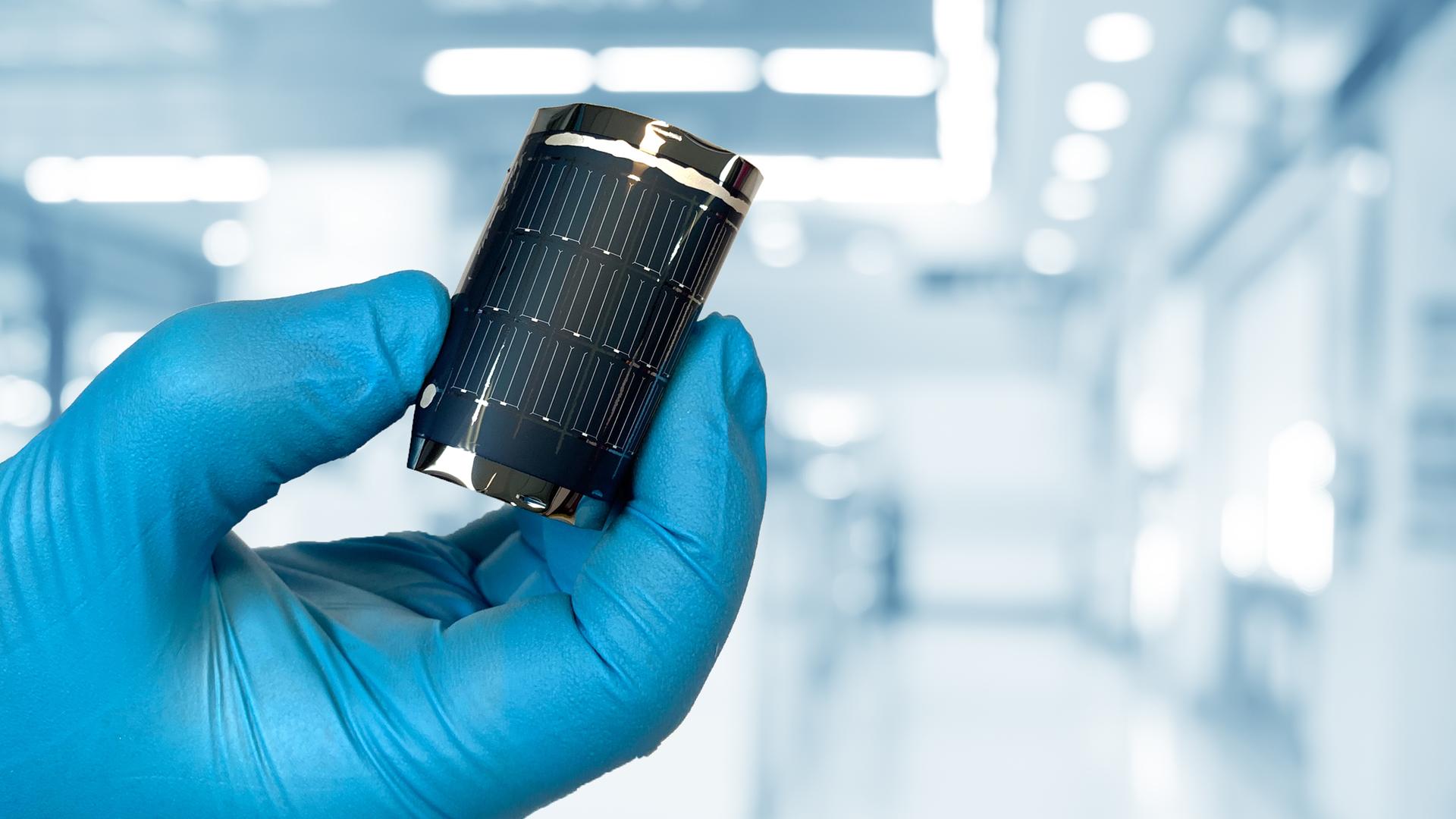
Ayodhya Nath Tiwari von der Schweizer Forschungsanstalt EMPA erinnert sich noch gut an seine erste Solarzelle auf Plastikfolie. Sie war kleiner als seine Fingerkuppe und die Performance lausig. Aber sie funktionierte! Sein Plan war, aus der Minizelle ein Massenprodukt zu machen: leichte, biegsame Solarzellen auf kilometerlangen Plastikbahnen, produziert im sogenannten Rolle-zu-Rolle-Verfahren. Wie diese Solarzellen aufgebaut sind, erklärt der EMPA-Forscher Romain Carron: “Es ist ein Sandwich aus vielen verschiedenen Lagen. Am wichtigsten ist die Schicht, die das Licht absorbiert."
Die Schicht besteht aus fast schwarzem Kupfer-Indium-Gallium-Diselenid, oder kurz: CIGS. Und sie ist hauchdünn, etwa fünfzigmal dünner als ein Menschenhaar. “Diese Schicht fängt die Lichtteilchen ein und verwandelt sie in elektrische Ladungsträger. Außerdem brauchen wir noch elektrische Kontakte vorne und hinten, um die Ladungsträger zu trennen und einen Strom fließen zu lassen", erklärt Romain Carron. Hinzu kommen zwei Zwischenlagen und eine Deckschicht, die vor Wind und Wetter schützt.
Problem Massenproduktion
Der Vorteil dieser und ähnlicher Dünnschichtsolarzellen: Sie können an Fassaden, auf Fahrzeugen, Dächern und Gestellen Strom erzeugen, für die gängige Silizium-Solarmodule schlicht zu schwer und sperrig sind. Die Produktion von der Rolle verspricht zudem hohe Durchsätze und damit niedrige Kosten. Kein Wunder also, dass die Idee nicht nur das Team aus der Schweiz faszinierte. Schon Anfang der 2000er-Jahre wurden erste Fabriken gebaut. Doch der Durchbruch blieb aus.
„Das ist natürlich sehr, sehr schwierig, wenn man sowohl ein neues Verfahren entwickelt, als auch das auf die Rolle-zu-Rolle im Quadratmetermaßstab, mit hohen Durchsätzen und so weiter, transferiert. Da gibt es einige Firmen, die daran gescheitert sind, nämlich an dem Hochskalierungsprozess", sagt Michael Powalla vom Zentrum für Sonnenenergie- und Wasserstoff-Forschung in Stuttgart.
Zum Beispiel das Start-Up-Unternehmen Nanosolar in Kalifornien, in das Risikokapitalgeber hunderte Millionen investiert hatten, bevor es 2013 Pleite ging. Die Kosten hätten eine Rolle gespielt, dass die Vorreiter gescheitert seien, aber auch technologische Hürden, erklärt Powalla. Hohe Produktionstemperaturen zum Beispiel können den Zusammenhalt der Lagen beeinträchtigen. Und die Trägerfolien aus Plastik oder Metall sind für die hauchdünnen lichtaktiven Schichten oft zu rau: „Sie müssen sich das so vorstellen: Die dünnen Schichten sind ein, zwei Mikrometer groß und wenn die Rauigkeit mehrere 100 Mikrometer ist, ist es so ein bisschen wie der Schnee auf einem großen Gebirge, der also sehr schwer zu einer geschlossenen Schicht dann zusammenwächst.“
Das Team aus der Schweiz will mittlerweile viele Probleme gelöst haben. Dabei half die enge Zusammenarbeit mit dem Startup Flisom, das seit 2005 eine Pilotanlage betreibt. Aktuell laufen dort bis zu drei Meter lange Solarzellbahnen von der Rolle. Längere Bahnen seien aber kein Problem, sagt Romain Carron: “Die Rolle ist einen Meter breit und kann ein oder zwei Kilometer lang sein."
Das Start-Up Flisom hat kürzlich außerdem eine Industrieanlage in Ungarn in Betrieb genommen, die CIGS-Solarzellen Schritt für Schritt am Markt etablieren soll. Auch die junge Firma Heliatek in Berlin hat eine kleine Serienproduktion gestartet. Das Unternehmen setzt auf organische Solarzellen, die fast ausschließlich Kohlenstoffverbindungen enthalten, was sie laut Hersteller besonders nachhaltig macht.
Stabilität und Wirkungsgrad
Ebenfalls für die Rollenproduktion geeignet ist eine Art Newcomer der PV-Branche: Perowskit. Das Material muss zwar noch stabiler und idealerweise bleifrei werden. Doch dann könnte es nicht nur solo, sondern auch als zusätzliche Lage im Solarsandwich aus der Schweiz dafür sorgen, dass möglichst viel der einfallenden Lichtenergie in Strom verwandelt wird.
Romain Carron: “Zurzeit liegt der Wirkungsgrad bei 21 Prozent. Wahrscheinlich können wir noch 22 oder 23 Prozent erreichen, aber viel mehr wohl nicht. Deshalb versuchen wir jetzt, verschiedene Technologien zu kombinieren. Und da haben wir auch schon sehr gute Ergebnisse: mehr als 25 Prozent Wirkungsgrad."
Das gilt allerdings nur für Solarzellen aus dem Labor. Im industriellen Maßstab von Rolle zu Rolle produziert, liegen die Wirkungsgrade der CIGS-Zellen zwischen zehn und 14 Prozent. Zum Vergleich: Gängige Siliziummodule bringen rund 20 Prozent. Allerdings hatten sie auch einen längeren Vorlauf. Die ersten Solarzellen aus Silizium wurden 1954 präsentiert.