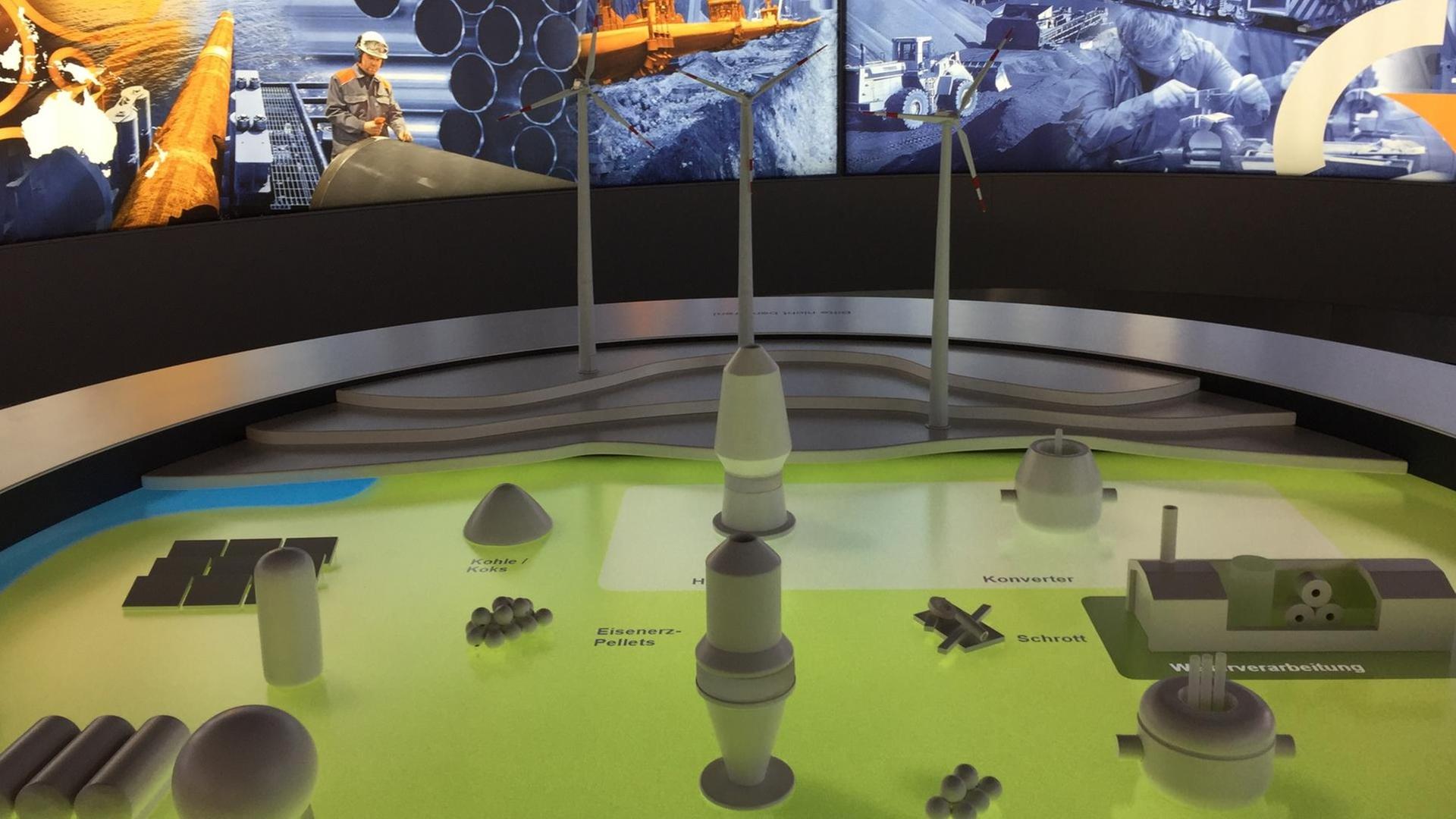
„Das ist der Abstich. Das flüssige Roheisen fließt aus dem Hochofen raus. Dies ist im Grunde genommen das erste greifbare Produkt auf dem Wege der Herstellung von Stahl für Kühlschränke, Automobile und Brücken.“
Heinz Jörg Fuhrmann steht vor dem Hochofen. Der Chef der Salzgitter AG schaut zu, wie ein Arbeiter im Schutzanzug eine Probe nimmt. Bei der heutigen Stahlherstellung wird Kohle benutzt, um den Sauerstoff aus dem Eisenerz zu entfernen. Dieses wird im Hochofen zugleich aufgeschmolzen. Es ist die produktivste und kostengünstigste Methode, um Roheisen zu gewinnen. Dabei entsteht das Klimagas CO2 – allein in Salzgitter sind es jährlich acht Millionen Tonnen. Ein Problem insbesondere für die heimischen Produktionsstandorte, klagt Fuhrmann: „Die europäischen Stahlhersteller müssen mit rasant steigenden Kosten durch den Zukauf von Verschmutzungsrechten aus dem EU-Zertifikatehandel rechnen.“
Treibhausgas lieber vermeiden
Mit ein Grund, warum die Salzgitter AG nun mit ihrem Pilotprojekt SALCOS darauf setzt, das Treibhausgas lieber zu vermeiden. Möglich wird das durch eine veränderte Produktionsweise: Bei der so genannten Direktreduktion wird der Kohlenstoff – vereinfacht gesagt – durch Wasserstoff ersetzt, der mit dem Sauerstoff aus dem Eisenerz reagiert. Projektleiter Volker Hille:
„Wenn man das mit Kohlenstoff tut, entsteht eine Verbindung aus Kohlenstoff und Sauerstoff: das Kohlendioxid, das heute eben ein so großes Thema ist. Wenn man das mit Wasserstoff tut, entsteht eine Verbindung von Wasserstoff und Sauerstoff, die wir alle gut kennen und die wir dringend brauchen, nämlich Wasser.“
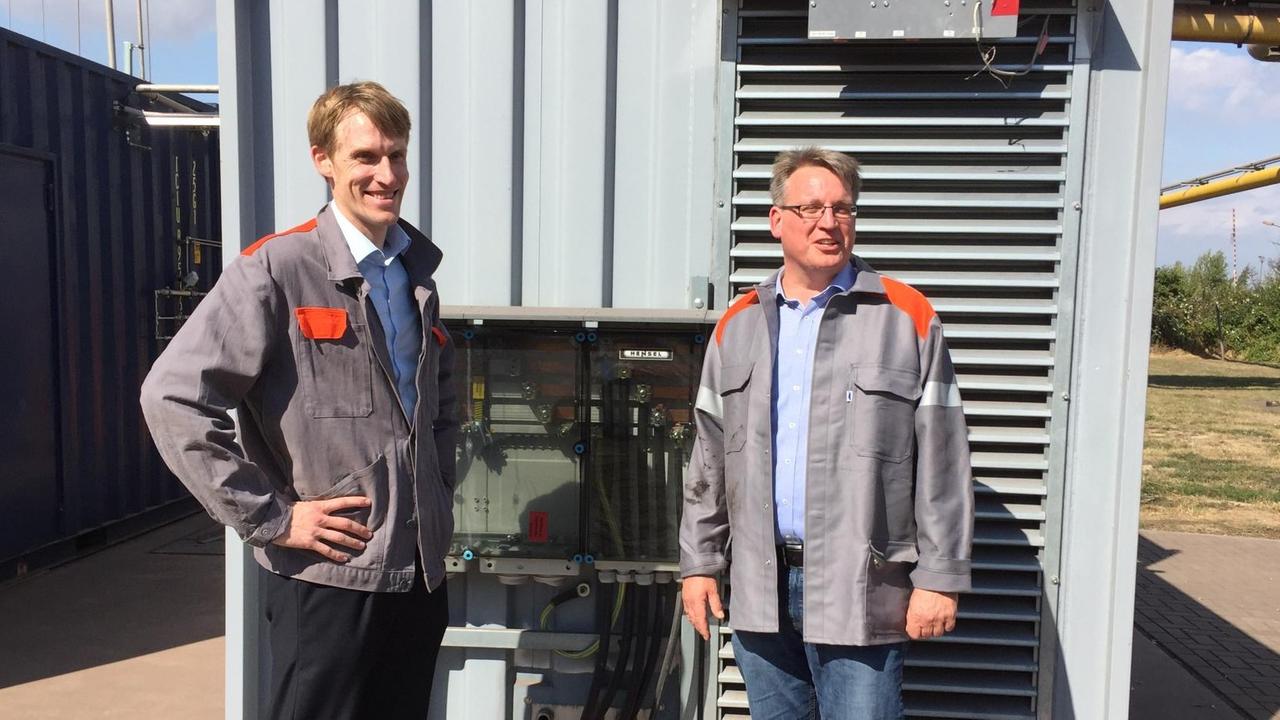
Kohlenstoff aus dem Produktionsprozess verbannen
Den Wasserstoff holt man sich derzeit noch über den Umweg Erdgas, dessen Hauptbestandteil Methan viel Wasserstoff enthält. Doch die Planer in Salzgitter setzen darauf, den Kohlenstoff ganz und gar aus dem Produktionsprozess zu verbannen: In Zusammenarbeit mit Fraunhofer Instituten erforscht die Projektgruppe um Hille, wie sich das Erdgas in weiteren Schritten stufenweise durch sogenannten grünen Wasserstoff ersetzen lässt – also Wasserstoff, der mittels Elektrolyse aus Windstrom erzeugt wird. Hier kommt ein anderes Forschungsprojekt ins Spiel, an dem die Salzgitter AG beteiligt ist: „Hier sind wir an der Green Industrial Hydrogen-Versuchsanlage!“
Alexander Ridenius, Konzernforschung. Noch passt die Versuchsanlage zur Erzeugung von grünem Wasserstoff in zwei unscheinbare Industriecontainer. Ridenius müsste für den Wasserstoff-Einsatz in industriellen Prozessen noch reichlich aufstapeln – an der technischen Machbarkeit zweifelt er nicht:
„Elektrolyse ganz einfach gesprochen, ist ja, wie man vielleicht aus dem Physikunterricht noch kennt: man hat zwei Elektroden, hält die ins Wasserglas – und dann entsteht auf der einen Seite Wasserstoff und auf der anderen Seite Sauerstoff. Das machen wir hier auch, mit einem etwas anderen Prinzip, das nennt sich Hochtemperatur-Elektrolyse. Wir haben die Möglichkeit, hier Dampf einzubinden, deswegen haben wir auch einen höheren elektrischen Wirkungsgrad.“
Strombedarf wird rasant ansteigen
Durch die Umstellung auf Direktreduktion – zunächst mit dem Vehikel Erdgas, später dann mit „grünem“ Wasserstoff – wird der Strombedarf rasant ansteigen. Dabei wird das Eisenerz nämlich direkt in festem Zustand in metallisches Eisen umgewandelt. Zur Weiterverarbeitung müssen diese porösen Klumpen in neu zu errichtenden Lichtbogenöfen geschmolzen werden – auch das frisst Strom in rauen Mengen. Der geplante Umbau eines bestehenden Hüttenwerks bei laufender Produktion ist ein weltweites Novum, sagt Projektleiter Hille:
„Ganz konkret müssen wir Möglichkeiten schaffen, diese enorm gestiegenen Mengen an Erdgas hierherzubringen, wir müssen da Pipelines für bauen. Der Elektrolichtbogenofen ist einzubinden in die Stoffströme im Stahlwerk. Wir müssen den Strom herbringen, und zwar aus erneuerbaren Energien, wir brauchen die Verbindung zu den Windparks …“
Könnte die gesamte Stahlproduktion umgestellt werden, ließe sich der CO2-Ausstoß laut Modellrechnungen bis 2050 um bis zu 95 Prozent reduzieren. Doch schon für die erste Ausbaustufe, von der sich die Salzgitter AG eine Verminderung um 25 Prozent verspricht, müsste das Unternehmen mehr als eine Milliarde Euro investieren. Konzernchef Fuhrmann wirbt in Berlin und Brüssel für Subventionen.
„Wir hätten den Mut, das anzugehen, wenn die Rahmenbedingungen stimmen.“
Für die Erzeugung von Wasserstoff kommt in erster Linie Strom in Frage, der bei starkem Wind nicht anderweitig verwendet werden könnte. Doch der wird bei weitem nicht ausreichen. Und dann sind da noch die Kosten durch die EEG-Umlage.
Für die Erzeugung von Wasserstoff kommt in erster Linie Strom in Frage, der bei starkem Wind nicht anderweitig verwendet werden könnte. Doch der wird bei weitem nicht ausreichen. Und dann sind da noch die Kosten durch die EEG-Umlage.
Deutschen Umwelthilfe begrüßt Projekt
Wird SALCOS realisiert? Peter Ahmels, Energieexperte der Deutschen Umwelthilfe (DUH), begrüßt das Pilotprojekt allen Hindernissen zum Trotz grundsätzlich. Die Umweltorganisation spricht sich auch für eine Unterstützung aus öffentlichen Mitteln aus: „Auf jeden Fall ist so eine Technologie, gleich zu Beginn schon zu vermeiden, dass solche Stoffe wie CO2 überhaupt erst entstehen, wesentlich sinnvoller, als zu versuchen, hinterher das CO2 irgendwo in der Erde zu verpressen oder umzuwandeln oder sonst wie damit umzugehen. Und wir werden am Ende 2050 alle Prozesse und alle Kreisläufe und alle Möglichkeiten nutzen müssen, um halbwegs vom CO2-Output runter zu kommen.“