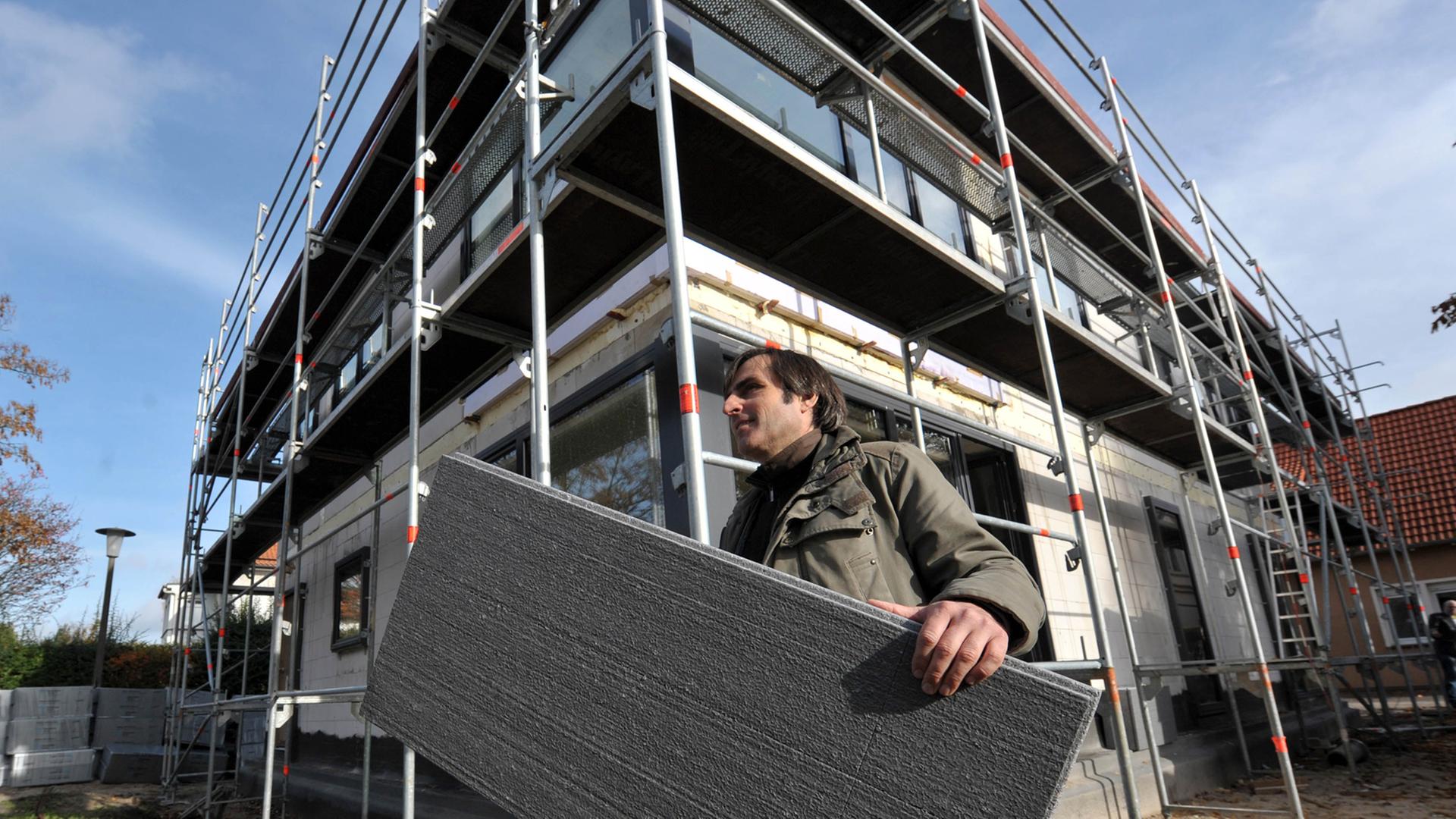
"Jetzt sind wir in unserem Technikum. Wir können vom Holzstamm bis zum Holzschaum alles herstellen. Hier haben wir zum Beispiel Hackschnitzel, die werden zu Holzfasern verarbeitet."
Julia Scholtyssek vom Fraunhofer-Institut für Holzforschung in Braunschweig schüttet die fingerdicken Hackschnitzel in eine spezielle Mühle – den "Kollergang". Zwei schwere Mahlsteine, die wie Räder im Kreis herum rollen, zermalmen das Holz unter Zugabe von reichlich Wasser, bis nur noch eine breiige Masse aus nasstriefenden Fasern übrig bleibt.
"Man sieht, es ist eine braune Paste, was wie Sand am Wattenmeer aussieht. Man hört es, wir haben hier einen hohen Wasseranteil. Der Feststoffgehalt liegt bei etwa zehn Prozent in diesem Fall."
Buchen, Kiefern, Fichten – praktisch alle Bäume, die hierzulande im Wald wachsen, können zu Holzschaum verarbeitet werden. Der Dämmstoff ist luftig leicht, aber auch fest und kann zu stabilen Platten verarbeitet werden – ähnlich dem Styropor. Noch aber ist es nicht soweit. Die nassen Fasern müssen erst noch getrocknet werden. Julia Scholtyssek spricht sogar von "backen", weil die Masse wie ein Kuchenteig in der Backröhre aufgeht. Damit der Brei beim Backen aufschäumt, gibt die Chemikerin - hier in der Leimküche des Instituts - noch ein paar Tropfen Wasserstoffperoxid als Treibmittel hinzu. Sie trägt dabei eine Schutzbrille – die wässrige Lösung ist extrem ätzend.
"Jetzt wird das Ganze verrührt. Wir starten mit 500 Umdrehungen pro Minute und gehen dann bis auf 1000 Umdrehungen."
Im heißen Trockenschrank zersetzt sich das Wasserstoffperoxid in Wasser und gasförmigen Sauerstoff, der die Holzfasermasse aufschäumt.Scholtyssek:
"Wir haben jetzt die Holzfasersuspension mit dem Schäumungszusatz in eine Form gegeben und stellen das jetzt für mehrere Stunden zum Trocknen in den Trockenschrank bei 90 Grad. Der Trocknungsprozess wird in diesem Fall voraussichtlich etwa sechs Stunden dauern. Das ist noch relativ lang. Und das ist eine der künftigen Ideen, dass wir diese Zeit gerne verkürzen möchten."
Beim Trocknen beziehungsweise Backen verdampft das Wasser und das Material wird luftig und porös. Gleichzeitig verkleben die winzigen Fasern, weil die im Holz enthaltene Stärke alles fest miteinander verbindet. Chemische Zusätze sind also unnötig. Am Ende hält Julia Scholtyssek einen leichten, aber fest und stabil wirkenden Schaumstoff in der Hand, dem man die Herkunft aus dem Walde nicht mehr ansieht: Holzschaum.
"Die meisten Dämmstoffe - basierend auf natürlichen Rohstoffen - die sind wenig druckfest, die sind nicht sehr stabil. Und jetzt war die Idee, ein Isolationsmaterial oder ein Dämmstoff oder auch ein Verpackungsmaterial zu entwickeln, das sich ähnlich wie konventionelle Schaumstoffe anfühlt und dabei aber nachhaltige Rohstoffe genutzt werden."
Platten aus Holzschaum könnten – so wie Styropor - direkt auf die Hauswand geschraubt und geklebt werden. Mit Hanf, Flachs oder Wolle geht das nicht. Diese Dämmstoffe wären dazu einfach zu weich, so die Wissenschaftlerin.
"Wir sehen hier, dass wir relativ stabile Schäume herstellen können, druckfest, sie fusseln nicht, sie fasern nicht, das sind die größten Vorteile gegenüber den sehr weichen und sich verformenden Materialien."
Den Wasseranteil zu senken, auch das spezifische Gewicht, um die Platten leichter zu machen, darauf zielen die weiteren Forschungen ab. Auch die Industrie zeigt sich interessiert. Bis der Holzschaum im Handel ist, wird es aber trotzdem noch eine Zeit dauern.