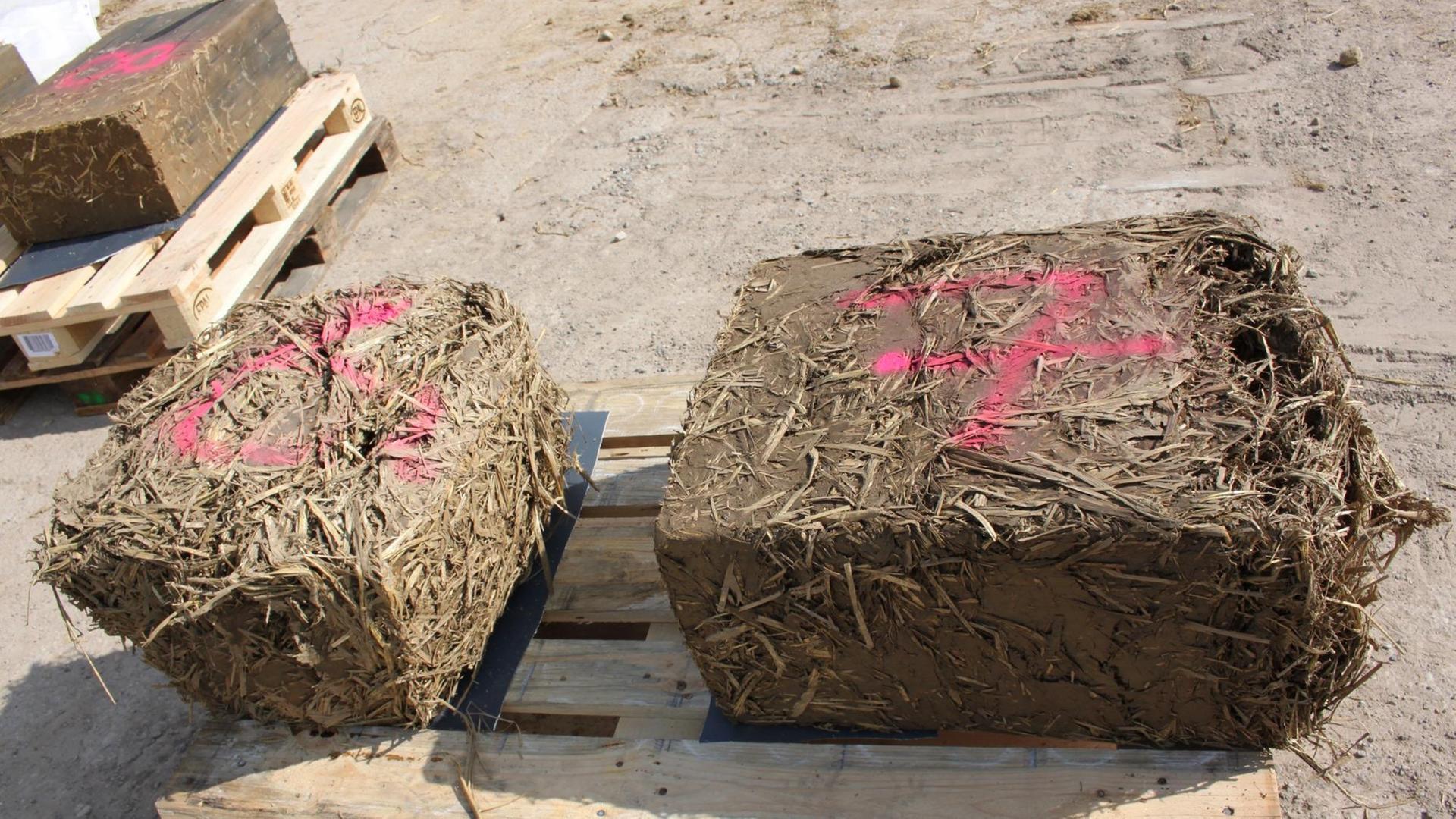
Ein Kieswerk im idyllisch gelegenen Perleberg in Brandenburg. Heiner Lippe von der Technischen Hochschule Lübeck zückt seinen Taschenrechner: "0,28 mal 0,48 mal 0,7 mal 1800: Wenn der trocken ist, wiegt der ungefähr 170 Kilo der Block. Es war eigentlich geplant , dass wir 20 Blöcke schaffen heute."
Die Rede ist von reisekoffergroßen Klötzen aus Wellerlehm, einer feuchte Mischung aus Lehm und Stroh, mit der in Deutschland schon vor Jahrhunderten gebaut wurde. Um die Klötze zu fertigen, schaufeln die Forschenden aus Lübeck und Projektpartner aus der Region verschiedene Mischungen in Eimer und kippen diese dann in eine Hydraulikpresse. Ein Stahlstempel drückt das Material mit 200 bar zusammen.
"Also heute geht es vor allen Dingen drum, dass wir den Lehm in verschiedenen Zusammensetzungen, also mit verschiedenen Rezepten, höherer Strohgehalt, geringerer Strohgehalt, testen, wie er sich in der hydraulischen Presse verhält."
Auf die richtige Zusammensetzung kommt es an
Auch die Feuchtigkeit der Mischungen wird bestimmt. Es gilt, die optimale Wellerlehm-Rezeptur für eine Lärmschutzwand an einem geplanten Abschnitt der A14 zu finden. Die Maße: 570 Meter lang und sieben Meter hoch. Die Schallschutzelemente könnten direkt vor Ort aus dem Aushub für die neue Autobahn gefertigt werden. Wellerlehm, das haben erste Tests gezeigt, schluckt den Schall ähnlich gut wie Beton. Und er hat weitere Gemeinsamkeiten.
"Es ist letztendlich wie ein Stahlfaserbeton. Und das ist ja das Spannende, das genau diese Strohhalme die Armierung bewirken. Wenn es trocknet und es möchte sich auseinanderziehen, dann halten die Fasern das fest."
Dabei gilt: Je mehr Ton im Lehm steckt, desto mehr Stroh verträgt die Mischung. Denn der Ton wirkt als Bindemittel, wie der Zement im Beton. Gegenüber diesem hat Wellerlehm vor allem zwei Vorteile. Er lässt sich klimafreundlicher herstellen und zu 100 Prozent recyceln. Und Wellerlehm ist selbsttragend, benötigt keine Stützen oder Verschalung, anders als der heute schon recht gängige Stampflehm. Der Grund für sein Nischendasein trotz aller Vorteile: Der traditionelle Wandaufbau ist wohl nur was für Überzeugungstäter, sagt Heiner Lippe.
"Das hat man früher gemacht, indem man mit Eichenknüppeln draufgeschlagen hat, sodass die Luft rausgeht. Dann hat man die Lage trocknen lassen. Dann hat man am nächsten Tag oder am nächsten Tag, je nach Trocknungsfortschritt, die nächste Lage aufgetragen. Zuvor hat man aber ein Brett auf diese etwas grobe Wand gelegt, in der zukünftigen Wanddicke, hat sich auf das Brett gestellt und hat an den Zehenspitzem vorbei am Brett lang die Wände glatt abgestochen."
Sind auch größere Gebäude aus Wellerlehm vorstellbar?
Die neue Methode, Wellerlehmelemente mit einer Presse vorzuproduzieren und vorzutrocknen, soll das Material nicht nur für Lärmschutzwände interessant machen. Den Ergebnissen erster Drucktests zufolge könnten daraus auch Häuser gebaut oder aufgestockt werden.
"Das ist auf jeden Fall so, dass wir damit auf jeden Fall unsere geplante fünf oder sieben Meter hohe Wand bauen können, die Lehmlärmschutzwand. Und wenn man davon ausgeht, sieben Meter: Eine Geschosshöhe liegt ungefähr so bei zwei Meter fünfzig, zwei Meter siebzig, da kommen wir allemal mit Lehm hin."
Für Hochhäuser ist der etwa zehnmal druckfestere Beton das tauglichere Material. Eine Raststätte aus Wellerlehm sei aber denkbar, sagt die Künstlerin und Initiatorin des Projekts Ute Reeh. Ob Wand und Gebäude tatsächlich gebaut werden, bleibt abzuwarten. Denn der Lehmbau ist zurzeit noch teurer als konventionelle Baumethoden. Mit den optimierten Wellerlehmrezepten aus den Kieswerktests aber rechnet das Team schon in ein paar Monaten.
"Und wenn wir dann praktisch das richtige Mischungsverhältnis gefunden haben, das richtige Verfahren und die richtige Feuchtigkeit, dann können wir uns spezialisieren und nochmal eine kleine Testreihe machen und dann praktisch tatsächlich auf eine Baustelle gehen, auf den Bau, die Lehmlärmschutzwand machen oder was dann auch immer damit geplant wird."