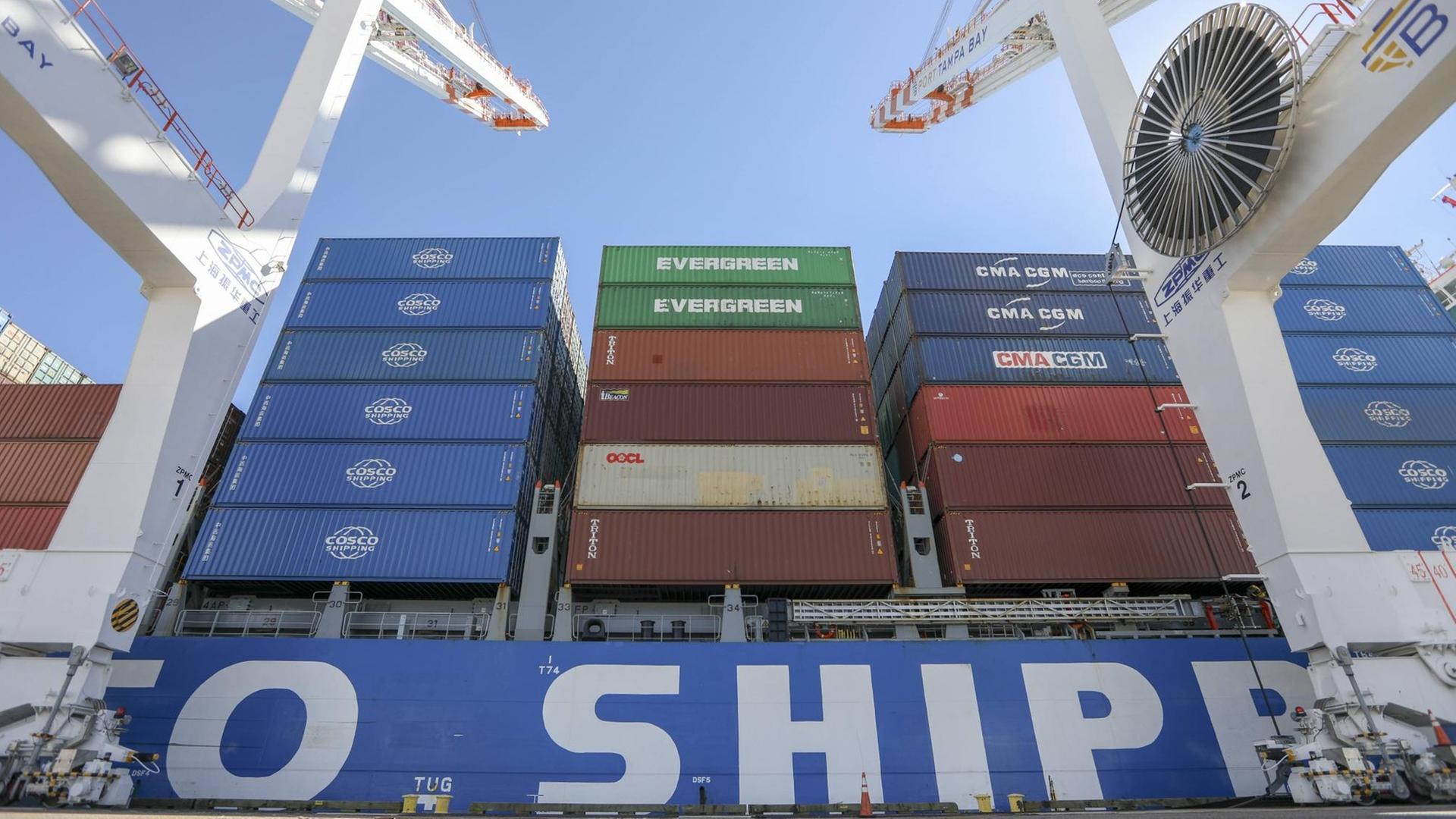
Berlin-Reinickendorf. Ein Gewerbehof. Auf Halle 7 steht noch der Name der Vormieter. Die neue Firma hatte erst einmal alle Hände voll damit zu tun, eine Produktion von FFP2-Masken aufzubauen. Innen läuft nun seit Mitte Februar von großen Rollen Vlies in Maschinen. Sie stanzen automatisch jede Maske aus, formen sie, versehen sie mit Tragegummis und stempeln den Firmennamen "Your Mask" auf. Mehr als 100.000 Mal am Tag. Mitgründer und Geschäftsführer Matay Erdinc:
"Wir haben angefangen mit zwei Produktionslinien. Dann haben wir im Dezember gleich die dritte dazu genommen, während wir eigentlich in den Anfängen waren, und haben mittlerweile auch schon die vierte Produktionslinie bestellt."
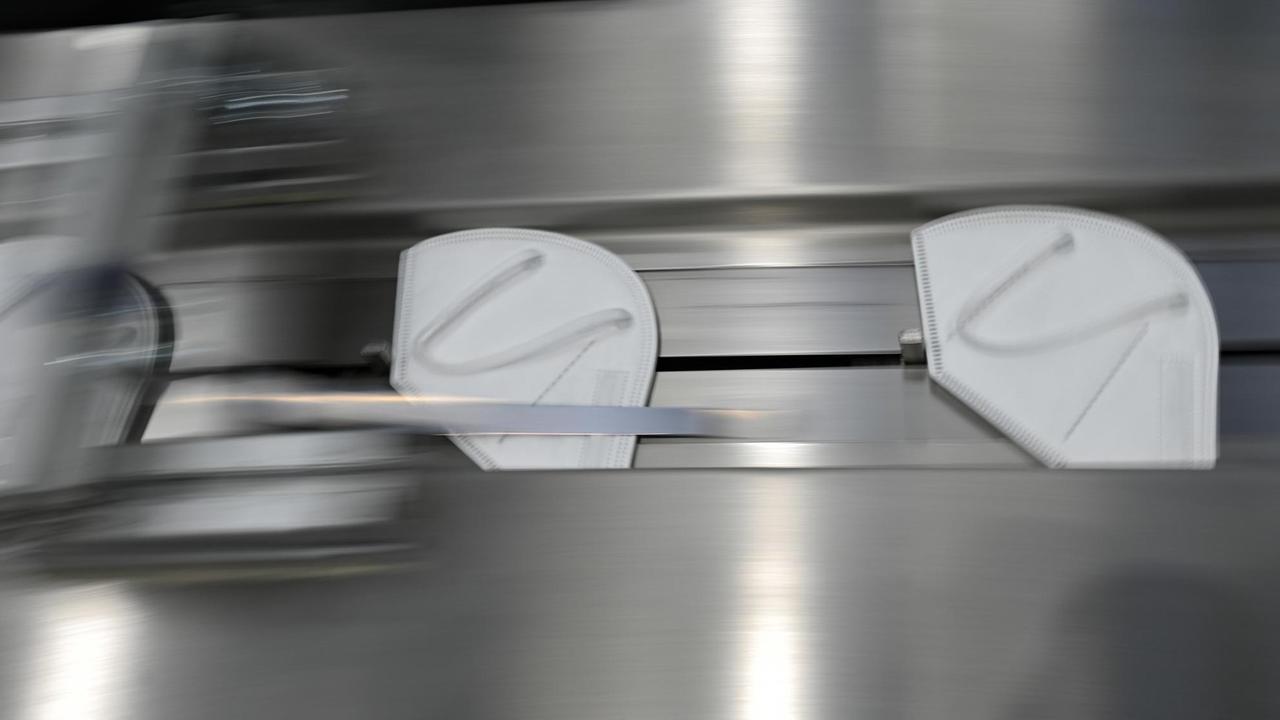
Innerhalb von sieben Monaten baute der gelernte Goldschmied gemeinsam mit seinen beiden Brüdern die Produktion auf. Keiner der drei ist vom Fach, trotzdem haben sie fast drei Millionen Euro investiert. Ihre Bank scheute das Risiko, als sie nach dem ersten Lockdown ihre Idee vortrugen.
"Dann sind wir mit diesen Plänen zur Bank und haben gesagt, hier, wir möchten das gerne machen. Wir glauben daran, dass die Pandemie noch nicht vorbei ist, und die Bank hat nur den Kopf geschüttelt, und so was finanziert keine Bank einfach so. Also wir haben das alles mit keiner Risikobeteiligung der Bank, sondern wirklich mit einer vollen Bürgschaft haben wir das selber finanziert, natürlich über einen Kredit, aber wir haben selber dafür gebürgt."
2020: Viele Lieferketten waren unterbrochen
Offensichtlich gab es Bedarf. Denn zu Beginn der Pandemie fehlten im Frühjahr 2020 in Deutschland Desinfektionsmittel, persönliche Schutzausrüstungen oder medizinische Masken. Viele Lieferketten waren unterbrochen. Der Leiter der Beschaffung bei der Hamburger Unternehmensgruppe Körber Michael Stietz:
"Was uns überrascht hat, muss man sagen, war die Geschwindigkeit wie die Logistikketten zusammengefallen sind, gerade im Bereich der Luftfracht, als auch in der Seefracht. Das war schon fast historisch einmalig, wie das zum Erliegen kann."
Ein hoher Anteil des Luftfrachtvolumens entfällt auf Passagier-flugzeuge. Als die nicht mehr flogen, brachen Transportkapazitäten weg.
"Das ist glaube ich etwas, was viele Unternehmen nicht im Bild hatten." Der Präsident des Kieler Instituts für Weltwirtschaft Gabriel Felbermayr. "Es gab in der Tat gravierende Lieferkettenprobleme in der ersten Phase der Pandemie, da sprechen wir also über April, Mai in etwa. Und das hat zum einen zu tun mit dem Ausfall von Lieferanten in China und dann ein paar Wochen später mit dem Ausfall von Lieferanten vor allem in Norditalien. Das hat aber nicht lange gedauert, und schon im Mai und dann im Sommer hinein kann man von einer vollständigen Normalisierung der Zulieferstrukturen sprechen."
Zu abhängig von anderen Weltregionen?
Die Politik reagierte. Das Bundeswirtschaftsministerium förderte beispielsweise mit 100 Millionen Euro die Herstellung von Masken und Vlies, um in Deutschland eine Produktionskapazität von jährlich zehn Milliarden Masken zu schaffen. Bundeskanzlerin Angela Merkel griff das Thema Lieferketten im Januar 2021 bei einer Videokonferenz des Weltwirtschaftsforums auf:
"Lieferketten haben sich nicht bewährt in Zeiten der Pandemie zum Teil, sind zerbrochen. Und wir müssen jetzt, bei Lehren aus der Pandemie, fragen: Sind das Schwachstellen, wenn wir zu abhängig sind von globalen Lieferketten? Oder wie machen wir solche Lieferketten so stabil und so verlässlich für die Zukunft, dass sie auch in Zeiten des großen Stresses halten?"
Haben sich europäische Hersteller auf der Suche nach Kostenvorteilen zu stark von Lieferanten in anderen Weltregionen abhängig gemacht, ob bei Mikrochips, medizinischen Schutzausrüstungen oder pharmazeutischen Wirkstoffen? Alleine aus China kämen 30 Prozent der importierten Grundstoffe für die Arzneien, heißt es in einer Studie des arbeitgebernahen Instituts der Deutschen Wirtschaft.
"Die Analyse belegt keine dominierende Abhängigkeit der deutschen Arzneimittelproduktion von Vorleistungen aus China. Gleichwohl können punktuelle Abhängigkeiten bei einzelnen Produkten gerade im niedrigpreisigen Segment von wenigen chinesischen Wirkstofflieferanten bestehen."
"Kunden wollen mehr Produktion in westlichen Ländern sehen"
Auch die Unternehmen reagieren. So will der französische Pharmahersteller Sanofi in Europa einen weltweit führenden Wirkstoffhersteller schaffen. Evonik, das zweitgrößte deutsche Chemieunternehmen, baut seine Wirkstoffproduktion auf dem Heimatkontinent ebenfalls aus. Der Essener Konzern hat in einem ersten Schritt 25 Millionen Euro in zwei hiesige Werke investiert. Der Leiter Forschung und Entwicklung Healthcare Stefan Randl:
"Wir hatten tatsächlich auch schon vor der Coronapandemie 2019 die Entscheidung getroffen, an unseren deutschen Standorten in Hanau und Dossenheim, Dossenheim ist ein Vorort von Heidelberg, zu investieren. Aufgrund der Tatsache, dass die Kunden einfach mehr Produktion in westlichen Ländern sehen wollen."
Warum verlangen die Industriekunden von Evonik danach?
"Ja, also Risikominimierung spielt da sicher auch eine Rolle."
Hyperglobalisierte Produktion "in Frage gestellt"
Rückblende: Nach dem Fall der Mauer produzierten ab Anfang der 1990er-Jahre immer mehr Firmen an billigeren Standorten oder lagerten Teile der Fertigung an Zulieferer aus, europäische Unternehmen oft nach Mittel- und Osteuropa und Asien. China avancierte zur Werkbank der Welt. Heute finden rund 12 Prozent der weltweiten und 17 Prozent der deutschen Wertschöpfung in globalen Lieferketten statt. Ökonomin Dalia Marin von der Technischen Universität München:
"Man produziert mit den niedrigen Löhnen in den Billiglohnländern, und wenn die Transportkosten hinreichend niedrig sind, dann sind die Kosten in der Produktion mit Lieferketten weitaus niedriger, als wenn man hier in Deutschland eine Arbeitskraft einstellt."
Die Produktion außerhalb Europas war aus weiteren Gründen billiger. Wegen laxerer Umweltvorschriften, geringerer Steuern und schwacher Gewerkschaften. Manche Unternehmen verabschiedeten sich gar komplett von einer eigenen Produktion.
"Das war eine sehr günstige Produktionsweise in der Vergangenheit, in der so genannten Periode der Hyperglobalisierung, die mit dem Fall der Mauer begann und mit der Finanzkrise endete. Aber diese Produktionsweise ist jetzt in Frage gestellt worden durch die gestiegene Unsicherheit, die es durch die Pandemie gibt."
Unübersichtlich lange Lieferketten
Wenn in Europas Öffentlichkeit über Probleme in den Lieferketten diskutiert wurde, dann ging es um die Ausbeutung von Arbeitern in Minen und Textilfabriken und um Umweltskandale, aber nicht um Risiken der Beschaffung. Sie funktionierte ziemlich reibungslos. Tatsächlich wurden die Lieferketten sogar immer länger und viele Unternehmen wussten gar nicht, wer alles an ihren Lieferketten beteiligt ist. Erst in der Pandemie nahm die breite Öffentlichkeit die Risiken wahr, die mit diesem Produktionsregime verbunden sind. Für einige Unternehmen erwies sich bereits der Reaktorunfall im japanischen Fukushima 2011 als Weckruf.
"Fukushima war so das erste Mal, wo es richtig hochkam, dass die Leute festgestellt haben, meine Lieferkette ist unterbrochen. Weil ich zwar meinen ersten Lieferanten kenne, also meinen Tier-1-Lieferanten, aber gar nicht weiß, von wem kriegt der denn seine Bauteile und von wem kriegt der, der die Bauteile macht, denn wieder seine Einzelteile. Und wenn ich diese Transparenz nicht habe, dann habe ich tatsächlich ein Risiko in meiner Lieferkette, und das wurde durch Corona jetzt noch mal befeuert und offensichtlicher."
Jan-Hendrik Sohn verantwortet den Vertrieb für mehrere europäische Länder für die US-Firma Ivalua. Sie bietet Unternehmen Softwarelösungen für die Beschaffung an, wobei die Handhabung von Risiken eine wichtige Rolle spielt. Der Manager beobachtet ein Umdenken. In den vergangenen Jahren hätten Unternehmen zunehmend auf mehr als einen Lieferanten je Warenteil gesetzt.
"Wenn sie betrachten vor drei, vier, fünf Jahren haben die Unternehmen in der Regel denjenigen ausgewählt, der am billigsten liefert. Dann hat man festgestellt, der Billigste ist vielleicht nicht immer der Beste. Also habe ich eine Strategie gewählt, mehrere Anbieter für dasselbe Los zu wählen und habe hundert Prozent aufgeteilt in vielleicht zwei Mal 50 Prozent oder habe ausgewählt in ein Lieferant pro Kontinent, ein Lieferant pro Teilwarengruppe."
"Ein-Lieferanten-Strategie ist hochgefährlich"
Aber es gibt trotzdem noch große Abhängigkeiten.
"Wir sind in Deutschland, Stand heute, nicht in der Lage eine Kopfschmerztablette zu produzieren, weil wir alles nach China gegeben haben. War gut. War günstig. Wenn wir es heute versuchen würden wieder Kopfschmerztabletten zu produzieren, hätten wir ein Problem, und das ist das Problem, was aus dieser Konzentration sich ergibt. Und ich sehe im Moment oftmals den Trend, dass man halt genau versucht wieder Dinge zurückzuholen und Dinge halt zu entzerren. Ein-Lieferanten-Strategie für mehr Dinge ist einfach hochgefährlich."
Wenn Lieferketten reißen, sei es zu spät zum Handeln. Der Manager der Hamburger Unternehmensgruppe Körber Michael Stietz:
"Denn einen Lieferanten aufzubauen, ihn fähig zu machen, dass er bei uns liefern und leisten kann, da liegen wir in einer Zeit zwischen zehn Wochen bis hin zu teilweise drei bis vier Monaten, bis ein Qualifizierungsprozess durchlaufen ist. Das heißt, eigentlich müssen wir immer damit rechnen, dass Unwägbarkeiten passieren und deswegen eben das Lieferantenportfolio konsequent und kontinuierlich immer wieder hinterfragen und darauf abstimmen, was wäre, wenn?"
Näher heißt nicht automatisch resilienter
Aber alle Risiken lassen sich nicht ausschalten, erklärt der Ökonom Gabriel Felbermayr.
"Wirtschaftliche Ausfallrisiken gibt es in jedem Lieferantennetzwerk. Es kann immer ein wichtiger Lieferant pleitegehen, ob der jetzt in China sitzt, in den USA oder in Bayern. Es kann immer auch technische Probleme geben. Und wenn man jetzt sozusagen einfach nur die Produktion näher heranholt, heißt das noch nicht, dass damit die Resilienz verbessert ist."
Verstärkt haben sich jedoch die politischen Risiken. Was tun, wenn sich zum Beispiel die USA oder China in einer Krise unkooperativ verhalten?
"Das sie also sagen könnten, bestimmte Wirkstoffe für bestimmte Medikamente behalten wir uns in einer gesundheitlichen Notlage selber und restringieren die Exporte Dann hätte Europa und Deutschland ein Problem. Und es sind eher diese veränderten politischen Risikobewertungen, die dazu führen könnten, dass man sagt, bestimmte Dinge wie Penicillin müssen wir in bestimmten hinreichend großen Ausmaßen in Europa produzieren können, weil wir uns sonst verletzlich machen."
Eigenständige Antibiotika-Produktion im Westen
Politik und Wirtschaft ziehen auch an einem Strang, um wichtige Produktionen zu stützen. So fördert Österreich die Modernisierung eines Arzneimittelwerkes in Kundl. Der Schweizer Pharmakonzern Novartis selbst investiert dort 150 Millionen Euro. Es ist die einzige Antibiotika-Produktionsstätte der westlichen Welt, in der dieses lebenswichtige Medikament komplett hergestellt wird, vom Wirkstoff bis zur Tablette.
Wenn es um moderne Produktionsanlagen geht, fehlt es in Europa auch nicht an Know-how. So fand Firmengründer Matay Erdinc gleich in Berlin einen passenden Maschinenbauer. Früher fertigte die Firma Jonas & Redmann automatisierte Produktionsanlagen für die Solarindustrie. Als sich das Geschäft weitgehend nach China verlagerte, orientierte man sich um. In der Pandemie erweiterte sie ihr Sortiment um moderne Anlagen zur Maskenproduktion. So wird beispielsweise in der Firma der Brüder Erdinc jede Maske während der Fertigung fotografiert und automatisch analysiert, ob der Nasenbügel, die Passform oder die Trageriemen richtig sind. Fehlerhafte Teile sortiert die Maschine aus. Auch beim Maskenvlies ist Matay Erdinc in Deutschland fündig geworden:
"Wir haben gerade einen Hersteller aus Bayern. Wir haben ab kommenden Monat einen Hersteller in Nordrhein-Westfalen. Also wir haben zwei Zertifizierungen, die basierend sind auf zwei verschiedenen Modellen der Maske mit zwei verschiedenen Lieferanten. Und ja, das ist das, wo wir uns festgelegt haben, dass wir gesagt haben, wir möchten diese Lieferanten haben als dauerhafte Partner, um einfach auch die Produktion zu sichern."
Gleichzeitig schafft die Firma mitten in der Pandemie auch neue Arbeitsplätze.
"Aktuell sind wir ungefähr mittlerweile um die 50 Festangestellte und 20, die in Zeitarbeit sind. Wir wollen aber in Zukunft wirklich komplett über Festangestellte arbeiten. Das ist step by step. Wir müssen viele Leute anlernen. Wir müssen auch immer schauen, wie die Situation der Leute ist. Es gibt ein großes Angebot an Leuten, die sich anbieten."
Lohnt sich das betriebswirtschaftlich?
Wasser in den Wein gießt der Ökonom Felbermayr:
"Die einzige Frage, die man sich stellen muss, ist, ob sich das für die Unternehmer tatsächlich betriebswirtschaftlich lohnt. Wir werden ja irgendwann Mal, hoffentlich bald, keine Masken mehr tragen müssen, und dann stellt sich die Frage, wie das Geschäftsmodell weiter funktionieren kann."
Matay Erdinc hat deswegen weitere nachgelagerte Maschinen bestellt, um weitere Arbeitsschritte zu automatisieren. Bald werden nicht mehr Menschen, sondern Maschinen die Masken in die Maschine einlegen, die sie in Plastikhüllen verpackt. Eine weitere Maschine wird die Masken am Ende jeder Produktionslinie in einen Karton verpacken.
"Wir wollen es möglichst automatisiert machen. Bedeutet nicht, dass wir auf die Mitarbeiter verzichten wollen, sondern sie werden dann andere Aufgaben haben. Das dient dazu, dass wir mit China konkurrenzfähig bleiben. Mit Sicherheit werden wir immer ein bisschen teurer sein als die Chinesen, aber wer dann auf Qualität wert legt, wird auch den Preis bezahlen."
Mit China konkurrenzfähig sein
Diese Erfahrung macht auch der Chemieriese Evonik mit seiner Kundschaft aus der Pharmaindustrie. Stefan Randl:
"Der Kunde ist, glaube ich, schon bereit etwas mehr zu zahlen, wenn Dinge aus westlichen Ländern kommen. Wir müssen aber nichtsdestotrotz schon noch konkurrenzfähig sein. Das heißt, wenn wir jetzt, keine Ahnung, zu Mondpreisen anbieten, zwei, drei, vier Mal so teuer wie aus China, dann wird man auch nicht erfolgreich sein."
Längst sind aber auch in China die Kosten wegen Umweltauflagen oder für Arbeitskräfte gestiegen und sie ziehen weiter an - damit verändert sich auch die Kalkulation europäischer Unternehmen.
"Der Unterschied zwischen westlicher und asiatischer Produktion ist natürlich in erster Linie in den Lohnkosten. Wenn man sich die Kostenstruktur mal ansieht, die gleicht sich natürlich auch an, ist jetzt nicht mehr ganz so extrem unterschiedlich, wie sie vielleicht mal vor zehn, 20 Jahren war, aber nichtsdestotrotz sind natürlich Lohnkosten in westlichen Ländern immer noch höher."
Neubewertung der Risiken durch Lieferketten
Unternehmen bewerten infolge der Pandemie auch die Risiken ihrer Lieferketten neu. Beeinflusst wird die Standortwahl auch durch den technologischen Fortschritt. Industrieroboter werden immer günstiger. Wie reagieren Unternehmen auf die steigende Unsicherheit und sinkende Kosten für die Automatisierung? Haben sich die relativen Kosten in den Lieferketten durch die Pandemie verändert? Zu diesen Fragen forscht die Ökonomin Dalia Marin.
"Wir haben jetzt ein Modell, das schätzt für die Vergangenheit, wie sich Schwankungen in der Unsicherheit auf die Lieferkettenaktivität ausgewirkt hat."
Die Daten aus der Pandemie liegen noch nicht vor. Deswegen zieht die Forscherin Daten aus vorherigen Krisen für den Unsicherheitsindex heran. Er stieg während der SARS-1-Virus-Pandemie Anfang der 2000er-Jahre um 70 Prozent, in der Finanzkrise um 250 Prozent. In der jetzigen Pandemie werde der Index schätzungsweise um 300 Prozent ansteigen.
"Wir können jetzt das Modell dazu verwenden, um eine Prognose zu machen, wenn dieser Unsicherheitsindex um 300 Prozent steigt, um wie viel sinken dann die Lieferketten, weil sie kostspieliger geworden sind. Und unsere Schätzung ergibt, dass bei einem Anstieg des Unsicherheitsindex um 300 Prozent, die Lieferkettenaktivität um 35 Prozent sinkt."
Weniger Arbeiter im Ausland, mehr Maschinen in Deutschland
Wie verändert sich der Grad an Automatisierung? Ihr Modell spricht dafür, dass hiesige Unternehmen einen gehörigen Teil ihrer Produktion zurückverlagern könnten und dann weniger Arbeiter in anderen Ländern und mehr Maschinen in Deutschland Waren produzieren würden. Ausschlaggebend dafür sind die aufgrund der Unsicherheit gestiegenen Kosten für Lieferkettenaktivitäten und die gesunkenen Finanzierungskosten für die Automation.
"Besonders ausgeprägt ist dieser Effekt für Deutschland und die USA. Wer das zum Beispiel nicht macht, ist das Vereinigte Königreich, ist Spanien und Italien. Das sind Länder, wo man es nicht sieht."
Außerdem gebe es Unterschiede zwischen Branchen. Für die Automobilindustrie oder die Textilindustrie beobachtet die Forscherin bislang keine Rückverlagerung, anders als etwa in der Chemieindustrie.
Emissionen durch Warentransport
Werden Unternehmen die komplette Wertschöpfung nach Europa zurückholen? Wohl kaum. Zum einen setzen auch Zulieferer an Billiglohnstandorten auf eine Automatisierung. Zum anderen wären damit Wohlfahrtsverluste verbunden. Laut dem Institut für Weltwirtschaft würde beispielsweise der Wohlstand in der EU um 3,6 Prozent sinken, wenn die EU ihre Außenhandelsregeln so ändern würde, dass die Einfuhrkosten für Drittstaaten in die EU sich verdoppeln würden – also ausländischen Anbietern den Marktzugang erschweren würde.
Andererseits sind solche Betrachtungen relativ. Denn eigentlich müsste der Welthandel in einer ähnlichen Größenordnung schrumpfen, wenn die beim Transport entstehenden klimaschädlichen CO2-Emissionen angemessen bepreist würden. Ökonom Felbermayr:
"Vermutlich reden wir da über Größenordnungen von drei bis fünf Prozent, die der Handel zu groß ist, weil die Transportemission nicht internalisiert sind, mit großen Unterschieden über die einzelnen Produkte hinweg."
Einiges spricht dafür, dass es zumindest zu einer gewissen Rückverlagerung und einem Ausbau der Produktion in Industrieländern kommt. So wie bei dem Berliner Maskenunternehmer Erdinc. Halle 7 ist bereits zu klein.
"Wir müssen uns definitiv vergrößern."