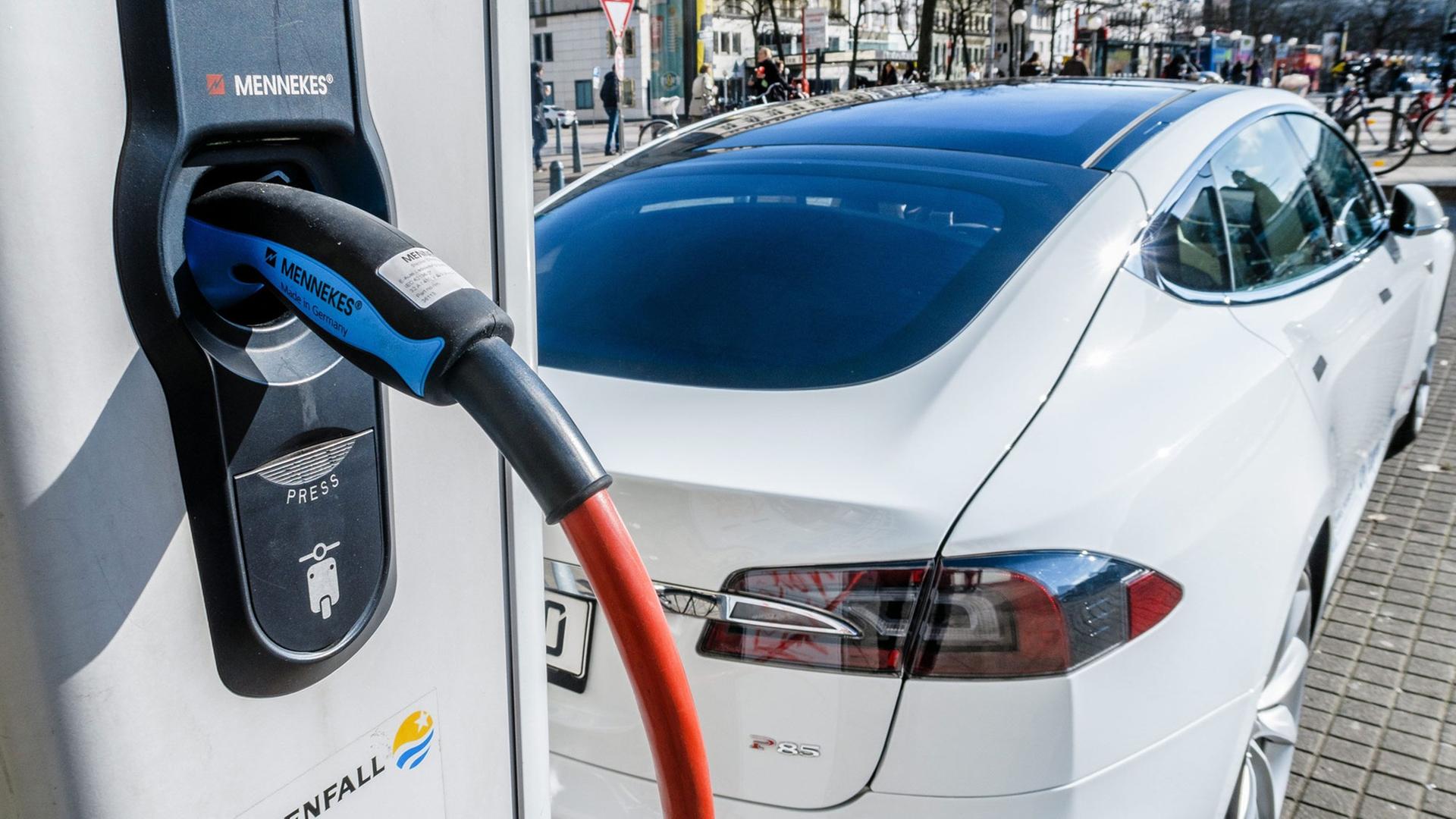
"Das ist jetzt ein System das haben wir entladen und kurzgeschlossen."
Die Restenergie der koffergroßen Lithiumionenbatterie hat Diplom-Ingenieur Jan Diekmann gestern in das Stromnetz der Technischen Universität Braunschweig eingespeist. Nicht nur um die Gewinnbilanz des Recyclings zu verbessern, vor allem um gefährliche elektrische Schläge zu vermeiden. Jetzt, 24 Stunden später, ist die Batterie tiefenentladen und kann gefahrlos von einem Techniker mit Roboter-Unterstützung auseinandergebaut werden.
"Das System besteht eben aus einzelnen Modulen. Hier Batteriemodule, das sind diese hier und dann haben wir hier noch so ein Batteriemanagementsystem, das die ganzen Lade- und Entladeströme steuert. Und das geht dann eben direkt ins Elektronikrecycling und wir nehmen dann diese Module und geben die in unseren Prozess."
Gefährliche Trennung
Denn in den Modulen stecken neben Kupfer und Aluminium auch seltenere Metalle wie Nickel, Kobalt, Mangan und das Lithium, die schon aus Gründen des Umweltschutzes nicht einfach weggeworfen werden sollten. Es ist allerdings nicht einfach, die Module zu recyceln. Die hauchdünnen, beschichteten Elektroden sind umgeben von einer gesundheitsschädlichen Elektrolytflüssigkeit. In Braunschweig setzt man trotzdem auf eine mechanische Trennung. Die Module, groß wie Toaster oder Mikrowellen, werden komplett in einen Industrieschredder gegeben und zerkleinert. Unter Schutzgas, damit sich nichts entzündet. Anschließend werden die Schnipsel getrocknet. Heraus kommt eine Art silbern, kupfern, schwarzes Metallkonfetti.
"Aluminiumfolie, das ist die Substratfolie von der Kathode. Und die Kupferfolie, das ist von der Anodenseite und da sieht man hier auch noch da ist Beschichtung noch drauf, das sind eben die Beschichtungen mit Lithiumübergangmettaloxide, die wir zurückgewinnen wollen."
Die feinen Metallschichten haben sich durch die mechanische Belastung im Schredder voneinander gelöst. Jetzt müssen sie noch sortenrein getrennt werden. Jan Diekmann schaltet den sogenannten Sichter ein: Ein Luftgebläse, dass das Metallkonfetti durch ein Zick-Zack Rohr nach oben pustet.
"Da sieht man eben genau die Trennung nach der Dichte, sprich die leichten Fragmente, die Separatorfolie aus den Batterien aber auch schon frei vorliegende Beschichtung, die sieht man hier hochfliegen. Und alles was Elektrodensammlerfolie ist, also Kupfer und Alusammlerfolie, die fällt nach unten."
Dann wird noch fein gesiebt, am Ende kann Jan Diekmann seine hochreinen Metallfraktionen den Kollegen in der Braunschweiger BatteryLabFactory geben, als Ausgangsstoff für die nächste Generation Batterien.
"Wir konnten schon zeigen, dass wir Materialien in einer Qualität herstellen können, die es eben wirklich ermöglichen, geschlossene Wertstoffkreisläufe zu realisieren, das heißt, aus alten Batteriezellen wieder Neue zu produzieren."
Prof. Christoph Herrmann, Institutsleiter Nachhaltige Produktion & Life Cycle Engineering an der TU Braunschweig, ist stolz auf das Erreichte.
"Wir schaffen mit unserer Recyclinganlage bereits 75 Prozent Recyclingquote, und wir glauben, dass wir auch noch Steigerungspotential haben, so dass wir vielleicht sogar über die 80 Prozent kommen können. Damit sind wir international ganz vorne mit dabei, das ist Spitze."
Noch lohnt es sich nicht
Von 1.000 Euro Materialwert einer Lithium-Ionen-Batterie kann die Anlage zwischen 600 und 700 Euro zurückgewinnen, hat Prof. Thomas Spengler ausgerechnet. Der Wirtschaftsingenieur leitet das Zentrum für Automobilwirtschaft und industrielle Produktion in Braunschweig. Recycling von Batterien von Elektroautos lässt sich hier mit Gewinn betreiben. Theoretisch zumindest, doch es gibt eine große Hürde: die Anfangsinvestitionen.
"Dadurch, dass sich die Elektromobilität nur sehr, sehr langsam in den Markt verbreitet, ist das Aufkommen von Lithium-Ionen-Batterien deutlich geringer als notwendig wäre, um bereits jetzt wirtschaftlich vorteilhaft in diese komplexen Recyclingtechnologien zu investieren."
Jan Diekmann und Christoph Herrmann bleibt also noch Zeit, ihren Maschinenpark zum Batterierecycling weiter zu optimieren.