rheticus-Projektleiter bei Evonik, Thomas Haas:
„In den letzten Monaten ist das durch die Energiekrise etwas ins Stocken geraten. Das heißt aber nicht, dass es verschwunden ist. Im Gegenteil: Die Nachfrage hat enorm zugenommen, insbesondere in Europa. Und ich denke, in Zukunft wird das noch weiter so gehen.“
Für Stefan Lechtenböhmer vom Wuppertal Institut zeigt das: Dass in manchen Bereichen der Industrie weiter CO2 anfällt, ist gar nicht so schlimm – vorausgesetzt man kann es speichern oder als Rohstoff für neue Produkte nutzen und dann auch bei der Müllverbrennung immer wieder auffangen: „Sonst haben wir’s nur einmal mehr genutzt. Aber dann hat man’s auch wieder in der Atmosphäre. Langfristig muss es dahingehen, das CO2 dauerhaft im Kreis zu binden.“
Technologisch machbar ist das – genauso wie die Umstellung auf grünen Strom und grünen Wasserstoff. Die Frage ist daher: Warum warten so viele Unternehmen ab? Warum stellen nicht schon jetzt viel mehr Unternehmen auf eine klimaneutrale Produktion um, obwohl klar ist, dass das Klima am Limit ist?
„Weil es zu teuer ist“, sagt Samir Khayat von der Landesgesellschaft für Energie und Klimaschutz in NRW. Das gelte teilweise für den Bau neuer Produktionsanlagen, aber auch für deren Betrieb. Denn grüner Strom ist in Deutschland knapp und damit teurer als fossile Energie – auch weil frühere Bundesregierungen die Erzeugung zu wenig ausgebaut haben.
„Wir werfen den Motor gerade wieder neu an. Da steckt natürlich schon drin, dass wir uns in den vergangenen Jahren allzu sehr auf die faule Haut gelegt haben, was den Ausbau der erneuerbaren Energien angeht.“
Die hohen Kosten klimaneutraler Produkte
Die hohen Kosten führen dazu, dass klimaneutrale Produkte am Markt teurer sind als fossil erzeugte – und sich schlechter verkaufen lassen.
Chemikalien, die aus CO2 hergestellt werden, wären bei den aktuellen Energiepreisen zum Beispiel etwa drei Mal so teuer wie aus Erdöl produzierte, sagt Thomas Haas von Evonik. Auch weil sie einfach deutlich mehr Energie in der Herstellung brauchen:
„Der nächste Schritt ist zum Beispiel, Kunden zu finden, die sagen, wir kaufen diese Produkte auch, wenn sie teurer sind als ein Produkt aus Erdöl. Das denkt man vielleicht, wäre selbstverständlich. Aber ist es eben nicht.“
Weder bei den Kosmetikherstellern, die Evonik die Chemikalien abkaufen. Noch bei den Verbraucherinnen und Verbrauchern, die dann im Laden lieber zu günstigeren Alternativen greifen. Industrieexperte Samir Khayat:
„Die Industrie wird und kann jetzt nicht in Verfahren investieren, deren Produkte am Weltmarkt nicht absetzbar sind. Also braucht es zumindest für einen Übergangszeitraum Maßnahmen und Förderbedingungen, um das aufzufangen.“
Das sehen auch die Unternehmen so. Der Stahlhersteller Thyssenkrupp zum Beispiel veranschlagt zwei Milliarden Euro für den Bau seiner klimaneutralen Produktionsanlage. Die Förderanträge beim Bund laufen. Und an ihnen hängt der Erfolg:
„Wir können die Investition nicht ohne Förderung stemmen. Das würden wir nicht machen können und damit auch nicht weiter eine Roheisenproduktion in Deutschland darstellen können“, sagt Marie Jaroni.
Und Thomas Haas von Evonik sagt, auch die Nutzung von CO2 als Rohstoff für Spezialchemikalien sei ohne finanzielle Förderung im industriellen Ausmaß nicht rentabel: „Es müsste eine Kompensation in der Art da sein, damit die Technologie auch in Deutschland und Europa wirtschaftlich ist. Und nicht in anderen Kontinenten gebaut werden muss.“
Wo die Energiekosten günstiger sind. Da ist es wieder: Das Risiko, dass durch den Wandel zur Klimaneutralität Firmen abwandern. Damit das nicht passiere, brauche es neben direkten Investitionsförderungen weitere Maßnahmen, sagt Stefan Lechtenböhmer vom Wuppertal Institut:
„Ausbau der erneuerbaren Energien und der zugehörigen Infrastruktur ist natürlich ganz, ganz primär. Dann muss man die Instrumente jetzt noch stärker einsetzen, die man hat, zum Beispiel die Contracts for Difference.“
Unternehmen fordern Planungssicherheit
Dabei sollen Unternehmen einen finanziellen Ausgleich vom Staat erhalten, wenn die Vermeidung von CO2 mehr Geld kostet als der Kauf vom Emissionszertifikaten. Das soll sicherstellen, dass klimaneutrale Produkte nicht teurer sind als fossil hergestellte. Stephan Behle von Saint-Gobain wünscht sich vor allem schnelle Klarheit: „Wir brauchen Planungssicherheit. Also eine Sicherheit über die nächsten 10, 15 Jahre. Das ist natürlich nicht einfach. Aber es müsste mal klar sein, wo geht denn die Reise hin.“
Und er wünscht sich einfachere Regelungen mit weniger Bürokratie. Eigene Windräder am Firmenstandort Herzogenrath aufzubauen, um grünen Strom vor Ort zu produzieren, sei zum Beispiel schwierig: „Weil die Abstände nicht passen, die Planungsverfahren nicht greifen oder teilweise viel zu lange dauern. Also die Zulassung von Windrädern: Wenn Sie sehr schnell sind, sind Sie vielleicht mit zwei bis zweieinhalb Jahren dabei. Und im Mittel, habe ich gehört, liegen Sie bei sieben Jahren.“
Immerhin: Dazu tritt im Februar ein bundesweites Gesetz in Kraft, das den Ausbau der Windkraft beschleunigen soll. Behle wird mit seinem Team weiter daran arbeiten, eine klimaneutrale Glasproduktion in Herzogenrath hinzubekommen. Dabei steht der Manager durchaus ein wenig unter Druck: „Wir sind hier vielleicht einer der Piloten. Das heißt man guckt hier auch hin. Sowohl vom Land als auch von der Zentrale in Paris.“
Also am Hauptsitz von Saint-Gobain. Stephan Behle nimmt das sportlich: „Wir würden gerne die Ersten in der Welt, zumindest aber gerne die Ersten in Europa werden.“
Das wäre gut für den ganzen Standort in NRW, sagt er: Für die Zulieferer, für die Universität Aachen, mit der Saint-Gobain zusammenarbeitet. Und für die Mitarbeiterinnen und Mitarbeiter, die dadurch wichtiges Know-how aufbauen. Und: Es ist wichtig, für Saint-Gobain selbst.