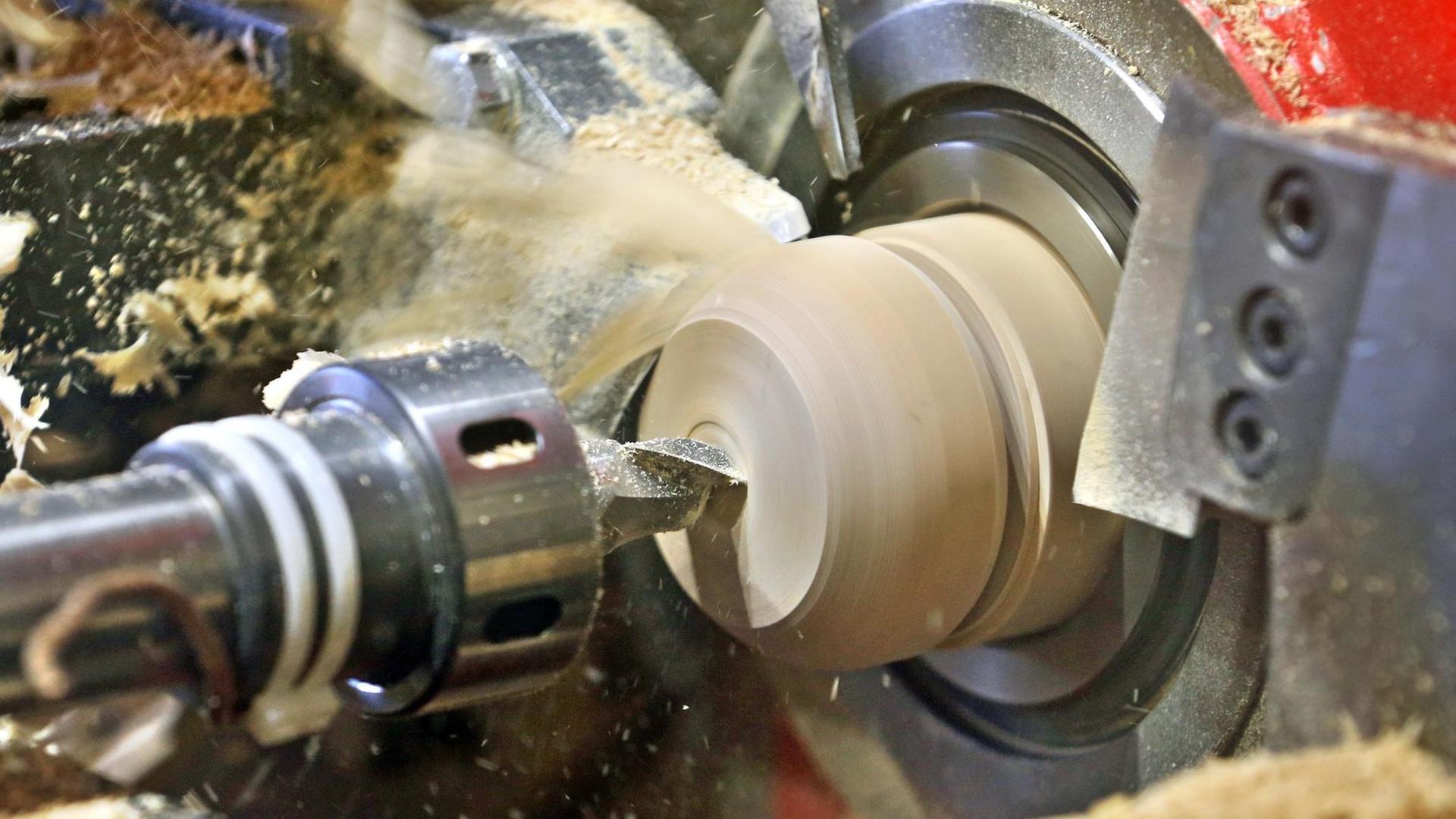
Der schnell rotierende Schneidkopf einer CNC-Fräsmaschine arbeitet sich durch einen Block aus Titan. Was auf den ersten Blick mühelos erscheint, bedeutet für das Fräswerkzeug aus Hartmetall einen Kraftakt – nach einer halben Stunde ist es nicht mehr zu gebrauchen. Denn beim Fräsen von festen Materialien entsteht extreme Hitze, erklärt Marc-André Dittrich vom Institut für Fertigungstechnik und Werkzeugmaschinen an der Leibniz-Universität Hannover.
"Zum Beispiel bei der Bearbeitung von Titanlegierungen haben wir durchaus Temperaturen von bis zu 1.000 Grad Celsius an der Schneide. Und diese hohen Temperaturen reduzieren auch die Festigkeit der Schneidstoffe, sodass sie schneller verschleißen können."
Neue Technik mit weniger Energieverbrauch gesucht
Ein Recycling-Verfahren für verschlissene Fräswerkzeuge gibt es schon länger. Spezielle Mahlwerke zerkleinern dabei das Material zu Pulver. Dieses wird durch das sogenannte Sintern zu meist zylinderförmigen Rohlingen verarbeitet. Daraus lassen sich neue Werkzeuge schleifen.
Die bisherige Technik verbraucht jedoch viel Energie. Darum haben Marc-André Dittrich und sein Kollege Jan Brüning mit anderen Forschern der Universität Hannover, mit der Gesellschaft zur Förderung angewandter Informatik Berlin und mehreren Industriepartnern eine Alternative entwickelt. Sie wollen abgenutzte Bohrer und Fräswerkzeuge umschleifen. Am Anfang steht ein zweigliedriger Analyseprozess, erklärt Jan Brüning:
"Das Eine ist eine Datenhaltung, die wir mitführen müssen, um zu wissen, mit welchem Fräswerkzeug wir es überhaupt zu tun haben. Also aus welchem Material ist es hergestellt worden? Und das andere ist dann eine optische Analyse des Fräswerkzeugs, um darauf rückschließen zu können, was mit diesem Werkzeug passiert ist. Sind beispielsweise Teile der Schneide ausgebrochen? Oder kam es zu einem größeren Bruch?"
Eine optische 3D-Analyse von Werkzeugen ist anspruchsvoll, weiß Niels Heuwold von der Gesellschaft zur Förderung angewandter Informatik in Berlin. Grund ist die glänzend reflektierende Metalloberfläche.
"Dieses Problem lösen wir durch die sogenannte HDR-Technik, bei der wie in der Fotografie mehrere Belichtungszeiten nacheinander genutzt werden."
Datenbank und Umschleifprozess
Damit lässt sich etwa ein Fräser bis auf wenige Mikrometer genau vermessen. Das ist wichtig, um auch kleine Bruchstellen oder Haarrisse erkennen zu können. Schließlich muss die Materialstruktur eines verschlissenen Werkzeugs noch stabil genug sein. Außerdem werden die Gesamtlänge und an mehreren Stellen die Durchmesser bestimmt. Alle diese Werte landen am Ende in einer Datenbank.
"Von jedem hinzukommenden Schrottwerkzeug werden nun ebenfalls diese Parameter bestimmt und mit denen der vorhandenen Werkzeuge in der Datenbank verglichen. Das Werkzeug in der Datenbank, das mit dem geringsten Aufwand hergestellt werden kann, wird über einen Algorithmus in unserer Software ermittelt und für den Umschleifprozess vorgeschlagen."
Somit bedeutet Umschleifen statt Verschrotten natürlich einen erheblich größeren Planungs- und Bearbeitungsaufwand. Trotzdem sei das Verfahren erheblich kostengünstiger als herkömmliches Hartmetall-Recycling, meint Jan Brüning:
"Je näher wir mit dem Zieldurchmesser an dem Ursprungsdurchmesser liegen, desto geringer sind natürlich die Zerspanungsaufwände, die wir haben. Und wir sind tatsächlich in der Lage, bis zu 50 Prozent der Kosten mit dem Verfahren zu sparen."
Verfahren für Werkzeugschleifereien interessant
Interessant wäre das Verfahren vor allem für Werkzeugschleifereien. Bei deren vorhandenen Maschinen ließen sich die neu entwickelte Messtechnik und Software nachrüsten. Aber dann müsste auch noch ein funktionierender Warenkreislauf zwischen Herstellern und Anwendern aufgebaut werden, betont Jan Brüning:
"Beispielsweise wäre hier denkbar, dass ein Werkzeughersteller Leasing-Verträge mit Kunden abschließt. Und dass dann auch sichergestellt ist, dass diese Werkzeuge genauso wieder zu dem Hersteller zurückfließen, damit er dann aus diesem Werkzeug ein neues herstellen kann."