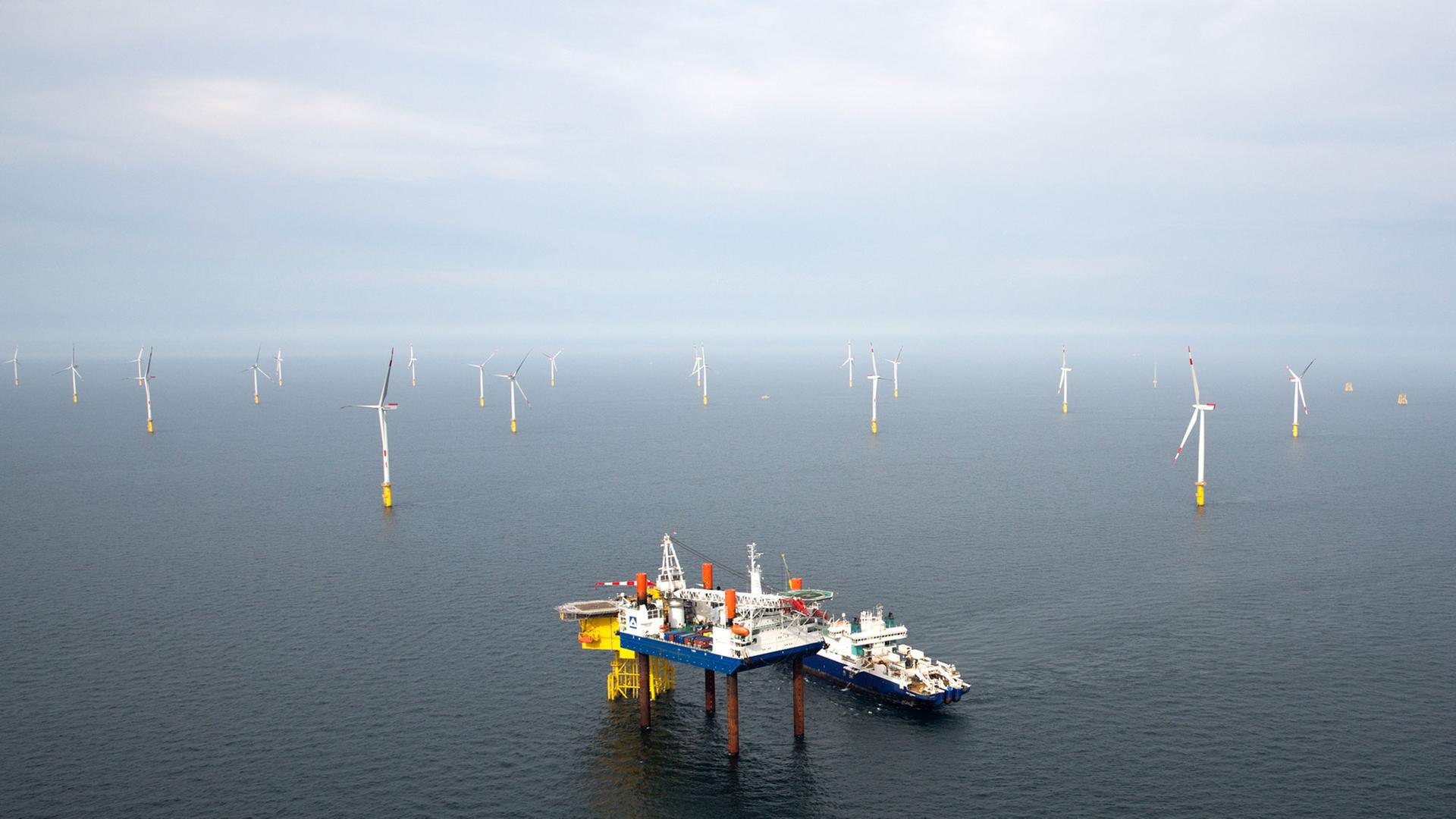
"Im schlimmsten Fall kann die Windenergieanlage umfallen, weil ein Riss drin ist und die Struktur versagt. Und da kann sich sicher jeder vorstellen, dass das sowohl ökonomisch ein großer Verlust ist als natürlich auch sicherheitstechnisch."
Damit es soweit erst gar nicht kommt, hat Bianca Weihnacht vom Fraunhofer-Institut für Keramische Technologien und Systeme in Dresden gemeinsam mit ihren Kollegen eine Methode entwickelt, mit der sich Schweißnähte an den Stahlpfeilern kontinuierlich überwachen lassen. Es ist eine Manschette, in die in regelmäßigen Abständen Ultraschallköpfe eingesetzt sind.
"Die senden in alle Richtungen Ultraschallwellen aus. Und da wo sich kein Riss befindet, wird nichts reflektiert. Also da kann man davon ausgehen, dass das Material intakt ist."
Denn Ultraschallwellen werden an nur an den Stellen reflektiert, an denen sich die Dichte des Mediums ändert. Das passiert zum Beispiel, wenn die Wellen statt auf Stahl plötzlich auf die Luft in einem Riss stoßen.
"Und die gleichen Ultraschallköpfe - oder bei uns sind das so kleine piezokeramische Sensoren, die da eingebettet sind in eine Manschette - die gleichen Sensoren können sowohl senden als auch empfangen und können dann also auch das reflektierte Signal wieder aufnehmen."
Regelmäßige Prüfungen sind gesetzlich vorgeschrieben
Die Daten werden dann an die Windparkbetreiber übertragen und die können dafür sorgen, dass die Risse repariert werden. Ein Viertel aller Stahlpfeiler in einem Offshore-Windpark muss pro Jahr inspiziert werden. Das schreibt der Gesetzgeber vor. Bislang fahren dafür Taucher raus und schauen sich jede Schweißnaht einzeln an. Diese zeitintensive Arbeit könnten die Manschetten mit den Ultraschallköpfen darin übernehmen. Dann müssten die Taucher nur noch ins Wasser, um die Manschetten an den Stahlpfeilern anzubringen - dort wo diese zusammengeschweißt wurden. Ausprobiert haben Bianca Weihnacht und ihre Kollegen ihr System an einem Stück Stahlrohr, dass sie - mit der Ultraschallmanschette versehen - im Hafenbecken von Rostock versenkt haben.
"Dort hat es sehr gut funktioniert. Also der Verfahrensnachweis ist erbracht und jetzt bemühen wir uns, das ganze in eine Form zu bringen, dass es von den Tauchern gut gehandhabt werden kann. Also dass man diese doch etwas anderen Anforderungen erfüllt, als wenn man jetzt onshore sich das anschaut. Und wir arbeiten daran, dass die Zuverlässigkeit eben dann im Endeffekt auch die 20 Jahre erfüllen kann."
Prüfung nur an gefährdeten Stellen
20 Jahre sind die erhoffte Lebensdauer einer jeden Windenergieanlage auf See. So lange sollten auch die Ultraschallköpfe halten. Taucher wären dann nur noch nötig, um die Manschetten anzubringen, sie zu warten und eventuell die Batterien auszuwechseln. Bianca Weihnachts Idee ist es, die Manschetten nicht an jeder Schweißnaht einer Windenergieanlage anzubringen, sondern nur an den besonders stark beanspruchten und für Risse anfälligen Stellen.
"Wir haben Kontakte zu verschiedenen Windparkbetreibern. Die haben großes Interesse daran, weil sie ja verpflichtet sind, ihre Windenergieanlagen auch zu überwachen. Wir arbeiten auch daran, dass das in den Regularien eingebracht wird, dass sie zum Beispiel Sichtprüfung weglassen können. Man kann sich vorstellen: Wenn ein Taucher dort nur eine halbe Stunde tauchen kann, dauert es recht lange, bis man so einen Windpark inspiziert hat. Die Schiffe sind teuer. Man möchte eigentlich das etwas schneller erledigen und so eine Manschettentechnologie wäre da sehr günstig dafür."